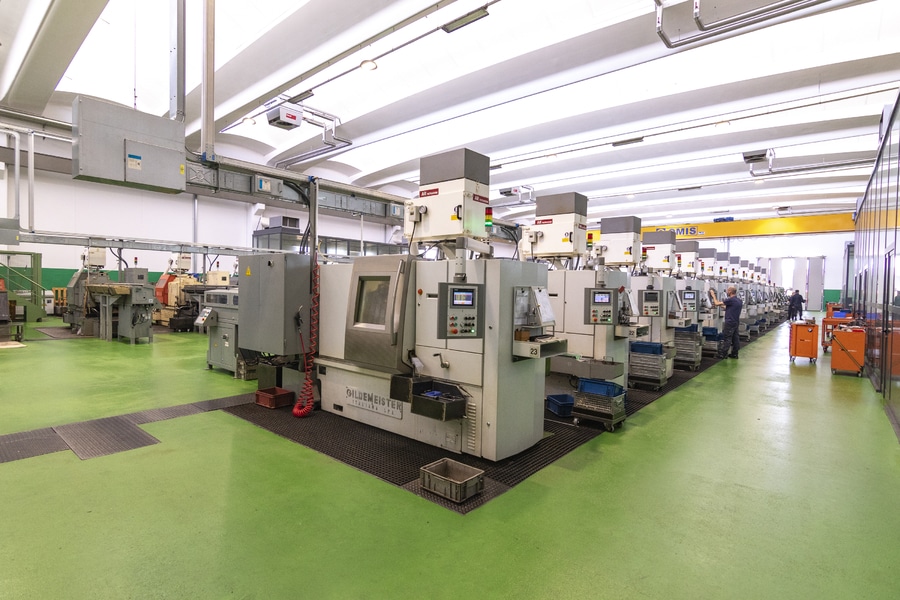
#Industry News
TURNER FOR PASSION ERBA SPA
CHANGE IS IN THE AIR
The story of Erba SpA is the
story of a man, Gianiosep
Erba, who at the age of 21
decides to start his own business,
together with his sister Carla, after
gaining a fair amount of experience
in other workshops. Already
at the age of 9, Gianiosep used
to attend this kind of places and
at 15 he worked on multi-spindle
machines
The way to the independent activity
begins with sacrifice and
without economic resources. And
yet, thanks to an unshakable will
and a never-ending commitment,
the company takes off.
"I used to work 7 days a week,
since early morning to late evening,
but not as an obligation.
It was really a great passion to
push me - the founder proudly
tells. Even my sister Carla, who
is now the company's counselor
and accountant, worked at the lathe.
We started producing small
metal parts for home furnishing
and household products. Then
we progressively expanded to the
gas and sanitary sectors, taps,
automotive, valves, until some
important orders also for the military
sector. Today the company
can count on 130 employees and
cutting-edge technology with 70
multi-spindle machines and 5
CNC spindles, as well as a certified
quality".They also had to go through hard
times. The crisis in 2008 hit the
company harshly. But instead of
surrendering or firing personnel,
the owner started up again with
renewed enthusiasm in the search
for new customers and in the
production of new samples, which
led in a few years to a further increase
in turnover and to an expansion
of the production site. In
the last times, when the younger
generation - the sons Simone,
Stefano and Mauro Erba, Marco
and Daniel Zonca - joined the
company, the activity took a leap
forward, acquiring important customers
also abroad.
The participation in trade fairs
gave the company a push overseas.
"After attending some exhibitions
in Europe and in Italy, in
2012 I left for Sao Paulo, Brasil,
without the machines and without
knowledge in the language of the
place - the owner remembers.
Yet, I brought home an important
order. Despite not having a dedicated
sales network, but relying
only on 'word of mouth', we have
acquired over the years customers
in Germany, France, South
America, Taiwan, who appreciate
not only our production of small
parts but also the one of bar loaders
and multi-spindle machines".
Our experience in customer
service
Erba Spa, active since 1972, deals
with the production of fittings
machined from bars,
mainly intended for the sanitary,
oil-hydraulic, diggers, gas valves,
automotive, bearings and medical
sectors. With two offices, in
Palazzago and Barzana (BG), the
company serves both the domestic
and the international markets,
supplying its products on
European and overseas countries,
like China, the United States, India
and Brazil.
The company is equipped with
multi-spindle lathes both with
cams and CNC, and with numerical
controlled single-spindle lathes
for the production of precision
mechanical small parts, made
with ferrous and non-ferrous materials.
