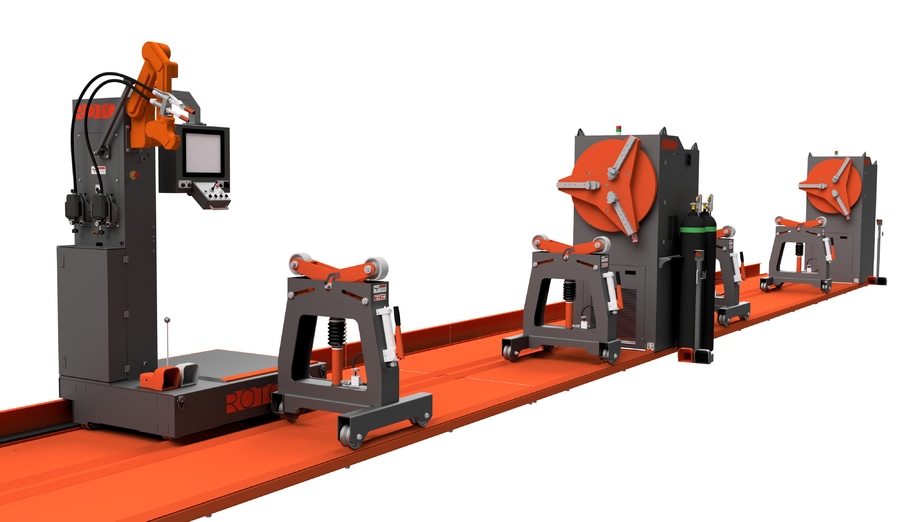
#Industry News
Rotoweld 3.0™ Keeps Leading the 4th Industrial Revolution in Pipe Spool Welding
The modern challenges in spool welding, The Industry 4.0 trend, A description of the Rotoweld 3.0
Industry Overview
The modern challenges in spool welding
Pipe spools are pre-built parts of a piping system. It is a term that covers pipes, flanges, and fittings. Pipe spools are commonly used in industrial constructions such as oil- and gas production facilities, power plants, refineries, and petrochemical plants. The spools are manufactured precisely by following several steps such as cutting, beveling, welding, or other processes depending on the requirements.
It can be very difficult to find the right welders to weld the pipe spools. There is a shortage of highly skilled and qualified welders in the pipe welding industry, which makes them expensive. Furthermore, the pipe welders are constantly making decisions about for example the torch angle and travel speed. It is proven to be extremely difficult to produce repeatable and consistent high-quality welds, as humans are prone to error. To deal with these problems, automated welding robots can be the solution.
The very dynamic field of automation in spool welding
There are many different possibilities when automating the pipe spool welding process. The welding process itself can be automated with robots and automated welding machines, but also the activities around the welding process can be automated. For example, conveyor belts transport the spools to the right place in the shop or robots to move the parts into position to be welded. In these cases, the process of spool welding is partially automated, but a qualified welder still manually welds the pipe spools. But the fact that pipes are mostly used for transporting dangerous gasses or liquids, there is almost no room for errors. This leads to an increase in automated pipe spool welding.
The Industry 4.0 trend
Industry 4.0, or sometimes called Smart Industry, is the name for a trend of automation for industrial manufacturing. This trend continues in industry 3.0, whereby machines are automated, but mostly run-on human input. The machine is simply following a set of programmed parameters, created by a human. With industry 4.0, the machine can use its data to streamline the production processes without the need for human intervention. The machines can connect and communicate with each other via the Internet of Things to become more efficient. The automated pipe spool welding machines by Tecnar fits in well with this trend.
A brief history of the Rotoweld
The reality of the show floor in automation and the idea of the Rotoweld
Back in the 1980s, many companies were developing vision systems for welding automation. "This was a period when a lot of vision systems were being developed," Tecnar's founder, Francois Nadeau said. "If you went to the welding trade shows at the time, you often saw about 15 companies that were putting together vision systems for welding automation." Many of these vision-system companies are not around anymore, mainly because manufacturers found it more cost-effective to adapt processes to automation by making weld preparations more consistent. But pipe spool fabrication is different.
