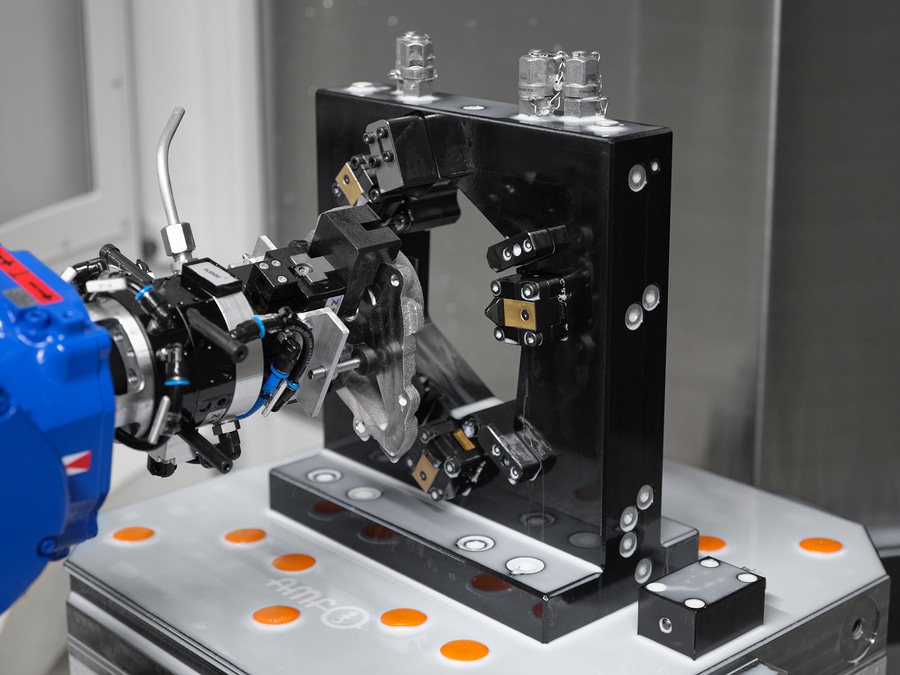
#Industry News
Application Scherzinger - Devices from AMF reduce costs and personnel deployment for the pump manufacturer
Clever hydraulic devices reduce costs and personnel deployment
The fact that super sports cars stick deep to the track is not due to dry sump lubrication at the least, which makes an oil sump obsolete. Scherzinger from the Black Forest manufactures the precision pumps for this purpose. The medium-sized company is delighted with such projects, which others are happy to turn down. This is because small series with such high demands on tolerance, process reliability and repeat accuracy are the paramount discipline of the Black Forest company. In order to achieve this reliably, Andreas Maier GmbH & Co. KG (AMF) has developed the right fixtures for this purpose. Now Italian and southern German super sports cars can go head-to-head in the Green Hell. And no matter who comes out on top in the end, Scherzinger and AMF are among the winners.
"This is exactly the kind of project we are passionate about," says Tobias King. "If we are involved at an early stage and can contribute our entire expertise in the development, design, construction and manufacture of high-performance pumps, then everyone is on top form," the project manager at Scherzinger Pumpen GmbH & Co. KG continues. When a premium car manufacturer from southern Germany knocked on our door about seven years ago, it was about a vane pump for dry sump lubrication for their super sports car. What started out as a manageable number of units in a manufacturing operation quickly grew into a series. And because the quality and stability of the precision pumps are impressive thanks to the high process reliability and repetition accuracy, this also arouses desires in Italy. But this marked the beginning of a new dimension, because it is not only Italian super sports cars that are currently in demand as never before.
The demand for super sports cars has been rising sharply for years
"Now this is all about quantities of several thousand per year, and that requires a completely different production concept," emphasises production planner Mario Maier from Scherzinger. Two cast aluminium housings and two covers are to be produced as fully automatically and unmanned as possible. The new 5-axis machining centre from Grob is therefore supplemented with new fixtures using automation from EGS "We have learnt a lot from the first fixtures, but now we needed a partner who understood us better and could respond to our needs," said Oliver Hindinger, who designs the work equipment at Scherzinger. This played into the hands of Willi Fast. The AMF application consultant for precisely such projects with key customers comes from a technical background and is happy to contribute his understanding and troubleshooting expertise. "I've been on the other side long enough and quickly recognise where the shoe pinches."
