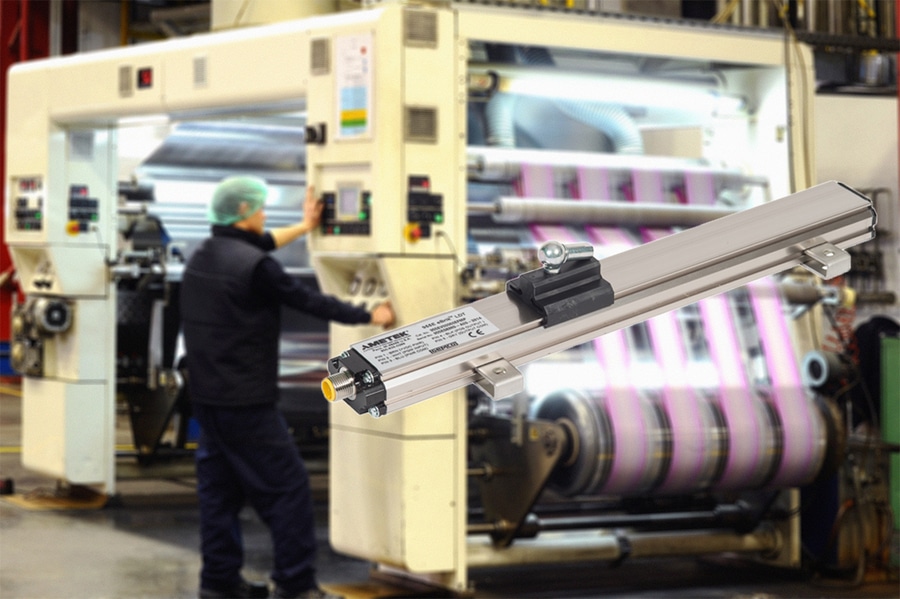
#Industry News
Magnetostrictive Control of Dancers on Rotation Press
Improved control of continuous web processing contributes directly to improved production speeds, reduced scrap and downtime.
Background
Improved control of continuous web processing contributes directly to improved production speeds, reduced scrap and downtime. Materials such as paper, nonwovens, textiles and plastics are commonly known for being parts of the web processing.
An important part of the controls in the continuous web process is the dancer controls of the roller controlling the tension of paper, textile or plastic, thereby ensuring an ongoing process without breaking or stretching the material in the rotation printing press.
Solution - How To Keep the Right Tension
Accurate output of a dancer control is essential for controlling the web.
A dancer is attached to a roller which is in constant contact with the material. The roller usually has a low tension cylinder or a pivot that allows the roller to move up and down typically +/ – 30 degrees to keep constant tension on the material without breaking it.
The right control of the dancers movement is crucial because faulty measurement can cause the paper or textile web to break. Monitoring the exact placement has traditionally been done by potentiometers, but the longer lasting solution is magnetic sensors, such as the Gemco Linear Displacement Transducers.
Potentiometers vs Linear Displacement Transducers on Dancers
Technologies Typically Used for Dancer Control:
1. Rotary or linear potentiometers have dominated the web tensioning industry for years, they feed the position data back to the control system. The disadvantage to this method is that linear potentiometers are unreliable and if held in one position for a long time the unit can “stick” on that position. The rotation press also inherently dither back and forth all day long in the same position and wear out that portion of the potentiometer.
2. Ultrasonic sensor have also been used for dancer control. However, this method has many disadvantages. For instance, humidity can affect the sensor performance, the unit is typically mounted under the roll looking up and over time lint can collect on the sensor causing incorrect readings.
3. Load cells can be used to detect the pressure applied to the dancer arm. This is costly and in some cases a strain gage output is not available.
4. Analog proximity switches are sometimes used but have a very small sensing distance of usually 10mm,(.39”) or less.
Advantages Achieved When Using LDT for Dancer Control:
The Gemco 955eBrik II™ Linear Displacement Transducer https://www.ametekfactoryautomation.com/products/linear-feedback/profile-style-linear-displacement-transducer/955-brik-series-linear-position-sensor is the ideal solution for dancer control of all types. The slide or floating magnet can be connected
to the dancer roll and a 0 -10 VDC or 4-20 mA output generated from the electromagnetic eBrik will accurately control the web process.
Advantages:
1. Non-contact providing long life cycle – Nothing to wear out.
2. Accurate to +/-0.03% of the stroke.
3. Repeatable to 0.001%.
4. Programmable stroke allows the customer to define the active stroke.
5. Rugged – Sealed to IP67.
6. Cost effective compared to other technologies.
7. Delivered in 1” increments up to 74” lengths for any application.
Benefits of Magnetostrictive Control
Non-contact magnetostrictive technology ensure accurate position sensors, longevity and reduced maintenance.
• Superior accuracy ensure production quality and fewer broken deadlines.
• Less down-time due to reparation of printing press.
• Minimizing the risk of technical breakdown compared to switch technology.
• Competitive for drop-in replacement of other Linear Displacement Transducer.
• Programmable zero & span.
All of the above secures a lower overall sensor cost requirement over the life of the
machine and fewer breakdowns of production, all leading to a safer budget.
Conclusion
The Gemco 955 eBrik II™ Linear Displacement Transducer (LDT) https://www.ametekfactoryautomation.com/products/linear-feedback/profile-style-linear-displacement-transducer/955-brik-series-linear-position-sensor is an ideal alternative to the traditional low-cost linear potentiometer. The small and constant adjustments in the web tensioning industry will in time cause wear in these potentiometers.
Magnetostrictive sensors offer non-contact position sensing and will therefore operate smoothly without experiencing wear and the following break-downs of production associated with contact type sensors.

