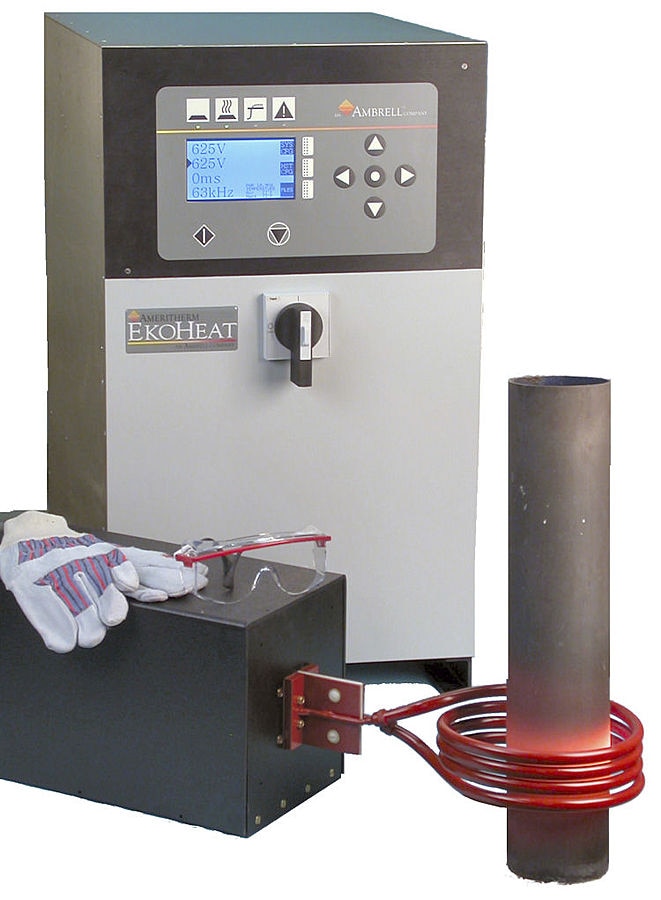
#Product Trends
Induction heating versus oven heating
*Superior Energy Efficiency: Induction provides rapid heating and can be turned on and off instantly. Energy is only used to heat the part that requires heating. Ovens often have lengthy ramp-up periods and are consequently left on perpetually, which results in excess energy costs.
*Precise Heating: With induction, you can heat up just the portion of the part that requires heating. With oven heating, the entire part may have to be heated, which can result in quality issues and scrap.
*Rapid Heating: Induction''s faster heating results in less scaling when heating steel, and ultimately better part quality. This is a significant consideration with die wear. Additionally, faster heating can garner higher production rates.
*Saved Floor Space: Ovens often require a significant footprint. Modern induction systems are small and take up less factory floor space. Induction workheads can be placed a distance from the power supply (up to 30m with an Ambrell EKOHEAT), making it easy to integrate into manufacturing processes.
*Greater Flexibility: Oven heating is typically a batch process, which can result in scrap. Induction is an in-line process and one part or many parts can be heated at a time in an energy efficient manner. Consequently, there is no need to inventory parts or, worse yet, scrap a lot of parts.
*Lower Maintenance Costs: Induction power supplies typically require less maintenance than ovens. With induction, coil repair or spare coils is the main consideration for maintenance, whereas ovens tend to be less reliable resulting in costly downtime and frequent oven relining.
For more information about induction, or to set up free parts testing with Ambrell''s Applications Lab, call +1 585-889-9000 or click here.