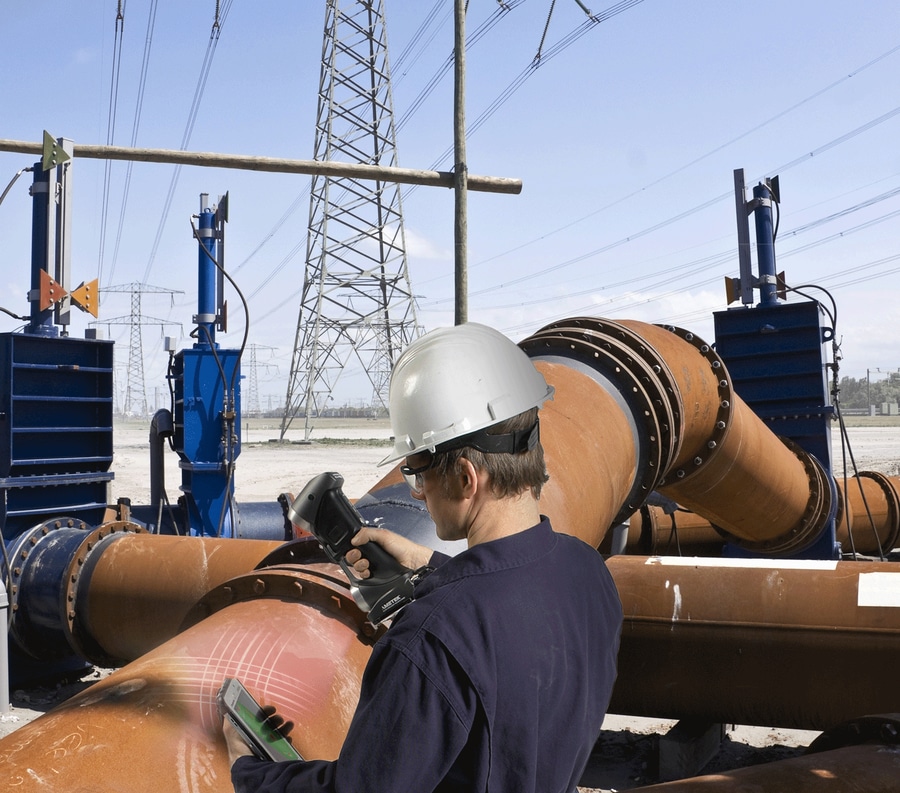
#Product Trends
3D SCANNING FOR NON-DESTRUCTIVE TESTING (NDT) IN REFINERIES
On-site Corrosion Control on a Column Skirt
DEKRA Industrial is one of the leaders in the prevention of industrial and occupational hazards in France and Europe. With its expertise to identify and assess hazards, the company plays an instrumental role in risk prevention for a variety of companies.
Material inspection, which mostly take place in the French region of Lyon, encompass a wide range of conventional and non-conventional NDT services and tools, such as conventional and phased array ultrasonic testing, time-of-flight diffraction (TOFD), Eddy current, robotics, electromagnetic acoustic transducer (EMAT), conventional and digital X-ray inspection, 3D laser measurements, alternating current field measurement (ACFM), thermography, Lixi Profiler, guided waves, AcousticEye and surface inspection.
Case Study: On-site Corrosion Control on a Column Skirt
3D scanning for non-destructive testing (NDT)
Since the fall of 2014, DEKRA Industrial has been using the HandySCAN 3D scanner and VXelements data acquisition software with Pipecheck, the software platform used to assess corrosion and mechanical damage in pipelines, refinery columns, and storage tanks.
"We made the decision to invest in Creaform’s 3D scanner and software as the solutions would allow us to perform all applications and tasks usually required in typical NDT environments with the flexibility that we needed. It is the best tool to effectively control pipelines, skirts or columns—even when access is difficult and no power supply is within reach," explained Nicolas Cricoveanu, Head of Advanced NDT at DEKRA Industrial.
Application
One of DEKRA Industrial’s recent NDT applications was to control the external corrosion of a column skirt in a refinery.
The skirt had a diameter of 3 m and the surface to inspect started at a height of 0.6 meters and ended at 2 m,with a nominal thickness of 10 mm. The skirt interior was covered with a concrete layer that prevented access to the opposite surface. The surface itself was complex and included many support plates, cavitations, manholes, insulation supports (about 50 on the control area), guards and mounting bolts. The objective was to control 100% of the accessible surface.
As the state of deterioration of the external surface was too advanced to proceed with a conventional ultrasonic control or to use a manual pit gauge, the HandySCAN 3D and Pipecheck software allowed operators to scan the surface in 3D to assess the most damage around the skirt’s circumference. Later, the results were presented in an official inspection report generated in Pipecheck.
Methodology
1. Once the surface is prepared (sanded and with its insulation removed) by on-site contractors, positioning targets are applied to it. Positioning targets allow the scanner to triangulate its position against the control surface during the 3D data acquisition process. Estimated time: 1 hour.
2. Reference arrow positioning allows the positioning of the indications in relation to X and Y references identified beforehand.
3. Positioning target acquisition and 3D surface scanning (approx. 20 m2 with a resolution of 1.5 mm). Estimated time: 45 minutes.
4. Data recording and site cleaning and restoration after inspection. Estimated time: 30 minutes.
5. Data processing and preparation of the inspection report. Estimated time: 12 hours.
The above application and methodology are based on the control of a 20 m2 surface carried out by DEKRA Industrial during a single intervention. This will enable the company to reduce data processing times in the future.
Before making the switch to Creaform's inspection system, DEKRA Industrial used a manual pit gauge and ultrasonic controls to inspect surfaces when their opposite surfaces were accessible and in good condition. However, in this case, the state of the surface would not have allowed for manual control according to the tests carried out before DEKRA Industrial's intervention. The method used with Creaform’ssolution provided relevant results—all while reducing control times. Had DEKRA Industrial used a manual pit gauges, it would have required a minimum of 3 to 4 hours without providing guaranteed results.
Nicolas Cricoveanu is thrilled with Creaform’s results. "The external damage assessment provided reliable high-quality results. We can now perform controls more quickly and accurately than with manual tools. As such, both the service provider and the client benefit from productivity gains since it greatly reduces downtimes due to control operations."
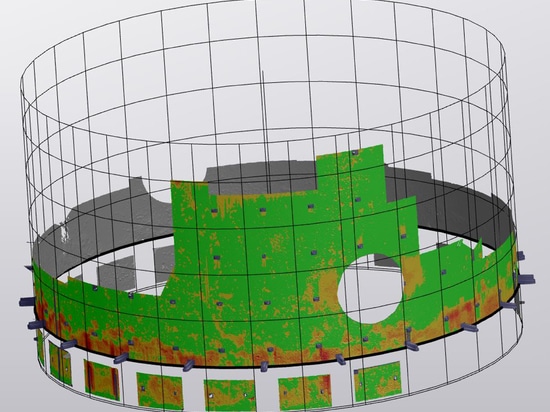