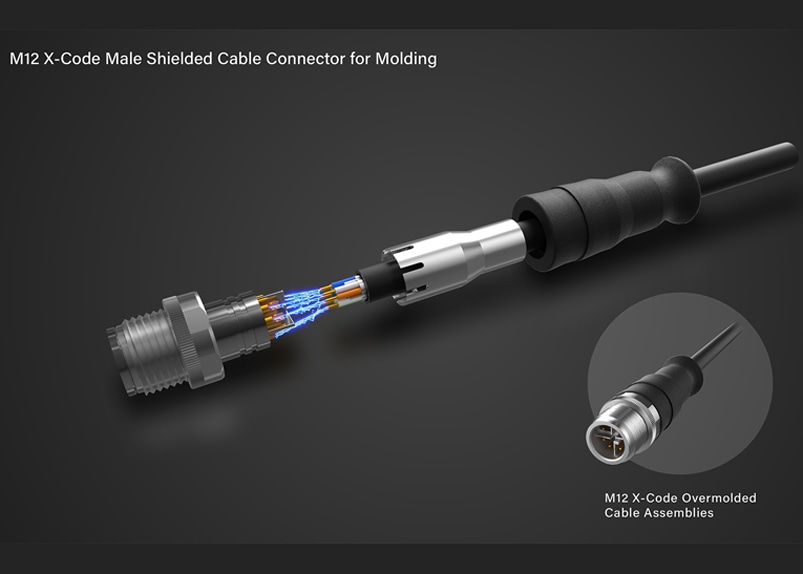
#Industry News
What is the M12 Connector? What Sets It Apart?
What Is the M12 Connector?
What Is the M12 Connector?
An M12 connector with a cable attached to it, demonstrating the connection between the two components.M12 connectors are robust, circular connectors featuring a 12-millimeter (mm) threaded locking mechanism. They are typically found at the end of PUR or PVC jacketed cables. The "M" refers to the standardized metric thread size of the connector. The number "12" indicates the specific diameter of the threads in millimeters (mm). The International Electrotechnical Commission's IEC 61076-2-101 defines the standard for the exact geometry and conductor configuration of M12 connectors. Besides, due to their compact size, high versatility, and resistance to environmental factors (such as vibration, dust, and moisture), these connectors are designed for a wide range of industrial applications and ensure safe operation. They also provide easy installation and built-in shielding against disruptive EMI/RFI signals, ideal for the current industrial setting. Common use cases include factory automation, industrial internet of things (IIoT) system, sensor connections, and Ethernet networks.
M12 Connector Codes and Pin Layouts
M12 connectors offer a versatile solution for industrial applications, but their true power lies in their ability to handle a wide range of signals and power. Different codes determine the pin layout and signal type (what function each pin serves) of the M12 connection, as well as the number of pins. The pin count options for M12 connectors include 2, 3, 4, 5, 6, 8, 12 and 17 pins variations. It's important to specify the right M12 coding to ensure proper functionality and avoid connection errors.
Coding for Data Applications
Coding for Data Applications
A-Coding Pin Assignment-A-code is the most versatile of the M12 connector codes. 2 to 17 pin counts allow it to handle various applications. You'll find A-coded connectors in sensors, actuators, DC power supplies, and Ethernet networks (up to 1 Gbit).
B-Coding Pin Assignment is primarily designed for fieldbus systems, such as Profibus, which link sensors, actuators, and controllers within a distributed automation network. Typically featuring 5 pins, B-coded connectors have a standardized pin layout for power and fieldbus data transmission.
C-coding (also referred to as Micro-AC) features a dual keyway design and caters to AC power applications. These connectors are optimized for powering smaller automation components, like compact motors and drives.
D-coding is specifically tailored for industrial Ethernet applications requiring data transmission up to 100 Mbit/s. These connectors usually have a 4-pin arrangement, accommodating two twisted pairs for data communication. Instead of power delivery, D-coded connectors focus on reliable signal transmission.
X-Coding X-codeX-coding is engineered for high-speed industrial Ethernet, supporting data rates up to a blazing 10 Gbit/s. To handle this increased bandwidth, X-coded connectors feature an 8-pin configuration. They are ideal for demanding applications that require fast and reliable data transfer, like real-time video monitoring systems or high-precision machine control.
Coding for Power Applications
Within the M12 connector family, several specialized codes cater to the unique demands of power distribution within industrial settings.
L-coding, S-coding, and T-coding are optimized for AC and DC power transmission. These codes feature pin configurations designed to handle higher voltages and currents, ensuring safe and reliable power delivery to motors, drives, industrial lighting, and other power-hungry equipment.
Coding for Power Applications
L-code S-code T-code
What Is the Difference Between M12 and M8 Connectors?
