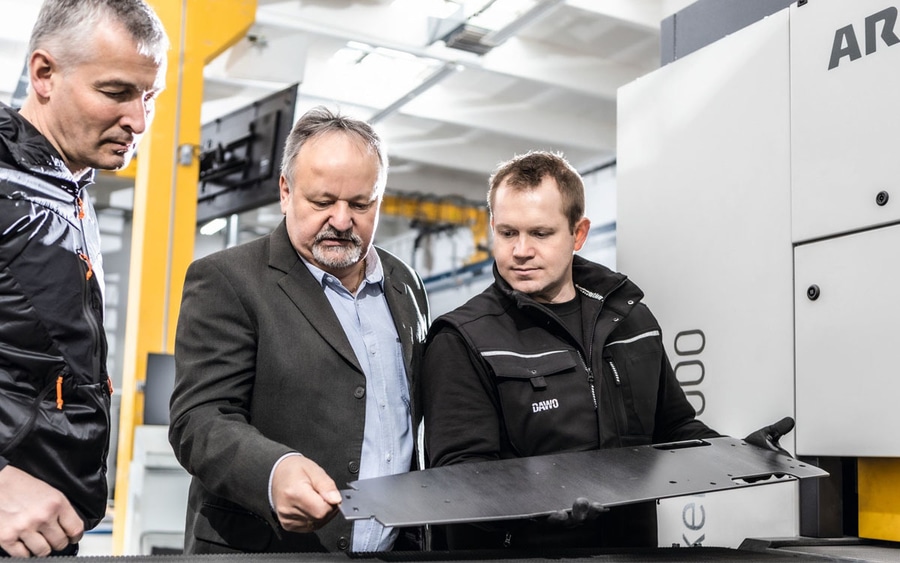
#Industry News
Deburring and edge rounding at the highest level:
DAWO relies on the EdgeBreaker® 3000
The DAWO GmbH from Austria has created a success story with the EdgeBreaker® 3000 when it comes to deburring and edge rounding. Thanks to the EdgeBreaker® 3000 deburring machine, even the most demanding deburring and edge rounding tasks can now be effortlessly and professionally carried out.
Supply more parts in better quality
With quality awareness, reliability and many years of experience, contract manufacturer DAWO GmbH in Mattighofen (Austria) has built up a loyal customer base in many industries: Mechanical engineering is the largest customer group, but aerospace is also included, as are the rail industry and commercial vehicle construction. "We can produce the required parts quickly and efficiently. And then there is our powder coating, which not everyone else has," says founder Wolfgang Dattendorfer, explaining why the company has grown so quickly. The 20 employees have access to modern machinery for laser cutting, bending, punching and drilling. DAWO also offers all welding processes (TIG, MIG, MAG, CMT) or stud setting. DAWO can even deliver individual parts and small series made of sheet metal within 24 hours if necessary.
"The fiber laser produces even sharper edges than the CO2 lasers. The ARKU machine is perfect for this."
- Wolfgang Dattendorfer, Founder and Managing Director of DAWO GmbH
Powder coating requires perfectly rounded edges
Thanks to its sister company DAWO Pulverbeschichtung GmbH, the contract manufacturer is also aware of what is required for a durable coating: perfectly deburred and rounded edges. Even with modern machines, these cannot be taken for granted. When the contract manufacturer purchased a fiber laser in addition to its CO2 laser cutting machine, the experts immediately noticed the sharp cutting edges of the new system. The idea of having their own deburring machine, which had been on the minds of the experts at DAWO for some time, became a definite project.
Powerhouse among the deburring machines
Dattendorfer then had the opportunity to inspect an EdgeBreaker® 3000 together with ARKU sales representative Thomas Weinfurtner at an ARKU user's premises. "In the end, we opted for the 3000 because of the double-sided processing. The machine offers what we want: a fast process and high throughput," says the DAWO Managing Director. This applies both to stainless steel parts, which make up the majority, and to aluminum parts. Dattendorfer continues: "We can offer clean parts quickly, even in combination with powder coating. This is very well received by customers."
The EdgeBreaker® also alleviates the shortage of skilled workers at DAWO. "We don't have enough people we need anyway. And I don't expect that to change much in the coming years," explains the DAWO founder, and says: "We are keeping our staff levels as high as possible and investing in automation." This enables DAWO to work efficiently and reliably and process larger volumes. Longer unmanned shifts are also possible.