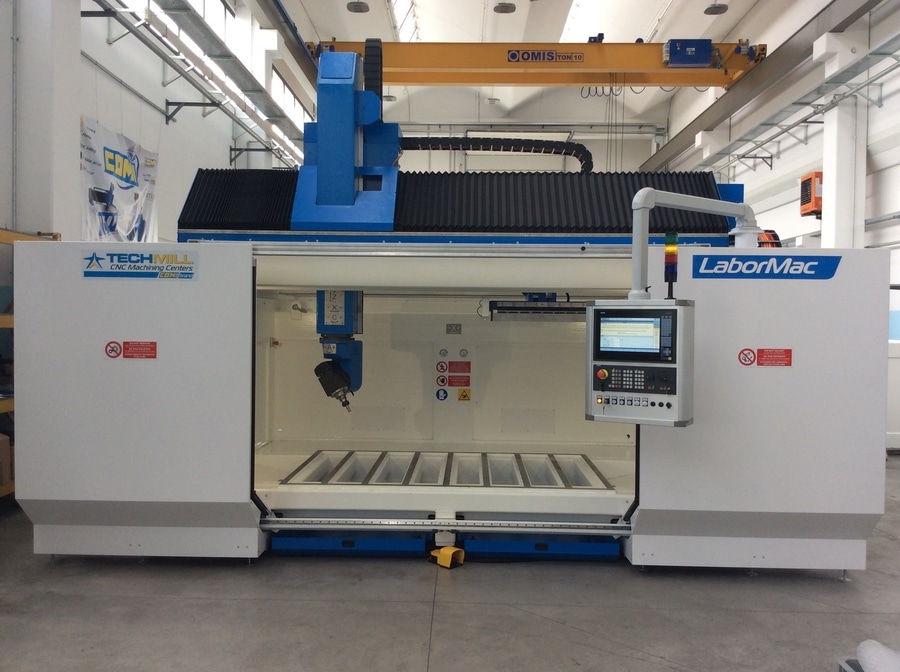
#Industry News
The state-of-the-art 5-axis CNC centers technologies compares with milling of composites
COMI/TechMill launches a new model
The increasing use of composite materials in diversified industrial sectors has created the need for 5-axis CNC machining centers that are capable to combine high productivity with high precision, to reduce workpiece management time, and to address operator safety issues.
Focusing on these goals engineers from the COMI group have optimized the configuration of the new CNC TechMill brand machine called LaborMac.
Ensure high productivity and high precision
Extreme rigidity goal has led to the adoption of a Gantry-type mobile portal on the Y axis, which significantly limits vibration by providing high-quality finishes even at high speeds. For composite part requiring maximum accuracy of milling, TechMill promotes the use of advanced measurement systems such as inductive lines on linear axes and direct encoders on rotating axes.
Being the core technology of any CNC milling machine, TechMill designs all its working heads internally and combine them with electro-spindles that deliver the maximum efficiency for the specific materials, size and workpiece geometry. The LaborMac aluminum head with 2 continuous interpolated axis transmits the movement to the rotating axes (A and C) by means of servomotors connected to high-precision gearboxes and absolute encoder systems, while to optimize performance on composite materials was chosen a 15 kW electro-spindle (S1) - 12 Nm torque that can operate up to 24,000 rpm, provided with 4 high-precision ceramic bearings.
Reduced workpiece management time
Thanks to the large opening of the pneumatic doors, it is easy to access the working table where the axis strokes allow milling of parts up to 2000 x 1000 mm and height of 750 mm.
To operate in masked time TechMill studied a palletized rotating table system that allows to load and prepare a new piece outside the machine without ever stopping it.
Another area of attention is the blockage of the pieces, so modern equipment is developed to quickly and efficiently mount parts of complex geometry on the working table.
Dust containment and extraction
Increasing attention is increasingly being given to operator safety, which leads companies to require dust containment and extraction systems.
The modern retractable folding roof greatly limits the escape of dust and carbon fiber / glass chips, composite material and lubricating fluid developed during the part machining, while ensuring the brightness inside the machine.
The CNC working center are then equipped with systems designed for conveying, extracting and filtering the dust, finally determines the level of individual protection from harmful dust and from the risk of explosion.