M12 and M8 connectors become popular choices with the rise of industrial automated systems. They are commonly used to link inductive sensors, actuators, and switches, due to compact size and transmission ability. The main difference between the two is their shell diameter and the number of pins.
Though M8 is smaller and cheaper, it has limitations in terms of power loads and pin options. This is where the advanced version of this connector, M12, comes in handy. M12 not only has a larger diameter that translates to a higher power capacity, but also a superior water resistance. Thus, it can function properly even when submerged, making it a valuable asset for applications in measurement, food and beverage, robotics, and other industrial use that involves moisture.
Ultimately, the choice between M8 and M12 connectors boils down to your specific requirements. Here’s a brief comparison of the two:
M8 Connector M12 Connector
Shell Diameter 8 mm 12 mm
Connection Density 4-8 pins Up to 17 pins
Key Advantages Compact size, lower cost Higher power capacity, more connections, robust design
Considerations Limited power and data, fewer pins Larger size, potentially higher cost
Coding Systems A-coded, D-coded (limited options) A-coded, D-coded, X-coded (wider range)
Other Shell Sizes in the M Series Connectors
M5
Miniature design: With a 5mm shell diameter, M5 connectors are ideal for space-constrained applications where size is a premium.
Low-power and limited signals: They are well-suited for carrying low currents (up to 2A) and a few signal lines, making them perfect for sensors, data acquisition, and control systems.
M23
Large and powerful: Boasting a 23mm shell diameter, M23 connectors are the biggest and most powerful in the M series.
High-power applications: They are designed for demanding tasks requiring significant 、ant currents (up to 63A) and multiple signal lines, making them perfect for heavy machinery, high-power motors, and industrial automation systems.
The Advantages of Using M12 Connectors
M12 connectors have revolutionized industrial automation by offering a robust and versatile solution compared to traditional wiring methods. With various pin configurations and coding options, M12 connectors can cater to a wide range of signal and power transmission requirements. Their unique design translates into a multitude of benefits, driving their widespread adoption. Further benefits include:
waterproof-connector-sealing-techUnmatched Ruggedness for Harsh Industrial Environments
M12 connectors outperform the common RJ45 in harsh environments. Their IP67-69 components withstand dust, moisture, vibrations, and extreme temperatures.
Constructed from robust materials like gold plating and beryllium copper contacts, these connectors can also withstand hundreds of mating cycles without compromising performance, reducing downtime.
Superior EMI/RFI Shielding to Prevent Signal Disruptions
Electromagnetic Interference (EMI) and Radio Frequency Interference (RFI) are external signals that derive from electronic devices, and without proper EMI/RFI shielding, these signals will disrupt the transmission of connectors or other sensitive areas, leading to inaccurate data collection and hindered process control.
The EMI/RFI shielding of M12 connectors are created with materials that reduce unwanted electromagnetic signals, such as silver, silver aluminum, silver nickel and other alloys, which act as fillers beneath a base material (usually silicone) in the gaskets. In turn, this metal shielding acts as a physical barrier for M12 connections, which can reflect or absorb disruptive signals, ensuring the integrity of data and power transmission.
Effortless Installation
Most M12 connectors feature a push-pull mechanism, allowing it to be inserted and removed easily without tools, as all you have to do is apply or release pressure in a specific direction. It is compact and enables fast operation, reducing installation time up to 80%, as well as labor costs in the process.
Another popular variation is M12 connectors with threaded coupling mechanisms. They can be screwed in by hand quickly and easily, while the threaded design offers excellent stability, making it highly reliable in applications where frequent vibrations are involved.
Optimal Size and Capabilities for Industry 4.0 Applications
With the rise of Industrial Internet of Things (IIoT) and Industry 4.0, the role of M12 connectors has become more critical. Their compact 12mm diameter is one of the main reasons for this wide application, along with their superior performance, durability, and lower maintenance costs. M12 connectors also have higher versatility, allowing them to seamlessly integrate with various industrial devices and systems, ultimately creating an interconnected industrial Ethernet environment.
The application of M12 within industrial automation is sophisticated, from data transfer between devices and programmable logic controllers (PLCs), to connecting sensors and network components. And as technology continues to evolve, M12 connector innovation keeps pace. They cater to diverse industries like robotics, cellular communications, and alternative energy, allowing M12 to be the leading solution for a future-proofed industrial landscape.
RJ45 V.S. M12 Connector for Ethernet Connections
Though both RJ45 and M12 connectors are common for industrial ethernet, RJ45 connectors are usually more compatible with Cat5 standards, which is often used in older systems; while the M12 connector has a sleeker and sturdier design, which makes it a better choice for limited spaces and harsh environments. We’ll delve deeper into their differences below:
The RJ45 connector is actually an earlier model, easily recognizable for its rectangular housing and eight pins. It has been widely established as an Ethernet connection solution and is available for both Cat5 and Cat6 (IEC 11801:2002) standards.
