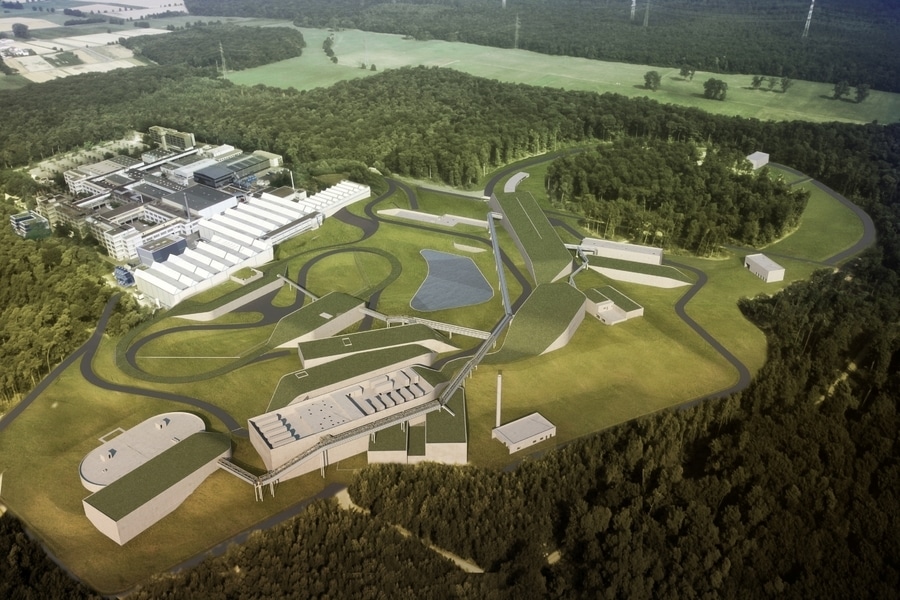
#Product Trends
In action for the universe in the laboratory: industrial shock absorbers from the Magnum family from ACE
Research in Darmstadt uses ACE industrial shock absorbers
The GSI Helmholtz Center for Heavy Ion Research in Darmstadt operates a large, globally unique accelerator facility for ions. Researchers from all over the world use the facility for experiments to gain new insights into the structure of matter and the development of the universe. In addition, they develop novel applications in medicine and technology. The new international accelerator center FAIR, one of the largest research projects in the world, is currently being built in Darmstadt. With FAIR, matter is to be generated and researched in the laboratory that otherwise only occurs in the universe.
The heart of the future accelerator center FAIR is the ring accelerator SIS100, which is equipped with superconducting magnets. This will have a circumference of 1.1 kilometers, while the existing GSI facility with the SIS18 heavy-ion synchrotron will serve as a pre-accelerator for the new accelerator complex. Industrial shock absorbers from ACE's Magnum family are used in one of the planned accelerator rings of the FAIR facility, the collector ring, which is to be used to store and cool the ions. They are used to secure the end position of drive units that are equipped with powerful linear motors. Industrial shock absorbers with the type designations MA3325EUM-14xxx with special stop sleeve and MA3325EUM-PP with PU head are mounted on the mechanical end stop of the moving linear unit. Their main task is to effectively absorb the inertia forces in the event of possible malfunctions in the linear motor drive unit, thereby protecting the construction. As a rule, the linear motor drive units ensure that the drive carriages are moved in two directions over a defined distance. This normally takes place without contact at the end of the respective section at the stops. For reasons of mechanical protection of the drives, the engineers in Darmstadt decided on the adjustable ACE industrial shock absorbers with thread size M33. These were designed in such a way that they can safely intercept the moving carriage if it should move outside the specified range due to a faulty control of the motor relay units.
Well prepared for the worst case scenario
With a stroke of 23.2 millimeters, the hydraulic machine elements from ACE, which can be precisely adjusted at the front and rear, are able to absorb 170 Newton meters of energy per cycle and can bring effective mass forces between 9 kilograms and 1,700 kilograms to a standstill safely, without rebound and without damage bring. If the components are only used in emergencies, because otherwise the deceleration is also taken over by the linear drive, additional energy overruns are permissible.
