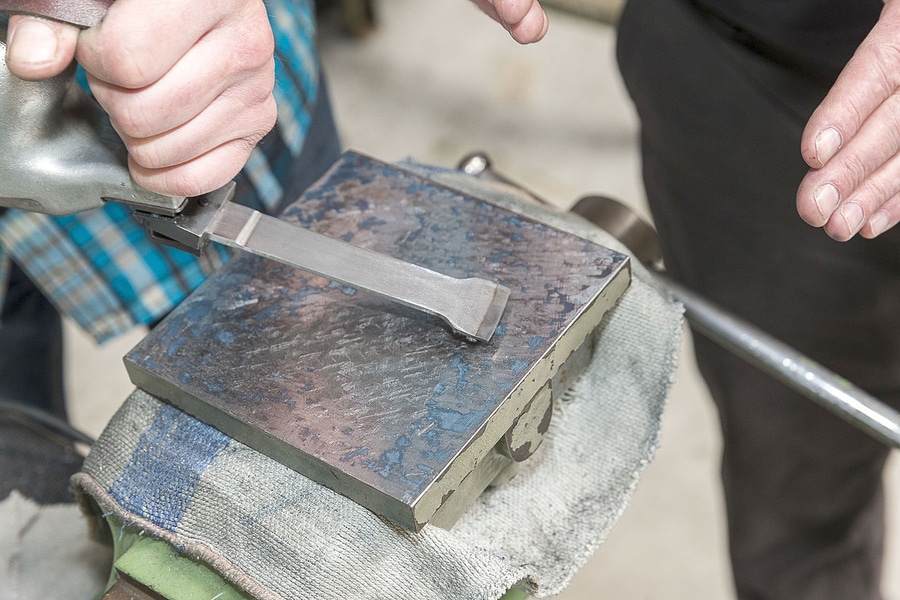
#Product Trends
The art of scraping
Scraping isn’t something that’s taught at vocational colleges and so the knowledge needed for the skills that scraping requires is gradually being lost. As a result, some workshops are attempting to stem the losses but face the problem that there is hardly any relevant training available. Biax recognised the challenge and consequently organised a training event that focused exclusively on scraping methods and invited Richard King, an “icon of scraping”, to be the instructor.
oung people in particular are only familiar with scraping from the stories they’ve heard from older colleagues. The task, which also requires great strength,
is to create very small depressions in the micrometre range on the machine
guide way surfaces in order to ensure sufficient lubrication and to reduce the loads that the guides need to absorb and so considerably increase machine life spans.
Scraping is particularly required for guide ways on presses, drills, lathes and milling machines. Smaller areas are often worked with hand scrapers but, of course, electrically powered ones are much easier to use as they don’t require so much strength and are up to 70% faster. In the old days, when high-precision
grinding machines didn’t yet exist, the guides on almost all new tool machines needed to be scraped out. These days, however, most manufacturers finish bottom guide lanes and top sliding surfaces with the help of high-precision grinding. The areas that need to bear loads on running surfaces are subsequently
usually worked by hand or electric scrapers. That’s why these days most scraping work, i.e. 95%, is carried out in the field of reconditioning used tool machines.
Scraping skills are passed down within companies from generation to generation. Everybody scrapes the way they were taught and think is right. That’s why incorrect methods are also propagated through the generations. And scraping has become a skill that is in danger of dying out. These days, it is frequently necessary to outsource scraping work to external service providers because there are just not enough young people to carry out the work that older generations used to do. So the fact that so few skilled workers now exist means that these providers are able to charge very high prices for their services. That’s why some companies are now attempting to restore scraping skills in their own workforces. But that’s where they face an almost insurmountable obstacle because training is not available in Europe and most of the very few surviving experts keep their cards close to their
chests because they possess a very exclusive skill. Demand exceeded all expectations The family-run Schmid & Wezel GmbH company, which is based
in Maulbraun in Swabia and which has been manufacturing the Biax electric scraper for over 50 years, saw what was happening and in response decided to organise an initial three-day training event for scraping and machine rebuilding
last April. “It was supposed to be an experiment and so we were genuinely surprised by the great uptake. We apparently hit a nerve of the time,” said Filipp Pachomow, Head of Sales at Biax. “The 10 available spaces were taken up so quickly that we could have easily filled several groups.” The training event was actually intended as additional support service for customers to help them restore lost know-how, he continued. We were pleasantly surprised to see the event attended by so many young people. The people in Maulbronn were able to acquire the services of Richard King, probably the world’s most famous expert in the field of machine rebuilding, as the scraping instructor. The 64-year old from the USA learnt “machine rebuilding” from scratch from his father, Hermann, who in turn was taught by German immigrants to the USA in the 1940s. Richard King has been teaching since the 1970s, Initially in the USA, but later also worldwide. The training event in
Maulbronn was the first of its kind in Germany. The three-day session focused primarily on basics: scraping by hand, the use of power tools and machine geometry. “You can’t expect more than a crash course in such a short time,” Richard King said. “A thorough training would require five days,” he said. The participants were still thrilled, however: “Richard has shown us entirely new techniques. Some of which were unusual and meant that we had to throw some things we had been previously taught overboard. But it’s worth it, you can increase your efficiency,” said one participant. Biax is planning further training sessions with Richard King for the autumn in response to the event’s great uptake.