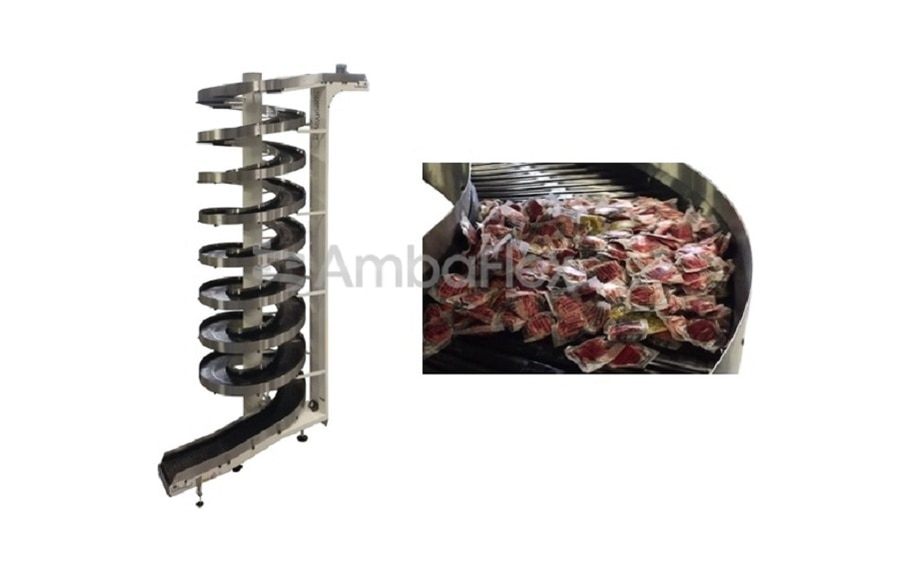
#Product Trends
Spiraling up bag’s in bulk
The 3 special bulk spiral conveyors have now been installed allowing the customer to increase their productivity over the coming decades.
A chemical company founded in Padova, Italy, in 1932 is active is the industrial production of insecticides, rodenticides and disinfectants for public health use. The company exports its range of products worldwide and is known as a quality company that fully accepts its environmental and social responsibilities.
However, their continued growth was limited by a specific aspect of the production lines. Their production efficiency was suffering because their down-stream packing equipment suffered from an inconsistent feeding flow and this made the equipment performance unstable. The problem was found to be caused by the so-called bucket elevators that, by nature, deliver an inconsistent flow. In order to meet their business objectives, the company needed to remove this bottle neck - but how?
There are no ready-made solutions that can handle an hourly throughput rate of 33,000 small lightweight bags measuring 60x60x10mm, and which only weigh 10grams, and also elevate them 5.5 meters. But when they told AmbaFlex about their issue, the sales engineering team came up with a very effective configuration based on a combination of the many available SpiralVeyor® options.
First of all, the 100% closed TPO style belt and small end roller diameters offer a unique platform with which to start the design. The AmbaFlex belt arrangement is such that the belt has no large slat-to-slat openings such as other systems have. This ensures that the small bags do not get stuck in between the belt elements.
Secondly, the highly polished, endless stainless steel plate guides on both sides of the belt offer almost no friction or jam points that could interrupt the seamless flow of the bags that are being handled in bulk. Furthermore, the specially designed connection profile even closes down the last gap between the guide and belt, thus ensuring zero downtime.
Finally, at the upper exit of the spiral conveyor, the extended transfer was specially configured. Traditional spiral conveyor belts make a 90 degree down belt turn, but this extension option offers a 180 degree turn of the belt allowing for a true waterfall transfer onto the connecting conveyor belt.
The 3 special bulk spiral conveyors have now been installed allowing the customer to increase their productivity over the coming decades.
One more proof of AmbaFlex’s leading position in Spiral Conveyor Solutions