This is when Nadeau came up with the idea of automated pipe spool welding machines, as he explains in an article on The Fabricator. "It's not practical to have a perfect, repeatable preparation," Nadeau said. “You'd have to re-machine all the flanges and pipe ends. It's a delicate operation with a [weld] preparation that by nature will vary. ''
This is where Nadeau and his team saw an opportunity. For years, pipe welding operations had installed automated systems for the cover and cap pass, but they had yet to automate the root pass successfully. If the fabricator had any automation at all, it required additional handling between the hand welding and the automated station. "So we focused on this," he said, "and developed a vision system and control strategy that varies the welding parameters dynamically to control the penetration of the root pass." This was the start of the Rotoweld.
Tecnar is a family-owned company that was founded in 1989 as a spin-off from Canada's National Research Council. Tecnar has 30 years of experience in automated pressure pipe welding and more than 150 commissioned Rotowelds around the world.
Nowadays, Tecnar has expanded to four distinct product lines that share a common goal: to make a difference in the daily life of its clients by integrating its technology and know-how.
4D Synergy ™ welding
Tecnar's Rotoweld features 4D Synergy welding, which is a unique patented technology that features all welding parameters in a single joystick command. This results in a unique machine that is so easy to operate that an operator can fully function in less than one week. Arc voltage, oscillation width, travel speed, and wire-speed all vary following a single movement of the Rotoweld's joystick. This ensures the arc and weld puddle dynamics are maintained in ideal conditions. The computer's fast reaction time means the machine can work at high deposition rates and travel speeds at which weld pool conditions are too critical to be sustained by hand.
Rootmatic ™
Rootomatic is the ultimate level of Rotoweld automation when it executes a root-pass in record time with its fully automated weld penetration control. It performs a 100% automatic open-bevel root pass at high travel speeds. It tracks the position of the puddle and the arc to ensure a complete fusion of inside edges. It can also adapt to the presence of tacks while welding to produce a smooth weld bead ready for the first fill pass. The 4D Synergy welding technology, together with the real-time image processing of the welding process, enables the machine to adapt quickly to varying conditions such as changes in the gap, alignment, and root face which results in the most adaptive automated root pass welding ever engineered.
Rail-based design = productivity
One that knows about fabrication will tell you that it is not just the deposition rate that matters. Actually, very few fabrication shops are limited by deposition rate. They are far more affected by set-up times, fit-up delays, and transitions from one joint to the next. When designing the Rotoweld 3.0, Tecnar made sure to engineer the product that optimized each and every step of the fabrication process on top of the high speed at which it is already welding.
And it is fundamentally a question of alignment. The Rotoweld 3.0's rail-based design is key to automation as it is the link between the welding robot, the support rollers, and the pipe rotators. It is essential to ensure reproducible positioning of the welding torch and the same welding position every time, regardless of the diameter of the pipe or length of the spool assembly. The Twin Bay's welding robot is seamlessly carried to a second welding station along the rails, so the Twin Bay model eliminates set-up time and increases productivity. When one pipe is being welded, the next one can already be prepared. What is more, is that all the welding cables are embedded in the rail design for safer and simpler shop operations.
A description of the Rotoweld 3.0
The ease of use and reliability of standard components
The Rotoweld 3.0 is specialized in automated pipe spool welding. Every component has been engineered to ensure the highest standards of productivity, quality, and reliability. Thanks to the 4D Synergy welding technology, minimal welding experience is required. It features all welding parameters in a single joystick command. Operators can be trained to perform ASME Section 9 welds in less than one week. Furthermore, the operators do not need to get close to the arc thanks to the camera-based welding arm, leaving them free from UV exposure, which is an important cause of skin injury and long-term concern for welders.
The robotized arm for ease of positioning
Upon loading the proper welding program, the Rotoweld's welding arm, driven by zero-backlash harmonic drives, will position itself automatically, respecting the pipe diameter and indicated stick-out. The welding vision system controls the puddle penetration and adapts welding parameters in real-time. The operator can follow the entire process on screen thanks to the integrated camera in the welding torch. Embedded LED lighting allows the welder to easily align the torch in the command before starting to weld.
