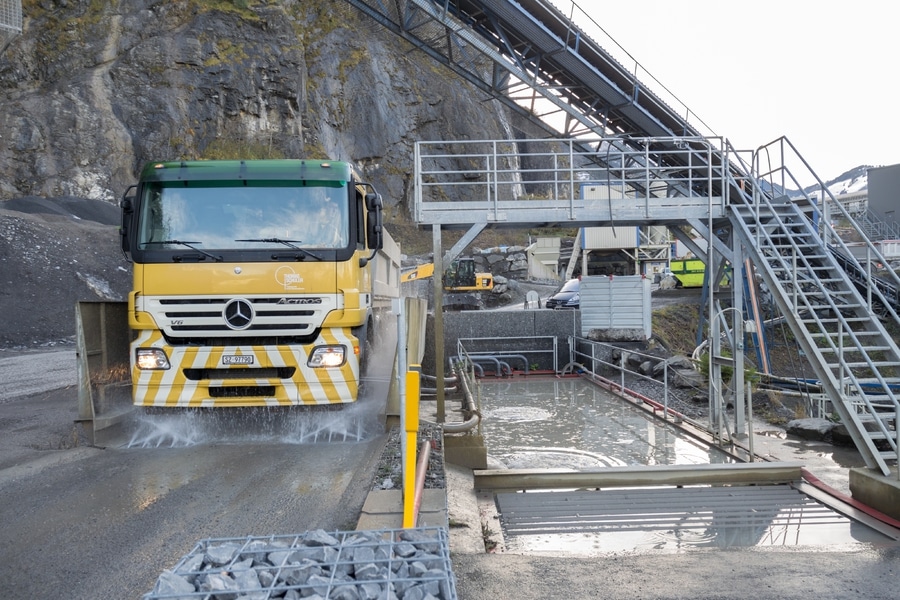
#Product Trends
MobyDick solves site emission problems
Wheel Washing, Dust Control and Demucking Systems
Filthy roads, dust pollution and dirt adhering to vehicles is part and parcel of everyday routine at many landfill sites, material transshipment points, recycling yards, construction sites and recovery plants. As a result, many responsible companies are increasingly looking for opportunities to reduce the negative effects of such emissions on people, the environment and machinery. As a global market leader in the field of emission control, FRUTIGER has been providing a broad range of modern and practical solutions from a single source for over 30 years.
Tyre washing systems solve the problem of dirty public roads
With up to 10 kilograms of dirt on wheels and chassis, thousands of trucks travel daily from contaminated areas onto pubic roads, thereby causing dangerous levels of dirt on the road surface. Thanks to the MobyDick technology along with expertise from over 4000 installed tyre washing systems, however, the tyres and chassis of construction vehicles can nowadays be cleaned simply and cost-effectively before departure. Depending on the level of dirt, various technologies and systems are used. As a rule, a distinction can be made between roller and drive-through systems. In the case of roller systems, the truck drives onto the system and positions the wheels between the rollers. The washing process is then activated by a start bracket. At the same time, the wheel is automatically turned and cleaned by the water that sprays out from numerous nozzles. The advantage here lies in the very good cleaning result, although about 2-3 minutes time is required for each washing process. In response to this, FRUTIGER developed the world's first drive-through system MobyDick® Quick in 1996, this superseded by the MobyDick® ONE in 2016. In a drive-through system, there is no longer any need to stop for tyre cleaning. Once the truck passes the light sensor at the entrance, the washing process is automatically activated. During the slow drive-through (crawling speed), the tyres and chassis are cleaned by water that is sprayed out of numerous nozzles (spray boom). The wash water flows automatically back into the system during the cleaning process, where the automatic reprocessing for the next washing process occurs. The mud accumulating as a result of this is removed by an integrated chain conveyor or excavator and can be disposed of easily. Depending on the amount of dirt and truck frequency, differently sized systems from 3.50 m (one wheel revolution) up to 20.00 m (six wheel revolutions) are used.