This results in four fixtures which, mounted on machine pallets, are inserted into the machine in just a few minutes and are positioned immediately thanks to zero-point clamping technology. The challenge here is fixing the blanks made of sand-cast aluminium. In a previous concept, two components were clamped and machined per fixture. However, this meant that more interfering contours restricted the machining process. "That's why we now only clamp one blank instead of two," explains Tobias King. "This has reduced complexity and significantly increased process reliability." Now the Grob 350, with its unique machine concept of the horizontal spindle position and swivelling table, can position the workpiece to the exact tolerance for each necessary machining operation after measuring the position.
Clever clamping solution considers all conditions
The blanks are clamped hydraulically with a maximum pressure of 190 bar. This is not entirely trivial with the larger pump housing. "To ensure that we can reach all positions during the machining processes, we have provided three tabs in the design that can be clamped and removed later," reports Oliver Hindinger. Once the EGS articulated arm robot has removed a part from one of the ten pallet drawers, it positions it precisely in the fixture. Then three vertical clamps with a 90° opening angle hold the housing in place with 7.8 kN, making it rock-solid and process-reliable. Additional mounting points are attached to the contact surfaces to prevent the workpiece from slipping. Holes and countersinks can now be drilled, sealing faces milled flat and the inside of the vane pump machined to size. The dimensional, positional and shape tolerances of 0.02 and 0.04 mm are very demanding. Once all the machining steps have been completed, a centring clamp built into the device fixes the pump housing in place. Now the toggle levers release the three clamping lugs so that the machine can remove them.
Although the production of the two covers is not quite as demanding, a few considerations are required to ensure that the blanks are securely clamped. Matching the horizontal spindle position of the Grob machine, the parts are inserted vertically into an arch-shaped fixture that completely encloses them on the narrow sides. Here the hydraulic vertical clamps also hold the parts firmly and securely in place after positioning. After machining, the parts are placed in further drawers of the pallet trolley before they are removed and deburred as well as finished.
Family run business with decades of tradition
In addition to the special challenges of vehicle technology and motorsport, Scherzinger pumps are also used in mechanical and plant construction as well as power plant technology. Founded in 1937, the company has divided its production into series and individual part to small series production with corresponding locations. The Black Forest-based company is also well known for its modular design, which enables it to quickly find suitable solutions for its customers.
At AMF, which is particularly valued worldwide for its zero-point clamping technology, such customised project tasks with tailor-made solutions are increasingly in demand. In doing so, the experienced experts are happy to bring all their expertise to bear in order to find the best solution for the customer's production, workpiece and productivity. When, as in this case, both are family run businesses with decades of tradition and have a common basis, it is a particularly good fit.
Direct communication between all parties at eye level with fast response times
Production has been running as desired since January 2024. The goal of fully automated, unmanned production has been achieved in record time. The result creates more capacity for other tasks thanks to the automation in combination with the fixtures. "We have managed to reduce personnel deployment by 25 percent compared to before," reports production planner Mario Maier enthusiastically. The fact that this project went into series production so quickly is thanks to everyone involved.
With satisfaction, Willi Fast from AMF summarises: "After initial discussions in March 2023, it was clear to me that there were many challenges to overcome in order to have all four fixtures ready for use by the planned start of production at the beginning of 2024. Our internal structure of design and project management proved to be a great advantage here, as it enables direct and transparent communication with the customer. We are particularly pleased that in Scherzinger we have a customer with whom the exchange of data and information is direct and swift. And this has been the case since our first joint project." Everyone at Scherzinger can only confirm this: "The fact that you can always reach a direct contact person and that AMF has always responded quickly is not something that can be taken for granted," says Oliver Hindinger. And Tobias King adds: "The collaboration was always on an equal footing. Unfortunately, we have experienced this differently."
Winners in particular beyond the track and on the road
In the meantime, demand for dry sump lubrication pumps from both the German and Italian super sports car manufacturers has increased significantly. Because the vehicles are not only approved for use on race tracks but also in normal road traffic, they are becoming increasingly popular with their customers, who can spend up to seven-figure sums. Scherzinger's forward-looking, automated production system can easily cope with increasing call-up figures. And in the end it doesn't matter whether Italy or Germany comes out on top at the Nürburgring, the high-performance pump of the dry sump lubrication system can cope with the extremely high demands of a 24-hour race with continuous speeds above 8000 rpm just as easily as the Sunday drive of the sports car enthusiast on the country road. That is why Scherzinger and AMF are definitely among the winners.
