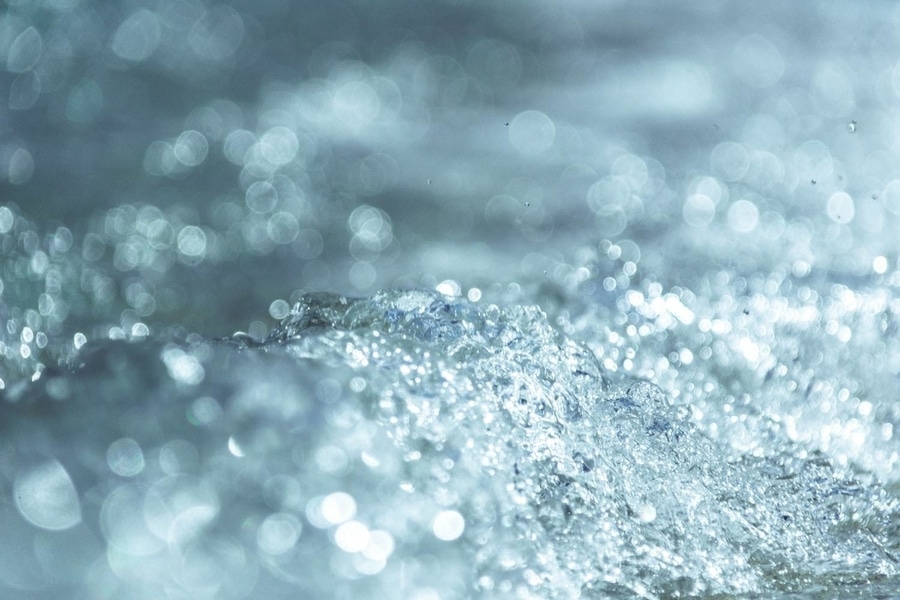
#Product Trends
Intrinsically Safe Tuning Fork Liquid Level Switch with NAMUR Output for Coal to Ethylene Glycol Liquid Level Measurement
After test trial, the client replaced all the original liquid level switches to Jiwei Ring-11 Intrinsically Safe Tuning Fork Liquid Level Switch with NAMUR Output.
Ethylene glycol is a chemical commonly used in many commercial and industrial applications including antifreeze and coolant. Ethylene glycol is an organic compound with the formula (CH2OH)2. It is mainly used for two purposes, as a raw material in the manufacture of polyester fibers and for antifreeze formulations. It is an odorless, colorless, sweet-tasting, viscous liquid. At present, there are three main processes for the preparation of ethylene glycol from coal-based, which are direct method, olefin method and oxalate method. Among them, oxalate method uses coal as raw material, and the so-called "coal to ethylene glycol" also refers to this process.
Jiwei’s client, a clean energy company in Jiangsu Lianyungang has been using liquid level switch for level measurement in coal powder pressurized convey device of ethylene glycol production, which requires the sensors have high performance.
Three Risk Factors in Coal to Ethylene Glycol Production
1. Toxic
Methanol, sodium nitrite, dimethyl oxalate and ethylene glycol produced in coal to ethylene glycol production are toxic and harmful substances. They have strong irritation to eyes, skin and mucosa.
2. High Temperature
In coal to ethylene glycol production, dimethyl oxalate is produced in the synthesis reactor at 120 ~ 145 ℃, and ethylene glycol is produced in the hydrogenation reactor at 170 ~ 210 ℃. As the high pressure steam temperature is up to 500 ℃, and the steam temperature used in the heat exchanger and distillation column in the whole reaction zone is above 100 ℃, the sensors should withstand the temperature above 100 ℃.
3. Inflammable and Explosive
The medium in ethylene glycol production is inflammable, explosive and hazardous, so requires high performance sensors with explosion-proof function.
Features of Jiwei Ring-11 Intrinsically Safe Tuning Fork Liquid Level Switch with NAMUR Output
NAMUR is an international user association of automation technology and digitalization in process industries. The term “NAMUR” is an acronym for a very long German description. NAMUR sensors limit current so that the current is not capable of causing ignition in hazardous atmospheres. A NAMUR sensor is usually powered by 8 VDC. When the sensor detects the target, the current flow through the sensor drops to less than 1.2 mA. When the target moves away from the sensor and is not detected, the current flow increases to above 2.1 mA.
NAMUR output is different from 8-16ma two-wire output, NAMUR output has smaller current and voltage, as well as lower power requirement of safety barrier. Therefore, NAMUR output has higher safety, and more suitable for explosive occasions.
Advantages of Jiwei Ring-11 Intrinsically Safe Tuning Fork Liquid Level Switch with NAMUR Output
● Four optional outputs: relay output, two-wire system, NAMUR and transistor.
● Certified for both Intrinsic Safety and Flameproof Enclosure explosion protection.
● High sensitivity due to the precisely pre-adjusted harmonic resonant frequency of fork, the lowest measurable medium density can be as low as 0.5g/cm³.
● With strong disturbance resistance ability, not influenced by foam, bubbles, viscosity, vibration and other liquid characteristics.
● Tines are made of 316L, can be lined with anti-corrosion coatings such as PFA, ECTFE, enamel, etc.
● The special setting of high-voltage protective airlight insulated bushing makes Ring-11 High-voltage Protection Liquid Level Switch effectively prevent accidental leakage of high-pressure strong corrosive liquid.
● Industry-leading performance for high temperature working environment. Process temperature can reach up to 250℃.
After test trial, the client replaced all the original liquid level switches to Jiwei Ring-11 Intrinsically Safe Tuning Fork Liquid Level Switch with NAMUR Output. The client also feedback that all the sensors have been running well beyond expectations for nearly a year since the installation, and in the new phase II project he will definitely use Ring-11 tuning fork level switches again.
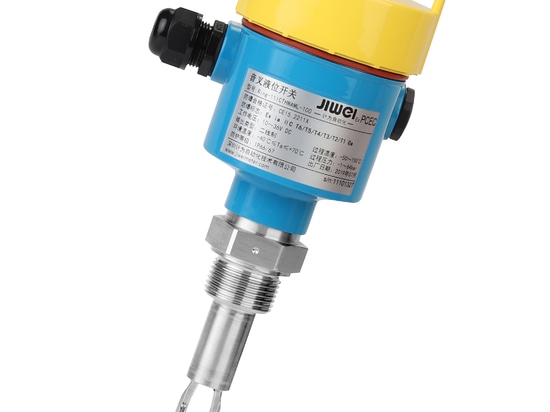
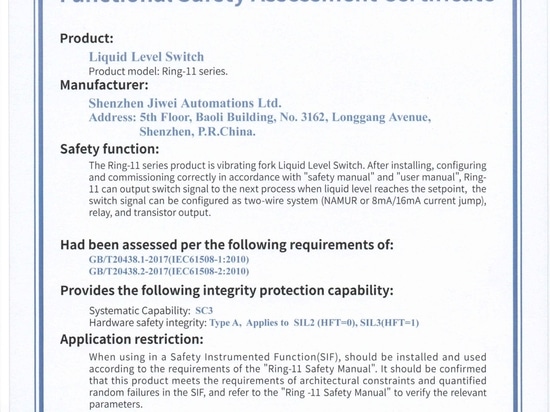