Researched among the
most technological models on the
market, the machines installed in
the two production sites are able
to produce pieces according to
specific customer requirements,
guaranteeing compliance also
with very narrow geometric tolerances.
The company is also able to provide
heat treatments on parts, such
as normalization, annealing, tempering
and decontamination, as
well as carrying out galvanic protective
treatments (nickel plating,
chrome plating, electrolytic galvanizing
and zinc-nickel) and surface
treatments (polishing, brushing,
dressing, tumbling, sandblasting
and Scotch Grip application) to
improve their characteristics and
provide a finished product ready
for use. Thanks to an external
supplier, it is also possible to carry
out bending operations of the pieces
after the turning process.
The finished product is delivered
according to customer needs,
in metal or plastic containers, in
cardboard boxes, or in special blisters,
marked with personalized
identification labels.
Assistance and maintenance
Erba Spa carries out the assistance
and revision of its production
plants. All the machines in the two
locations are overhauled by the
internal maintenance department,
formed by qualified personnel in
the management of the mechanical,
electrical and software-related
parts and PLCs. In collaboration
with the company LOAD, today Erba sells machines
completely overhauled and customized
according to customer
needs, with CE certification.
Quality controls
The Bergamo-based company
has adopted quality controls in
all production processes: processing,
equipment and selection of
finished products, through state-
of-the-art instruments and a
department dedicated to 100%
objectified control of production.
The machines are equipped with
cameras for dimensional verification
of the pieces and identification
of eventual chip residues.
Both on the raw material and on
the parts subject to external treatments,
strict controls are carried
out during the receipt of the
goods, according to the requirements
provided by the customer,
verifying the quality certificate on
each individual lot treated by the
supplier. Suppliers are approved
and subjected to periodic audits
according to the ISO 9001 and
IATF 16949 certification schemes.
Respect for the environment
In both locations, there are stateof-
the-art IFP ultrasonic washing
machines which use a completely
vacuum washing cycle in all
phases: thanks to the ultrasounds,
this type of washing guarantees
the complete elimination of all
oily residues from the components
just made. Deep cleaning but also
attention to the environment: in
fact, washing machines ensure
no pollution both inside the working
area and outside. Thanks to
a special solvent based on modified
alcohol, Erba guarantees the
cleanliness of the parts from microparticles
of oil and impurities,
overcoming even the strict controls
in the medical sector.
The machines are also equipped
with the oil mist cleaners created
by ARFILTRAZIONI, AIR CLEANER
- MIST COLLECTOR, used
for the vacuuming and - through
Hepa filters - the filtering of the
oil mist spread in the production
area: this guarantees the absence
of oily particles in the air which
are recondensed to be reintroduced
directly into the machine,
thus guaranteeing a healthy working
environment, in compliance
with the regulations in force.
Why we chose AR FILTRAZIONI
"We had major problems to overcome with the existing centrifugal plants made in England - explains Stefano
Erba - and the mist and fumes in the workshop were still heavy; this caused us problems with the sanitary controls.
Furthermore, we needed a rapid and infrequent maintenance, as well as the recovering the condensed oil.
To solve our problem, become more complex after the use of whole oil on all lathes and high pressure pumps during
a 24-hour activity, we tested two different Italian brands for a few months. That period of time was enough to decide,
in 2013, to equip all our machines with AR FILTRAZIONI systems and nowadays we can definitely state that our
choice was decisive for the solution of all our problems, with the following advantages: a clean environment, fast,
annual and low-cost maintenance, zero additional working hours thanks to the presence of a filter clogging detector
on each machine; moreover, a relevant recycling of condensed oil, which can be re-introduced into the machine, a
fundamental aspect from an ecological point of view and for economic savings. Our opinion on the plant is summed
up in one word: it is simply perfect!"
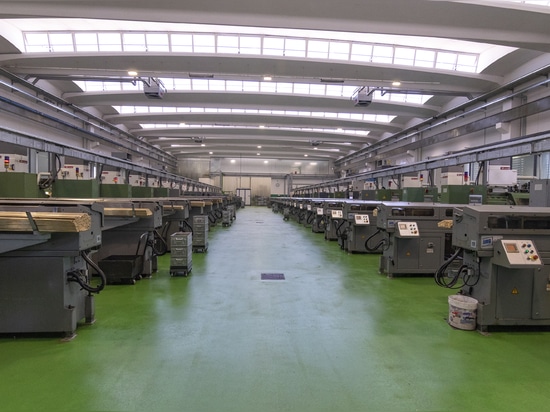