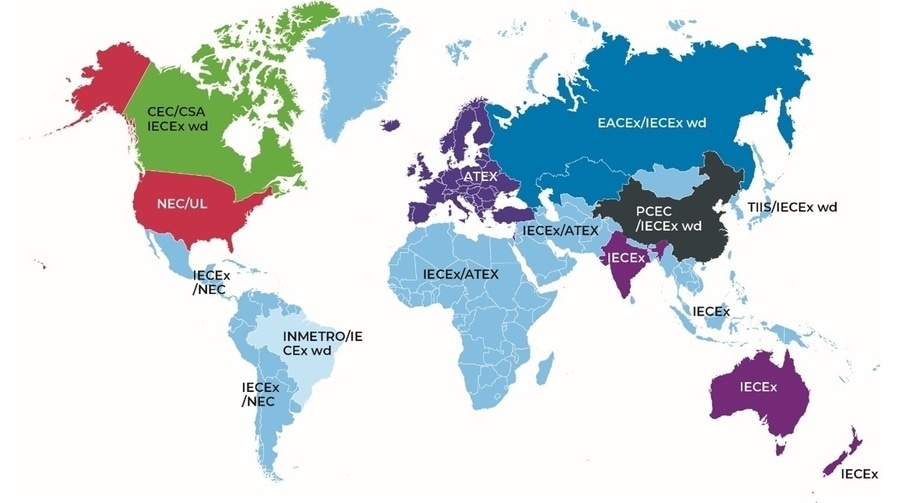
#Industry News
Why is the Cygnus 1 Ex so unique?
The Cygnus 1 Ex is Intrinsically Safe, certified to Zone 0, suitable for hazardous areas. There are a number of impressive statements we have used to introduce our Cygnus 1 Ex Ultrasonic Thickness Gauge, but what do they all really mean?
The Cygnus 1 Ex is Intrinsically Safe, certified to Zone 0, suitable for hazardous areas. There are a number of impressive statements we have used to introduce our Cygnus 1 Ex Ultrasonic Thickness Gauge, but what do they all really mean? Let’s demystify these statements and explain the rules and regulations surrounding the use of equipment in hazardous areas.
WHAT ARE EXPLOSIVE ATMOSPHERES?
The term Ex is recognized globally for explosive atmospheres and the schemes used to prevent explosions.
Hazardous Areas are locations where there is a risk of fire or explosion, due to the presence of ignitable or flammable substances in the air. These substances include gases, vapours, and dusts that are present in the air, at concentrations high enough to produce an ignitable mixture.
EX SCHEMES & STANDARDS AROUND THE WORLD
Like the term ‘Ex’, these schemes are named as such that they too can be recognized globally. ‘IEC’ is an UN-endorsed standard used to provide a common point of reference for understanding the variety of different Ex rating standards that are used around the world. The ‘IECEx system’ is a certification to standards relating to equipment for use in explosive atmospheres. This map shows which schemes and standards are adhered to in each country.
From the map, you will notice Ex systems are used around the world and most systems are based on IECEx. Regions like the European ATEX Standard and the North American NEC/UL Standards use the IEC 60079 Standard as a source:
• NEC / UL Scheme (North America) - UL 60079
• ATEX scheme (European) - EN 60079
• UKEX Scheme (United Kingdom) - BS EN 60079
• INMETRO Scheme (Brazil) - EN 60079
Cygnus 1 Ex gauge has been approved to IECEx, ATEX and UKEX requirements, and is the ONLY gauge that meets the highest classification of ATEX Zone 0, which is equivalent to NEC (UL) Class I Division 1 Group “ALL”.
WHAT ARE ZONES & DIVISIONS?
These are hazardous area classifications:
• ‘Zones’ is the term used within the European ATEX scheme
• ‘Classes’, ‘Divisions’ and ‘Groups’ are terms used within the North American NEC/UL scheme
In both the IECEx and ATEX Systems hazardous areas are classified into Zones based on an assessment of the frequency of the occurrence and duration of an explosive atmosphere:
• Zone 0 - An area in which an explosive gas atmosphere is continuously present or for long periods;
• Zone 1 - An area in which an explosive gas atmosphere is likely to occur in normal operation;
• Zone 2 - An area in which an explosive gas atmosphere is not likely to occur in normal operation and, if it occurs, will only exist for a short time;
• Zone 0 is the Most Hazardous Area.
In the North American NEC/UL Ex scheme Divisions are used in place of Zones:
• Division 1 = Zone 0, Zone 1
• Division 2 = Zone 2.
Plants and facilities will have many different Zones or Divisions. Once these hazardous areas have been established, signs must be installed to warn and inform anyone entering the area.
It is important to be aware that these area labels can change, especially, for example, as a result of a leak. If a welded joint, flange or valve is leaking, the Zone around it can be elevated from Zone 1 to Zone 0.
EX STANDARDS VS. OTHER TESTING METHODS
There are other methods for testing equipment in hazardous areas, but it is important to be aware how they differ from Ex standards.
The MIL-STD-810G only tests a piece of equipment to see if it can cause an explosion on the day of the test, without taking into account use in the field, being dropped, becoming faulty or batteries short circuiting. This means it provides no guarantee that the equipment cannot cause an explosion.
Ex on the other hand, provides assurance that the equipment, even if faulty, cannot cause an exposition. The equipment must be DESIGN to be safe. Redundant safety circuits are designed in, so if one fails the next will still provide protection. Equipment is drop tested, IP tested, batteries are short-circuited to check they don’t explode or get hot. Materials used must be alti-static to avoid the build up of static charge that can cause sparks.
Below illustrates the differences between Ex and MIL-STD-810G:
• Ex to ISO 60079 (IECEx / ATEX / UKEX / INMETRO / NEC-UL) >> MIL-STD-810G (Method 511.5, Procedure I.)
• Equipment must be safe by design. >> This is a simple test done in an explosive atmosphere. The test operates equipment in a 4% n-Hexane fuel/air mix to see if it causes an explosion.
• A notified body examines the equipment and issues an Ex Certificate if standards are met. It is legally binding. Equipment manufacturers are regularly audited to ensure compliance. >> This is NOT an Ex Certification (no certificate) and the equipment is NOT Ex certified.
• An EPL is stated to clarify which zones it can be used in. >> The equipment CANNOT be taken into an Ex zone.
• Multiple fault conditions are applied and considered. It requires the use of redundant safety circuits. >> NO fault conditions are applied. NO battery sparks are considered. NO drop testing is done. Static electric build up is NOT considered.
Look out for the next article, which explains what we mean by ‘Intrinsically Safe’, what Equipment Protection Levels (EPLs) are and what you need to know about Hot Work Permits.
Cygnus 1 Ex, like all other Cygnus products, is manufactured in the UK and has a 3 year warranty.