Demucking systems clean very dirty construction vehicles within minutes
In contrast to tyre washing systems, a demucking system does not involve keeping public roads clean, but instead automatically removing coarse dirt from the chassis, underbody as well as wheels or tracks of construction vehicles within just a few minutes. In this regard, the washing system is able to clean tracked vehicles up to the size of a Caterpillar D11, but also dumpers and wheel loaders, depending on customer requirements. This technology is also used in a zinc mine in India, for instance. As is common in most opencast mines, a huge fleet of service and construction vehicles ensures smooth operation here too. These vehicles are continually exposed to high levels of dirt, especially during rain. Lumps of earth stick to the axles and chassis, thereby increasing fuel consumption and causing damage. Until recently, the vehicles were washed laboriously using high-pressure cleaners before service work. An unpopular and time-consuming task! To combat this problem, a MobyDick® demucking system was installed. Thanks to this solution, the entire fleet can now be cleaned regularly without major effort. A complete wash of the front, side and chassis takes just a few minutes and the vehicles can be used again straight away. This saves resources, places less of a burden on the environment and contributes towards improving working conditions on site.
Dust control systems reliably bind dust emissions in the air
Parallel to the increasingly stricter air pollution control regulations in many Western countries, along with new insights regarding the harmful effects of dust on the human organism and the environment, the demand for effective dust binding solutions has also intensified in recent years. As a result, tyre washing systems were also used increasingly for