The Magnum family from ACE, which is considered the reference class for medium-sized industrial shock absorbers, is equipped with high-quality sealing technology that has been tried and tested in many thousands of applications. In addition, thanks to hardened guide bearings and integrated fixed stops, they have proven to be extremely robust and durable under many operating conditions in continuous operation. They are used in all areas of mechanical engineering. Typical fields of application are automation and handling, for example in machine tools and machining centers, as in the case described as a mechanical safety element integrated in linear slides or at the end of the path of swivel units to increase cycle times. Designers use the dampers, which are infinitely adjustable thanks to the easily accessible adjustment segments, also in the end positions to protect portals or in heavy industry to absorb masses on impact plates.
In Darmstadt, the technicians decided on the one hand to equip them with special stop sleeves and on the other hand for heads made of polyurethane. While the former strengthens the above-average massive construction of the ACE industrial shock absorbers as standard, a noise reduction of 3 to 7 dB is possible through the use of the special impact heads. With this selected combination, everything has been done in the FAIR system, purely in terms of shock absorbers, to ensure that there is peace and quiet even if the worst comes to the worst.
technique box
How industrial shock absorbers work
The hydraulic shock absorbers used in the present application were specially developed and manufactured by ACE for industrial purposes. These machine elements usually work with a pressure sleeve, with certain types, ACE shock absorber GmbH also uses a patented rolling membrane technology. The pressure sleeve of the adjustable and self-adjusting small and industrial shock absorbers works as follows: If a moving mass hits the damper, the piston sets the oil in the pressure sleeve in motion. The oil is pushed through the throttle bores, whereby the energy introduced is converted into heat. The number of effective throttle bores in front of the piston decreases, the speed is continuously reduced over the braking distance. The internal pressure remains almost constant and the force-displacement curve is therefore almost linear. For the longest service life of up to 25 million strokes, ACE has developed a hermetically sealed rolling membrane for special types of small shock absorbers. This ensures phase-clean separation of the damping fluid from the ambient air. This also enables direct installation in the pressure chamber, for example as end-position cushioning in pneumatic cylinders up to 7 bar. In addition, the rolling membrane favors the very low restoring forces of these maintenance-free, ready-to-install dampers. Perfectly graded hardness ranges and maximum energy absorption as well as the integrated fixed stop are further plus points. In addition, the use of a bolt protrusion enables impact angles of up to 25 degrees.
Magnum family: innovations for the highest damping performance
The larger industrial shock absorbers used in the presented application for the medium size of ACE with threads from M33 to M64 are representatives of the Magnum product family. This includes innovations such as diaphragm accumulators, a new type of sealing technology, pressure sleeves in the shape of a solid block and the availability of stainless steel versions with a stroke of up to 150 mm. In all designs and sizes, these machine elements not only increase the damping performance, but also significantly extend the service life of the machines and systems in which they are integrated. In addition, the effective mass range can be significantly expanded using these electroless hydraulic components, which gives users more leeway in terms of the damper size and the utilization of the overall performance of their design.
The range of solutions from ACE is also characterized by the fact that there is a wide range of suitable accessories for this and all other damper series. This eliminates the costly and time-consuming in-house production of assembly parts. Designers also benefit from specially developed dampers for applications with particularly high or low ambient temperatures. The stainless steel variants are also predestined for applications in medical and food technology with high hygienic requirements.
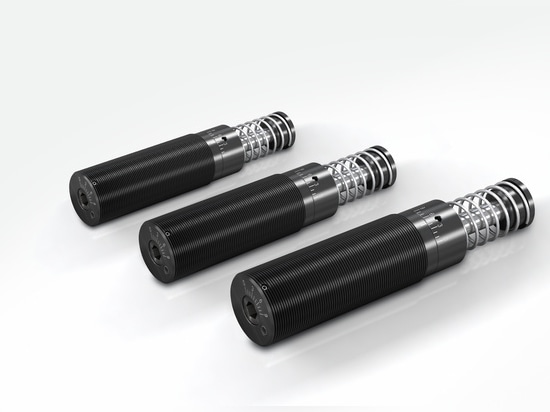