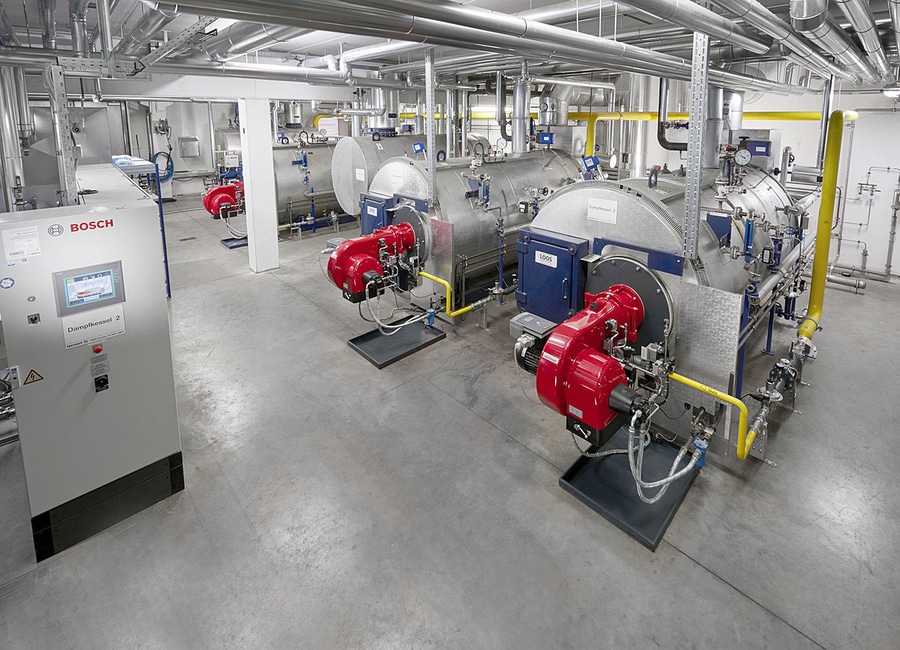
#Product Trends
Fleischwaren Sutter modernises process heat supply with boiler technology from Bosch
In collaboration with Bosch Industriekessel and the plant construction company Helmut Herbert, the Sutter Fleischwaren GmbH has modernised its steam boiler system at the main factory in Gau-Bickelheim. Thanks to the cost savings of around a quarter of a million Euros per year, it has been possible to successfully compensate the considerable increase in energy costs since installation of the steam boiler system. Furthermore, the operation of the boiler plant and analysis of operating data has been improved significantly by the new Bosch control system. The investment will be amortised after approximately three years.
In the course of a continuous plant optimisation, Sutter has introduced an energy management system for analysing savings potentials efficiently and evaluating them with regard to economic aspects. The process heat supply with three oil-fired steam boilers was quickly identified as one of the biggest energy consumers of the plant. Christian Böhme, the Energy Manager at Sutter, explains: "Prior to the modernisation we had been supplied with around 30,000 litres of light fuel oil – every week at another price. The switch to natural gas has improved our reliability of our energy cost planning. This is an advantage that we can pass on to our customers in the form of stable prices."
In the course of the modernisation, Bosch Industriekessel supplied new, modern dual fuel burners. The existing light fuel oil supply was maintained as backup. In case of supply shortages in winter times the natural gas supplier can request the short-term operation with light fuel oil. In return, the natural gas supplier waived a building cost subsidy for the laying of the gas pipeline. In comparison with the previous fuel oil burners with mechanical combined group, the new burners are electronically controlled. They are able to modulate down up to 350 kilowatt and thus facilitate a significantly quieter and more efficient part-load operation. In additon, the losses on the flue gas side have been reduced from six to five percent by using a combustion control with oxygen sensor.
In the area of control technology Sutter has opted for the modern Bosch control system consisting of the boiler control BCO and system control SCO. With the existing boiler control the supply of spare parts would have foreseeably become more difficult in the coming years. Besides the automated water treatment, the SCO includes the adaptive boiler cascade control in order to avoid standstill damages in the backup boiler. Furthermore, it automatically reports abnormalities during operation of a boiler to the superordinate control system.
During the introduction of a certified energy management system, the consumption figures need to be recorded on a regular basis to enable the analysis of energy saving potentials. Sutter opted for the superordinate control system Master Energy Control MEC from Bosch. Thanks to this system the energy manager and the technical managers can view the status of the system at any time from their working places and can easily evaluate the recorded data.