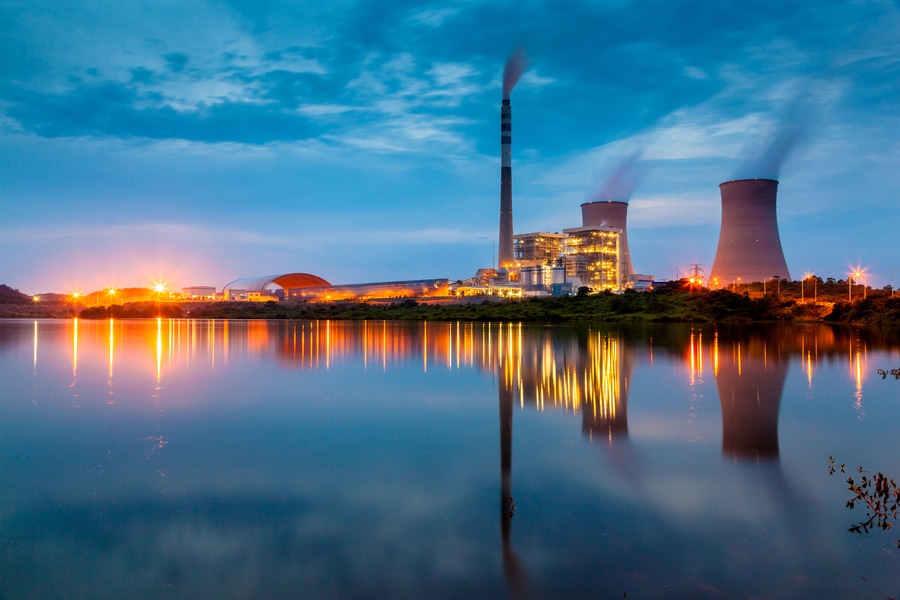
#Industry News
Interoperability of IEDs using IEC 61850 in practice
Interoperability of IEDs using IEC 61850 in practice
In 2004, the IEC 61850 standard was developed and issued, introducing state-of-the-art technology, also in the field of secondary circuits for power automation. Its aim was to completely move away from current practices of building analogue secondary circuits, replacing them with Ethernet and digital solutions.
At the same time, the standard defines communication interfaces and protocols for automation devices in an attempt to bring about their unification and interoperability between devices from different manufacturers, which was a very complex issue in the run-up to its development. Even before it was officially published, the standard received a great deal of interest from automation device manufacturers. One could say that there was a race to achieve compliance with the new standard.
The situation was quite different when it came to operating practices among electric traffic companies. The implementation of the standard in actual facilities is usually met with great caution, as its introduction completely changes current practices and habits. This applies not only to the implementation of secondary circuits, but also to the ways in which they are commissioned, tested and operated. Most of the previous experience would have to be thoroughly revised and rebuilt. Currently, the standard is readily used in automation equipment for communication with the control system, in many fields replacing previously used telecommunication protocols such as 60870-5 or MODBUS, despite the fact that to date there are only a few digital substation installations in the world fully implementing the IEC 61850 standard.
The first implementations of the standard in substations were recorded in 2005 in Germany and Switzerland [4]. These were not process bus based implementations but only used selected elements of the standard, such as network configuration, communication stack (MMS), standardised functions (logic nodes), commissioning process and testing. Despite this, advantages were pointed out, such as the scalability of Ethernet or the reduction of telecommunication links, resulting in less time needed for task coordination, final acceptance and testing. In addition, the advantages of using standardised function names defined by the standard were noted - it was possible to move seamlessly from requirements definition to design as soon as the order was received, saving time and eliminating potential errors. The SCL station description language allowed the creation of security configuration templates, which reduced commissioning time. The complex wiring in individual
fields, replacing them with an Ethernet connection. This saved time in laying cables, cable trays and terminals. Another advantage is that tests of automation systems based on Ethernet connections can be performed completely in the laboratory. On-site tests only had to be repeated for wire connections.