In 2002, the Profibus User Organization (PNO) has specified a new RJ45 connector that features a push-pull mechanism, along with a IP67 rated a plastic or metal housing, which has then been approved by the Automation Initiative of Domestic Automobile Manufacturers, Germany for use in PROFINET systems.
M12 connectors, being considerably newer in the industry, boasts a D-coding that has already been issued an Industrial Ethernet standard according to IEC 61067-2-101 Amendment 1, and has an IP167 rating that is advantageous in industrial environments. Its application is also supported by PNO, while being included within the PROFINET specification with the RJ45 push-pull connector.
The M12 connector also has a more compact design, while providing stable connection even when subjected to physical stress (including shock and vibration), making it ideal for the miniaturization of devices.
However, some M12 connector types are only partially compatible with the Cat5 (IEC 11801:2002) Ethernet transmission standard, which may cause electrical imbalance and hindered transmission, so it is important to select M12 connectors that can prevent these issues.
M12 Connectors IP Rating
Within the two-digit IP rating, the first digit indicates the level of protection against solid objects like dirt or dust, whereas the second digit represents the level of protection against liquids (including dripping water, sprays, splashes, summersion etc.)
M12 connectors commonly hold IP67, IP68, and IP69K certifications, demonstrating their suitability for demanding applications:
IP67: This rating signifies that the connector is completely dust-tight, having complete protection against contact up to 8 hours, and can withstand powerful water jets from any direction, as well as temporary immersion up to 1 meter for 30 minutes. This type of M12 connector is a popular choice for applications involving frequent exposure to dust, washdowns, splashes, or temporary underwater use.
IP68: This indicates that the connector has the same resistance against solids and water jets as the IP67 rating, while also being able to withstand prolonged immersion in water up to 1.5 meters for 30 minutes, making it ideal for environments prone to occasional flooding.
IP69K: Not only are IP69-K rated M12 connectors dust-tight, they can also endure high-pressure, high-temperature water jets commonly used in industrial cleaning processes. This makes them perfect for applications in the food and beverage industry, chemical plants, or anywhere requires frequent rigorous cleaning.
How to Select the Right M12 Connector?
Choosing the right M12 connector for your application requires careful consideration beyond simply following equipment recommendations. While manufacturer data sheets provide a starting point, with details such as product material, cable assembly method, etc, it's crucial to select a high quality connector with power and temperature ratings that exceed your equipment's absolute maximum requirements to ensure safe operation.
Material
As we’ve mentioned earlier, materials with signal attenuating properties are crucial for the M12 connector’s EMI/RFI shielding, so be sure that silver or silver alloys are incorporated for proper protection against disruptive electromagnetic signals. The material of your M12 connector shell also plays a critical role in its durability and performance. Common materials for the shell include plated brass, stainless steel, and various other alloys.
Nickel-plated brass is the most popular choice for M12 shells as brass offers good conductivity, while the nickel plating provides durability and excellent resistance to corrosion, while being affordable. Stainless steel on the other hand, offers superior strength, corrosion resistance, and washability for environments with extreme temperatures, high pressure, or aggressive chemicals. Some M12 are made with different alloy variations to achieve specific properties such as enhanced strength, improved corrosion resistance, or better machinability, you may consult your manufacturer for detailed information on the alloy.
For the contact pins, copper is used to provide excellent conductivity. There are also some M12 connectors that include a lightweight, high-performance thermoplastic casing to provide better insulation and limit the connector’s exposure to harsh elements
Cable Assembly Method
M12 connectors usually offer options for overmolding and on-site assembly.
Overmolding: This ready-to-use version is assembled by creating a sealed layer around the cable and connector junction, which can provide enhanced protection and durability against dust, moisture, vibration, and extreme temperatures. You can even incorporate logos or custom markings into the overmold for branding purposes.
On-site Assembly: This type of M12 connector can be quickly soldered or crimped together on-site with simple tools, saving manufacture time. Its design also allows greater flexibility over cable length and other features, which makes it ideal for prototyping needs or other applications where frequent re-assembly is necessary.
Power and Temperature Ratings
Identify the absolute maximum power your device consumes and its operating temperature range before choosing a M12 connector, as this will impact the overall performance capabilities. Once you have determined these factors, opt for a connector with higher ratings to provide a safety margin. This buffer ensures reliable operation even under unexpected fluctuations or peak conditions.
Environmental Considerations
We previously discussed IP ratings, which indicate the level of protection against dust and liquids. Consider this when choosing an M12 connector with an IP rating suitable for the anticipated level of contact and water exposure in your application.
Moreover, if your equipment may be subjected to shock or high vibrations, be sure to select a connector known for its resistance to physical impact.
For harsh environments with chemicals or corrosive elements, it is also advisable to ensure the connector housing material offers superior corrosion resistance, to prevent risk of damage and electrical hazards.