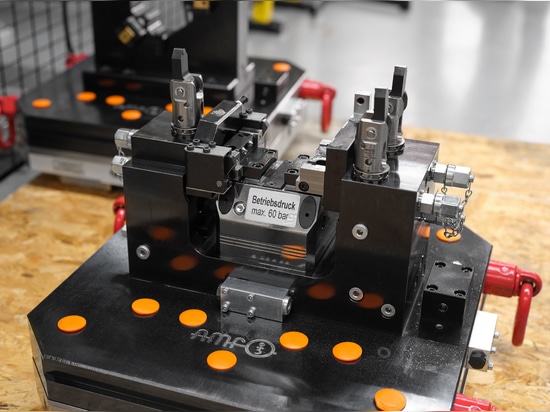
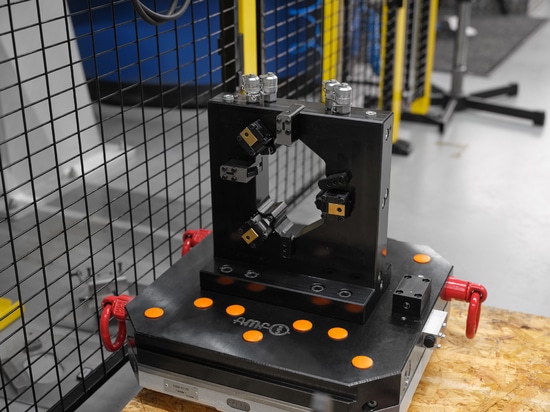
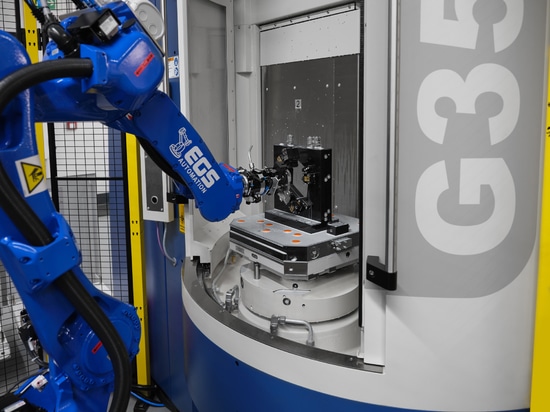
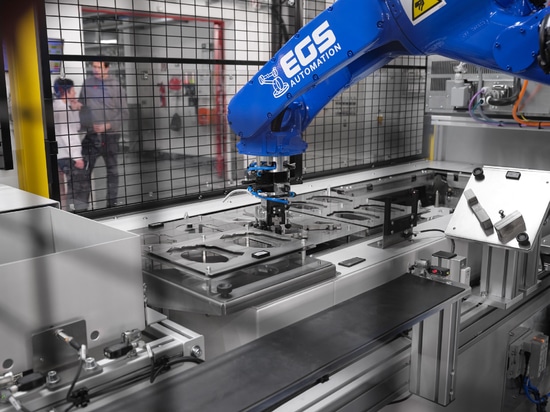
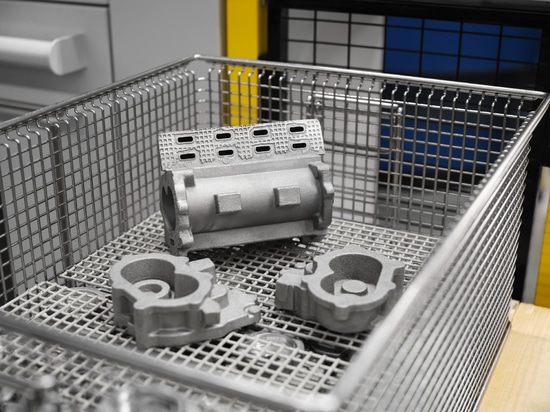
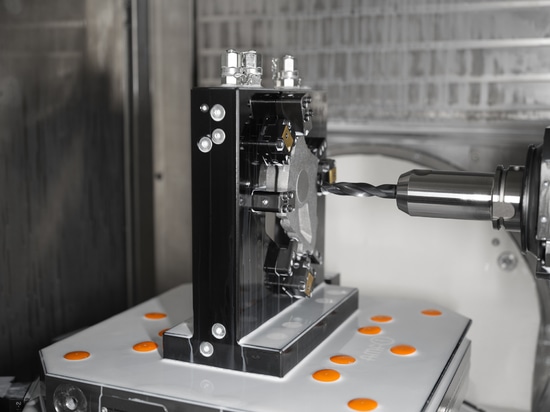