The specifications
The Rotoweld 3.0 is designed with 2 welding torches: one to perform open-root-pass butt welds and the other for filling passes. Each torch has its own wire spools. The welding arm is self-positioning in just a few seconds with no human manipulation. Root pass is done in GMAW and fill passes can be chosen between GMAW, FCAW, MCAW. It is available as Single Bay and Twin Bay for pipes with a diameter between 3 and 42 inches and with a pipe stand capacity of 4,535kg. Both models are also available as heavy-duty; for bigger or heavier pipes with a diameter from 3 up to 48 inches and a pipe stand capacity of 6,804kg. The Single Bay increases daily production capacity with 150+ dia inch whereby the Twin Bay increases the daily production capacity with 300+ dia inches. As a rule of thumb, typical Rotoweld 3.0 welding times are as follows: 1 min.
The Single Bay had a width of 7.5 ft. and a length of 30 ft. The height is 8.8 ft. whereby the HD has a height of 11.5 ft. The Twin bay has the same dimensions, except the length, with is 77 ft. for both the regular as the HD.
The software
The Rotoweld user interface (UI) is designed with proprietary operating software to be simple, easy to use, and efficient. The Rotoweld UI features a large central image to ease torch positioning using the LED vision system to increase welding precision and a welding program to facilitate the tracking of critical welding settings and the uploading of new welding programs. The live display shows all welding parameters, including welding current and live heat input. A simple log-in function allows Rotoweld operators to easily enter the ID and job number of work in progress.
The Rotoweld 3.0 has a Lincoln Power Wave welding source. The Root pass - STT and the Fill Pass - GMAW are Lincoln Power Wave S500. The Fill Pass - SAW is Lincoln Flextec 650. All specifications can be found on the website www.rotoweld.com .
Additional options
The Rotoweld has been around for over 30 years and Tecnar has been improving the machine to respond to the needs of the industry. Many options are available for a new or an existing Rotoweld.
Submerged Arc: Get the advantage of achieving a root pass and SAW filling on the same machine while reducing the handling time, simplifying the shop operations, and improving productivity. The SAW option features a dedicated twin torch holder with the MIG root pass torch and SAW torch kit for 3/32 wire. That means it takes less than 20 minutes to change the Rotoweld from the MIG-MIG to the MIG-SAW configuration. The SAW option comes with a Lincoln Flextec 650 power source plus a 100-pound flux pressure feed tank. The proprietary designed flux recovery bins, engineered to be easily emptied, are a great advantage of the SAW option. They are mounted directly on the idler rolls so they can be easily placed under the joints and can be swapped from one side of the idler roll to the other in just 5 minutes. The Rotoweld ' s LED vision system allows the SAW torch to be positioned on top of the pipe while safely staying on the welding carriage. The SAW vision mode also provides a linear guide as an overlay on the screen to help the welder create a smooth surface finish between passes.
Flux core / metal core: The Rotoweld can easily be switched between MCAW and FCAW. All that is needed are adopted feeder rolls. Furthermore, if a Rotoweld is dedicated to stainless steel operations, then it is best to go for the highest standard and have all the grippers changed to stainless steel. If any contamination has to be avoided, the Rotoweld idler rolls can be ordered with high-capacity rubber sleeves that can sustain 15,000 lbs. / 6.804 kg of load while keeping the spools clean and smooth.
Fume extractor: Welding fumes can be a threat to the welder's health and it can make the shop environment an uncomfortable workspace. And with the labor crisis in most developed economies, providing a safe work environment has become mandatory. The Rotoweld 3.0's fume extractor is a self-positioning hood with a welding carriage. It is easy to install and more affordable than wall-mounted systems. Furthermore, it is also more environmentally friendly. It is silently operating at the welding station and the pump and filters are easy to access. The filter can surface an area of 520 sq. ft. and is self-cleaning.
The installation: It is possible to have the Rotoweld installed and fully operating in one week. When self-installing the machine, it is even possible to have it installed in one day. The machine operator can be trained to perform ASME Section 9 welds in less than one week.
The support: Tecnar takes pride in offering the best manufacturing/engineering warranty and support in the business so you can rely on Rotoweld 3.0 technology for years to come. With over 150 Rotowelds at work around the world and 30 years of experience in automating spool shops, Tecnar's service team is more than qualified to help you. They use the client's Rotoweld Prodatalog information to benchmark their shop's productivity, identify areas for improvement and offer solutions based on their expertise.