dust suppression in the past, which however meant that all problems associated with dust emissions could not always be solved effectively. FRUTIGER Company AG has therefore been providing a broad portfolio of dust binding solutions from the MobyDick® dust control line for several years. The modern dust binding systems work according to the principle of dust binding via ultrafine water droplets. In contrast to earlier systems, which produce large or differently sized droplets with low-pressure pumps, high-quality medium-pressure and high-pressure pumps between 20 - 100 bar are increasingly utilised today, these creating a water mist with a high number of tiny water droplets via special nozzles (50μ to 150μ in outdoor application and 20μ to 80μ for indoor application). Smaller water droplets work more efficiently as – besides their greater number and homogeneous size – they also remain in the air longer owing to the lower flight and fall velocity. This results in a low suction effect around the droplets, causing them to bind frequently with dust particles and allowing these to drop to the ground. The proven technology makes it possible to utilise the water used very efficiently for dust binding.
Home in Switzerland, at home in the world
With its headquarters in Switzerland along with ISO-certified production plants in Europe and Asia, an assembly centre in the USA, as well as an international network of service and sales offices, FRUTIGER is represented with MobyDick specialists throughout the world. For further information visit www.mobydick.com.
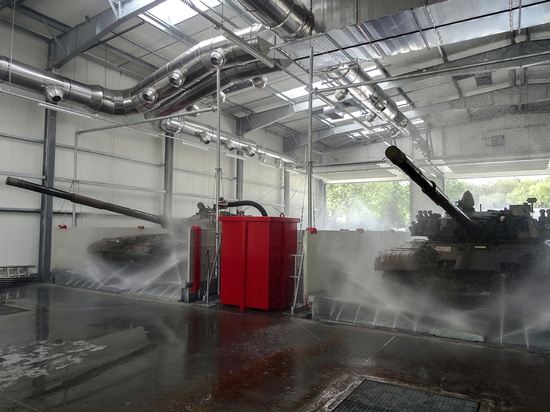
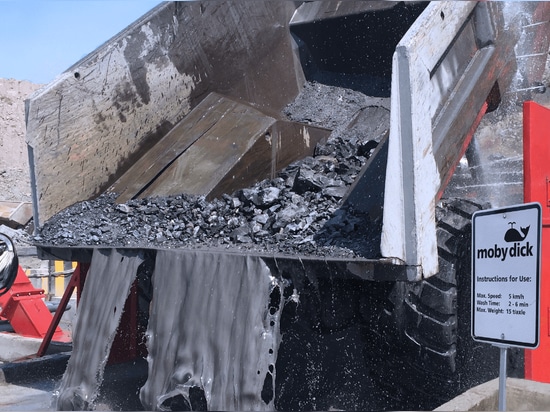
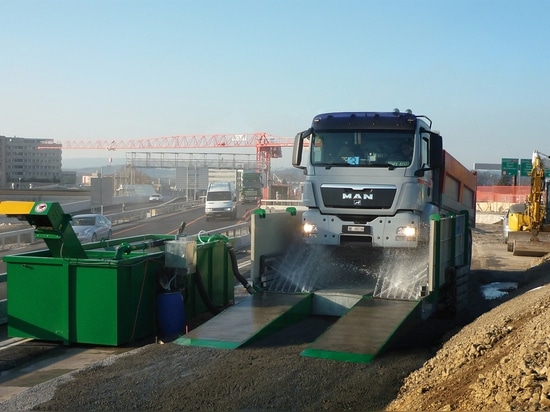
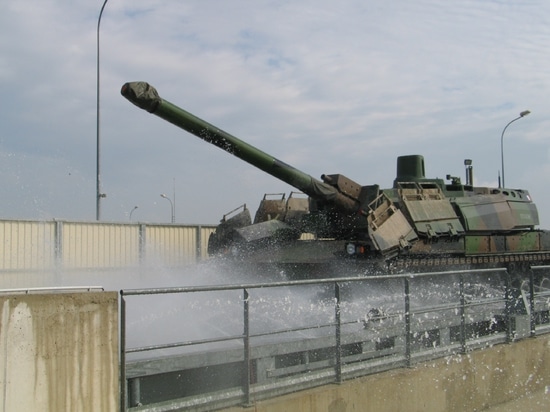
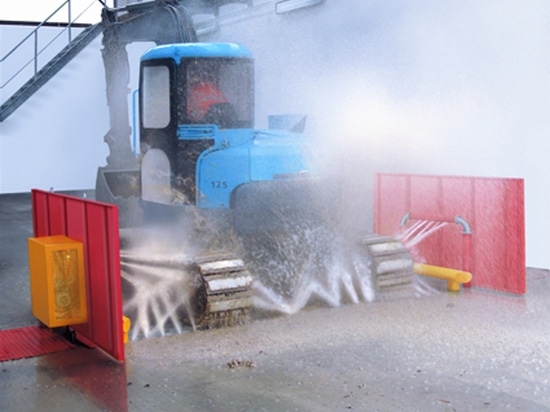
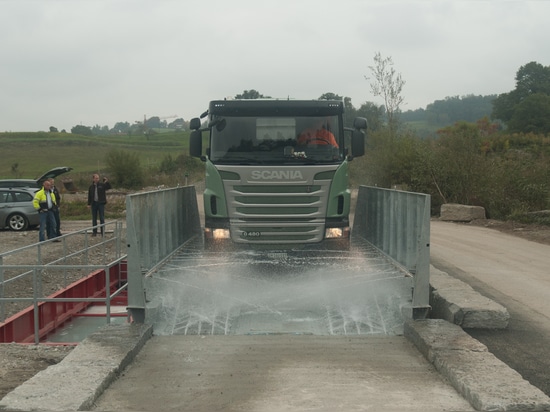
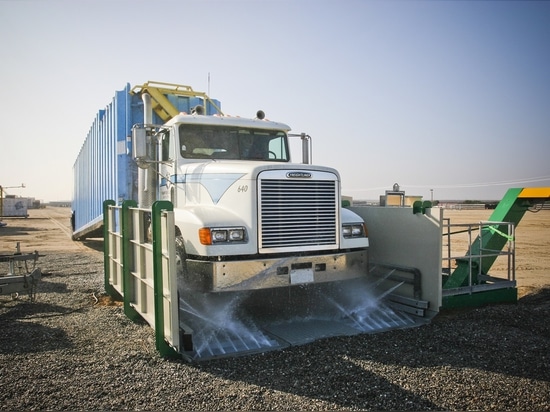