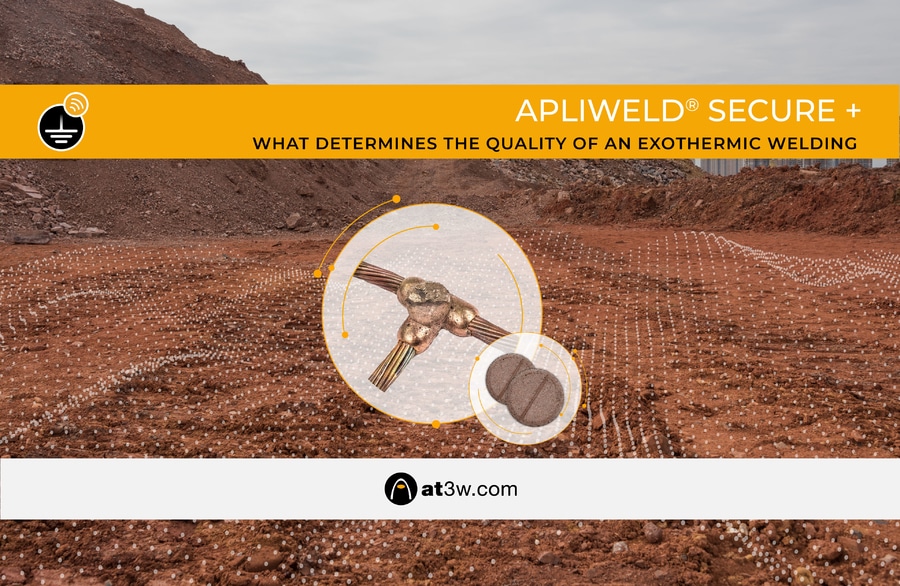
#Industry News
What determines the quality of an exothermic welding?
Exothermic welding, also known as aluminothermic welding, is the result of a process that achieves the molecular union of two or more metallic conductors through a chemical reaction.
If it is performed correctly, it results in a bond that is superior in conductivity and durability to any that is carried out mechanically. To obtain this, it is vital to follow certain criteria that determine the quality of the welding.
The fundamental element of any electrical installation is the earthing system. Its reliability and durability depend on its correct execution. An earthing system must be designed and executed properly to maintain its quality over time, which means that the connections have to be durable.
Copper aluminothermic welding is the most suitable method to achieve this, as the resulting joints have characteristics that are superior to any mechanical joint and wear-resistant. This type of welding, however, must meet certain quality criteria to ensure these conditions.
Verification and certification, two guarantees
In order to check whether the welding has been done correctly and that it meets the desired quality, a visual inspection should be carried out. At this point, it is important to check that the welding covers at least the previous surface of the conductors and that there are no other visible defects that could affect the quality, such as the presence of pores, slag or other impurities. The colour of the welding should be copper, variable in intensity, but with a metallic shine.
In this step, the degree of purity of the reagents is not so important if the end result is a connection that can withstand at least the same current as the conductors themselves and it has a similar mechanical resistance.
These two data can be proven by the certificate UL 467 “Grounding and bonding equipment”. To obtain this certification, it´s necessary to undertake an electrical and two mechanical tests of a series of weldings with different types of joints. The UL 467 certificate guarantees that the welding will fulfil the electrical and mechanical characteristics required for the installation.
Apliweld® Secure+: security and versatility
The exothermic welding system Apliweld® Secure+ from Aplicaciones Tecnológicas has a certificate UL 467, as well as other safety and versatility features.
Safety is achieved by the possibility of remote ignition, either by cable or by remote connection. During welding, copper melts at over 1100°C and it´s common to have sparks and spatter at very high temperatures. The wireless electronic ignition can reach up to 5 or 6 metres via Bluetooth connection and it ensures that the user can never be hurt by material spatter, sparks or any other element of the reaction. Remote ignition also eliminates the use of flammable material and provides a unique and safe procedure for this type of connection.
Versatility is provided by the tablet format of the Apliweld® Secure+, which can be used for traditional ignition or the electronic ignition mentioned earlier. The replacement of the usual eight references with just one and the compact format make it much more economical and easier to use and store.
If you would like to know more about the Apliweld® Secure+ exothermic welding system from Aplicaciones Tecnológicas, you can contact us via this link.
If you are interested in receiving free training on aluminothermic welding from our experts, you can also access our webinars section.