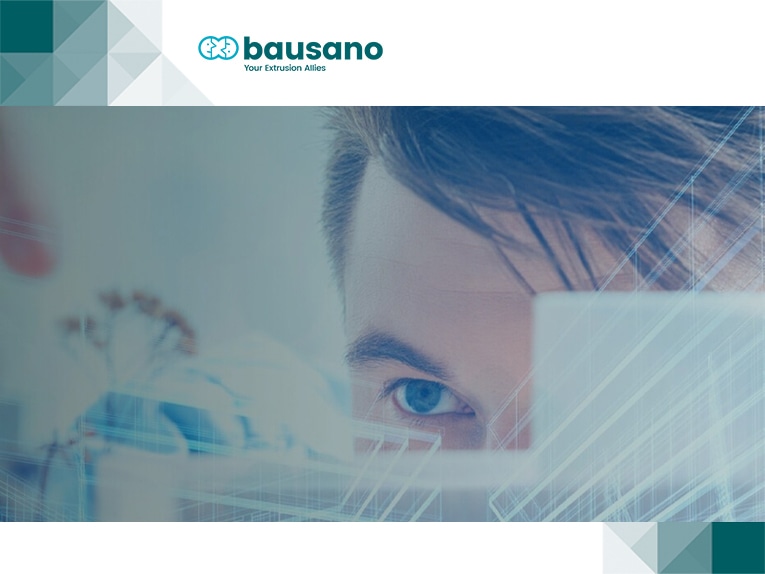
#Industry News
Converting natural gas to plastic
The term "plastic" suggests one material, but there are actually hundreds of different plastic polymers
Polymerization occurs when a chemical reaction causes molecules to react together to form polymer chains. These polymer chains can be engineered to control the specific physical properties of the resulting plastic resin, thus allowing the product to be designed for many different uses.
For example, some plastic products may require extra strength, some require maximum flexibility and others need to be resistant to solvents. All of these requirements can be accounted for by the polymers used in the process.
Polyethylenes may be labeled as low-density or high-density polyethylenes (LDPE or HDPE), or other designations that can be seen at the bottom of household containers. Rarely a day goes by without coming into contact with items made of plastic.
We see it all around, in everything from food packaging, medical equipment, furniture and vehicles, to toys, computers and clothing. But most people don't realize that natural gas is where a lot of plastic production starts.
The first stop in processing natural gas to plastic is the cracker plant. Crackers turn either naphtha, a crude oil-based product, or ethane, a natural gas liquid, into ethylene, a starting point for a variety of chemical products.
Ethane is formed the same way other hydrocarbons (e.g. oil and gas) are generated. Hundreds of millions of years ago, organic material such as plankton fell to the bottom of a seabed.