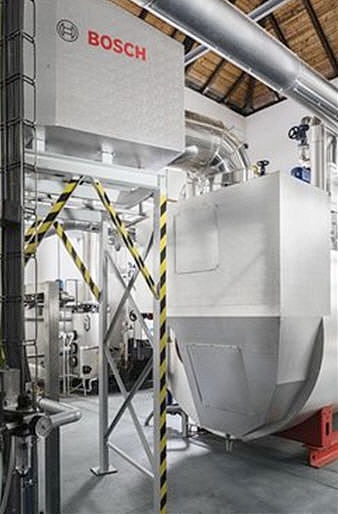
#Product Trends
New steam boiler from Bosch saves up to 16 percent energy costs
Pivovar Klášter brewery renews its steam supply
Mashing, boiling or keg and bottle cleaning: The production of beer is an energy-intensive process and thus needs an efficient and reliable steam supply. In the Pivovar Klášter brewery in the Czech Republic a steam boiler operated for over 30 years. In order to increase the reliability of supply and to reduce the running costs Pivovar Klášter decided to renew its existing energy system. With the new UL-S steam boiler from Bosch not only the reliability increased thanks to numerous automation equipment, the steam boiler also saves around 47 m³ of natural gas per hour. Around 75 percent of these savings are realised by the recovery of waste heat from flue gas. In total, the brewery saves up to 16 percent on fuel costs with the new system.
The first flue gas heat exchanger, the economizer, is used for preheating the feed water. Thus, the need for fuel for heating up and evaporation of water in the boiler is reduced. In the downstream heat exchanger the flue gas is additionally condensing. Due to the low temperature of this waste heat it is used for preheating the brewing water.
The shell boiler can provide 4,000 kilogram of steam per hour. The natural gas firing with modulating control ensures an elastic operating behaviour. The burner capacity can be adjusted continuously to the actually needed steam demand. It is thus possible to reduce the number of burner starts resulting in higher efficiency and prolonged lifetime of the boiler and burner. After downtimes the boiler can be started very gently from the cold state by using the intelligent automatic function SUC (start-up control).
The boiler control BCO provides easy access to important operating data like fuel consumption, boiler and burner operating hours or the number of burner switches. Further optimisation possibilities can be derived from this data. Furthermore, the BCO automatically controls desalination and blow-down. In comparison to a manual operation the demand-controlled process saves energy and water. In addition, the water service module from Bosch provides the boiler with deaerated feed water. This protects the system from corrosion and ensures a continuous high steam quality.
The perfectly matched components from Bosch provide a reliable system and allowed a quick and smooth installation. Zdenek Prokupek, director of Pivovar Klášter, is pleased about the good result and the cooperation with Bosch: "With the new system we have managed to reduce our energy costs significantly and thanks to the high degree of automation we can now completely focus on beer brewing. Both the quality as well as the local service from Bosch in the Czech Republic have convinced us."