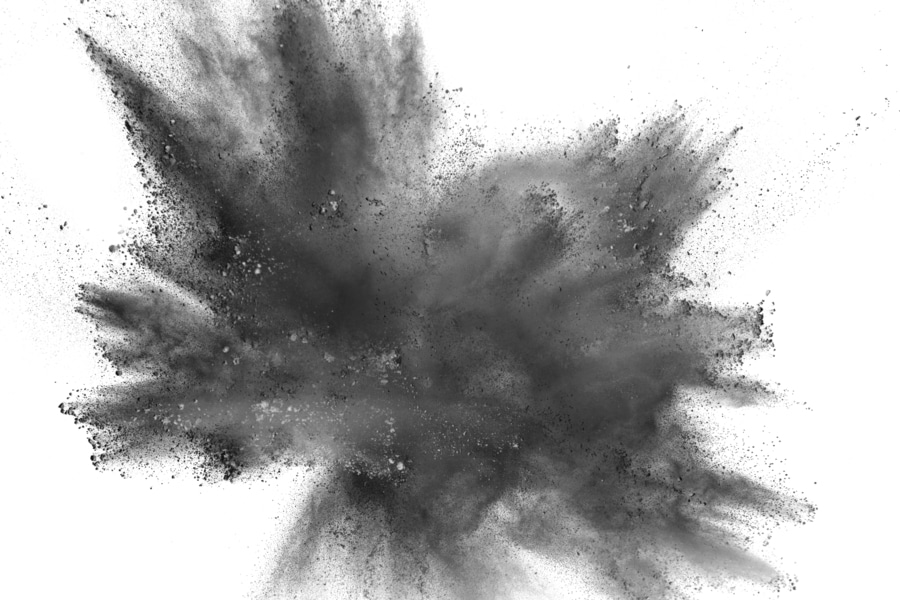
#Industry News
Blending bulk materials, maintaining particle structures and avoiding dust
Dust is produced wherever dusty goods are processed. Dust binding by wetting can take place gently and precisely in amixon® mixers.
Dust and its risks
Wherever powdery goods are processed, dusts occur. Their unpleasant property is that they can escape through the smallest of leaks. For example, from big bags, mixers, silos, pipelines or from filling plants. Dust can remain suspended in the air for a long time and settle everywhere. This happens preferentially on horizontal surfaces. In the event of a airblow, they swirl up again and float in the air. Some dusts are hygroscopic, absorbing moisture from the surrounding air and wetting all the surfaces on which they are deposited. This makes cleaning more difficult. Salt dusts, in particular, can be corrosive. Dusts can be combustible and even explosive. This is always the case if they are of organic origin; if they are very fine and dry. In the working environment, dusts are always a nuisance, they affect our well-being and irritate the respiratory tract. Escaping dusts are expensive, they represent material loss and imply disposal costs.
Powders that are end-used by consumers are usually conditioned, so that their dust content is negligible.
When particles are smaller than 0.1 µm, they are referred to as nanoparticles. Many materials exhibit completely new properties when they are nanodisperse. In medicine, powder metallurgy, electrical engineering and high-performance ceramics, nanodisperse structures pave the way for new materials and functions.
As the particle diameter decreases, the specific surface area increases logarithmically. The same applies to chemical reactivity. If particles are smaller than 0.1 µm, they are referred to as nanoparticles. Many materials exhibit completely new properties when they are nanodispersed. In medicine, powder metallurgy, electrical engineering and high-performance ceramics, nanodisperse structures pave the way for new materials and functions.
Binding dusts. Gently moisten bulk materials. Distribute extremely small liquid material quantities into large powder quantities
Dust binding by wetting can take place gently and accurately in amixon® mixers. Dust emissions can be avoided by agglomerating dust-fine particles together or by adhering them to larger particles. Even the smallest amounts of a suitable liquid can be helpful. The precondition, however, is that the liquid is distributed evenly over the entire surface of the bulk material.
Two-substance nozzles can atomise low-viscosity liquids micro-fine. At the same time, they create a fluidisation zone in the mix. This favours the mixing process.
KoneSlid® powder blender
Dust formation can be avoided within the bulk material by avoiding abrasion on the particles. This is where a conflict of objectives becomes apparent: on the one hand, the mixing process should achieve ideal homogeneity, but on the other hand, the particles should not break, crush or round during mixing. This problem can only be solved if an ideal mixing quality can be achieved with minimum energy consumption. This KoneSlid® mixer from amixon® realizes the gentlest way of powder mixing. It is preferably used:
• Where many spray-dried agglomerates are involved in the mixing process. These are, for example, milk powder derivatives for dietary nutrients such as baby food, cappuccino, .....
• medical active ingredients
• biological substrates
• enzymes
• cultures of bacteria
• instant beverages, iced tea, spices, tea, muesli, fat powder, lecithin powder, .....
KoneSlid® mixers achieve ideal mixing qualities in a very short mixing time. The discharge process is completed in just a few seconds.
Testing and process development
The mixing systems described above can be tested in the amixon GmbH technical center. Here, we gain interesting insights together with our customers. amixon® permanently keeps more than 30 test apparatuses available for you. In this way, we can make almost "the entire world of powder mixing" available to our customers at one location. A day in the amixon® technical center will be rewarding for a profitable investment decision. A powder mixer usually has a long service life. Often more than 20 years, sometimes even 40 years. Many times a day, important questions repeat themselves in the daily routine:
• Preservation of particle structures: How efficiently is mixing carried out?
• Flexibility: How much may filling levels vary?
• Efficiency: How well does self-cleaning and residual emptying work?
• Production reliability: Is it enough to take a look inside the mixer?
• Acceptance and ergonomics: How quickly can inspection openings be opened and closed?
• Are inspection doors permanently tight?
• Exclusion of contamination: How long does dry cleaning take?
• Control of microbiology: How long does wet cleaning and drying take?
• many more questions .....
We predict with high probability very good results and a high gain of knowledge.