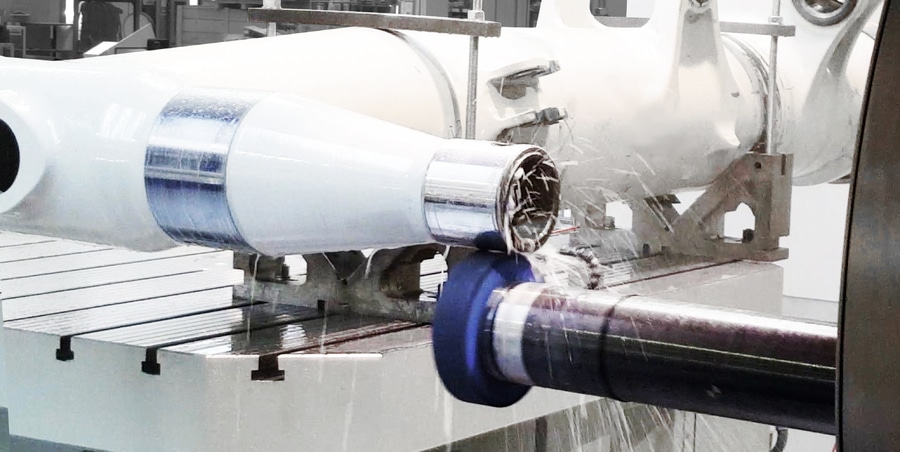
#Industry News
AEROSPACE REPORT
Precision flies
The aeronautical and aerospace sector has
in AZ SpA a technological partner able to
propose numerous specific grinding
solutions with high innovative content. In the
range of grinders designed by AZ, the new
LBC777 line for the orbital machining
of landing gear is a recent and very
successful example.
The aerospace sector is in continuous
technological evolution and seems not to
know crisis. Direct, indirect EOM and
certified aerospace subcontractors always
research and develop innovations for all
components and processing processes
used, for example, new "hyper-special"
materials such as inconel, high-alloy steels,
super alloys with base of cobalt and nickel,
titanium etc. Aerospace also means working
on very expensive single pieces and
following strict production procedures with
special work cycles that guarantee their
traceability and above all "zero defect" on
the final pieces. For machine tool suppliers,
and in particular for finishing machines
such as grinding machines, no mistakes
are allowed.
In this context, among the manufacturers
of cylindrical grinding machines accredited
for aerospace, the Italian AZ SpA of Thiene
(VI) has been able to gain a worldwide
leadership success thanks to the high quality
and performance levels of its products. This
is the result of high professionalism and
engineering creativity able to grasp and
often anticipate market demands. AZ has an
impressive range of grinding solutions
designed specifically for the aerospace
industry called "AZ Aerospace" for the
manufacture and maintenance of
components of aircraft engines and
landing gear.
AZ grinding machines are all
customisable, energy efficient, safe, reliable
and comply with Industry 4.0 requirements.
The numerous lines available are developed
with the range AKP for landing gear
grinding machines with gap bed, GSB for
internal landing gear grinding machines, RU
and RUG for universal grinding machines for
external and internal diameters and LBC for
landing gear orbital grinding machines for
external and internal diameters.
In particular, the new LBC777 represents a
recent example of a solution for
asymmetrical heavy parts with rotating
table. One of these grinding centres is
successfully used for all Boeing series with
others for alternative brands of landing
gear. A new self-balancing orbital grinding
system and rotary table facilitates the
grinding of the heavy-duty landing gears
without displacement of the workpiece. In
fact, the rotary table allows the grinding of
external and internal diameters in a single
piece grip and is moved by the overlapped
and crossed arrangement of the main
machining axes, Z and X, which allows ample
operating capacity with reduced dimensions
on the ground. The machine axes slide on
high precision recirculating linear guides.
The machine base has been designed with
FEM analysis and is made with a special
“Composital” technology structure that
reduces the elasticity coefficient,
guaranteeing an exceptional absorption of
vibrations, great machine rigidity, stiffness
and high dynamic performance.
The LBC777 wheelhead is configured with
two spindles for internal grinding and one
spindle for external grinding. The
wheelhead, mounted on a rigid structure, is
equipped with an AZ system for
self-balancing and runs vertically in the
Y-axis, on sliding guides with anti-friction
material "Turcite" equipped with
automatic lubrication.
The grinding machine is characterised by
the particular processing cycle that takes
place through the orbital grinding of the
workpiece surface. On the stationary piece
and positioned by the rotating table, the
grinding wheel used follows the geometric
trajectory of the piece along its generating
line both for grinding external and internal
diameters. With this axis scheme, the
machine allows an internal grinding capacity
from 70 up to 900 mm, an external grinding
capacity from 10 up to 450 mm and a
tangential grinding capacity of 2,000 x 850
x 1,500 mm.
Silicon carbide, corundum, CBN and
diamond grinding wheels allow grinding all
aerospace materials, metals and their alloys
including chromium and, in particular, those
subjected to the most innovative systems for
thermal spray techniques, such us H.V.O.F.
(High Velocity Oxygen Fuel). The grinding
process has some functions to give to the
operator few automatic and safe working
cycle: electronically variable spindle speed,
GAP control, dressing control, CRASH
control and control of orbital diameters
from CNC. This offers the machine the
possibility to reach unbelievable
performance on accuracy. In addition,
Wikicam is a monitoring system that allows
to control remotely some parameters of the
CNC machine. There is also a built-in live
video streaming solution to monitor what
the machine is doing in real-time. The
connection to the builder's headquarters is
made by a high-strength secure encryption
algorithm, using a VPN.
The grinding machines produced by AZ
use the most advanced mechatronic
solutions. Measurement systems, motors,
drives, as well as machine mechanisms and
applied CNCs, are selected among the best
brands in the world. With over 40 years of
experience in the sector and more than
3,000 grinding machines delivered and
operational in more than 80 countries
worldwide, AZ has always distinguished
itself in tackling and solving technical issues,
even with complex shape, proposing
customised solutions to individual customer
needs. The design creativity of AZ allows the
creation of product lines, like the new
LBC777, to be among the most
sophisticated on the market today.