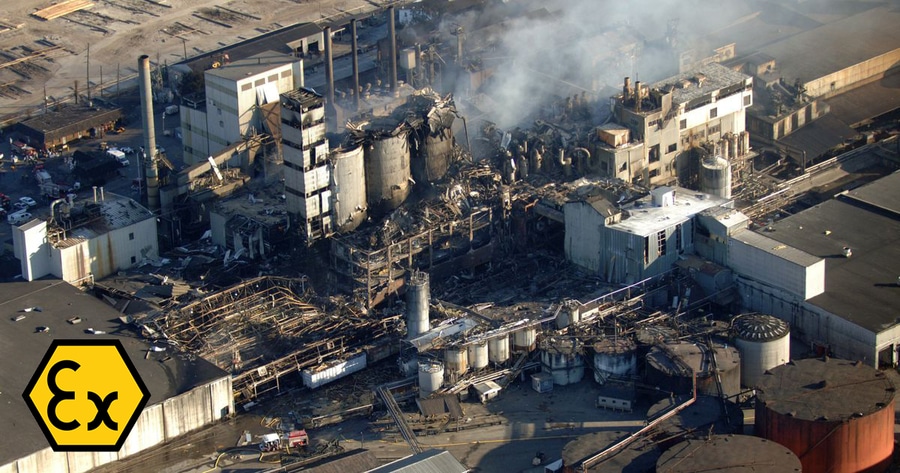
#Industry News
Risk of explosion during potentially hazardous dust handling and removal
Delfin solutions wth ATEX certification
Dust removal is among the most common cleaning requirements in a company, regardless of whether it is a productive or a logistic activity.
The dust to be removed is frequently different from the atmospheric one or the one caused by dirt. Usually, the real hazard is represented by the dust generated or used in production processes. In fact, this material is frequently combustible and may cause an explosion, under certain circumstances. As a matter of fact, all organic, synthetic, or metal dusts with a granulometry lower than 500 microns, may pose this threat as much as inhaling flammable liquids.
That’s why, during the last 30 years, Delfin has been offering a range of ATEX certified vacuums that allows to carry out cleaning and maintenance operations in total safety.
One question arises: What is an ATEX certified industrial vacuum? When is it useful for a company to evaluate its purchase?
In order to make the right choice, it is fundamental to understand the European ATEX regulations and how they are applied in the choice and supply of an ATEX industrial vacuum for explosive dust.
ATEX
The word ATEX identifies an explosive atmosphere. So, when it comes to ATEX, we refer to the equipment specifically designed to be used in atmospheres and environments with potentially explosive gas or dusts.
Among these, we can find many materials “of common use” like:
• Natural organic substances (flour, sugar, cereal, alfalfa etc.)
• Synthetic organic substances (plastics, pigments, pesticides, chemical products, oils, hydrocarbons etc.)
• Coke carbon and synthetic fibers
• Metals and powders with no link to the organic compound (aluminum, magnesium, zinc, iron, etc.)
CONDITIONS UNDER WHICH AN EXPLOSION TAKES PLACE
In order for an explosion to occur, the presence of potentially explosive material is not enough. In fact, some other necessary conditions must occur in the right percentage or within a defined time frame. These conditions can be found in the Fire Triangle.
The Fire Triangle is made of:
- Oxygen
- Heat source
- Fuel
When it comes to dusts, considering the Fire Triangle, the explosion occurs:
- If the dust is considered as combustible
- If the dust forms a cloud
- If the dust has the necessary granulometry
- If the dust clashes against a trigger of sufficient energy
- If there is enough oxygen
ATEX DIRECTIVE
Speaking of ATEX regulation, there are two European directives explaining and officializing this topic:
- The directive 2014/34/UE is addressed to ATEX certified equipment manufacturers. This directive regulates the harmonization of different States’ regulations with the manufacturing of equipment and protection systems intended for specific use in potentially explosive atmospheres.
- The directive 1999/92/EC is addressed to the equipment users. This directive provides the useful information to define those areas in which, in a workplace, a person can be exposed to the risk of explosive atmospheres due to the presence of gases, vapors or mists and/or combustible dusts. This directive defines the “risk-areas” of a workplace.
Identifying the risk areas in a workplace is essential to identify the best certification when looking for machinery. This is responsibility of the machine user.
The danger zones identified in the directive are:
- ZONE 22 for dust, ZONE 2 for gas: low risk
It is unlikely that the conditions for an explosion may occur and if they do, it’s just for a short period of time (less than 10 hours in a year).
- ZONE 21 for dust, ZONE 1 for gas: medium risk
It’s likely that the conditions for an explosion may occur sporadically during the ordinary functioning (among 10 and 1000 hours in a year).
- ZONE 20 for dust, ZONE 0 for gas: high risk
The conditions for an explosion occur continuously and over long periods of time.
For each risk area listed above, the directive has associated a certification that the machinery must have:
Dust
ZONE 20: CATEGORY 1D
ZONE 21: CATEGORY 2D
ZONE 22: CATEGORY 3D
Gas
ZONE 0: CATEGORY 1G
ZONE 1: CATEGORY 2G
ZONE 2: CATEGORY 3G
DELFIN SOLUTIONS WITH ATEX CERTIFICATION
Given the conditions for an explosion to occur and the related legislation, how does Delfin guarantee its customer the safe handling and removal of dust when using a vacuum cleaner?
Some of the major causes of triggering when using an industrial vacuum are:
• Static electricity and power continuity on equipotential surfaces
• Penetration and contact of dust/gas inside electric components
• Mechanical sparks
• The achievement of maximum surface temperature
Keeping all these features in mind, Delfin R&D department has developed a wide range of vacuums to prevent these risks to occur on the vacuum cleaner. Moreover, some specific Delfin products that can be used in all ATEX areas have been certified by accredited external agencies and internally tested.
Once identified the risk area where to use the vacuum, Delfin will be able to provide all the necessary guidelines to choose the most suitable vacuum:
- Compressed air
- Electrical
- For continuous use
- For intermittent use
- For dusts
- For liquids
There are so many different industries where Delfin ATEX vacuums are currently being used: food, pharma, 3D printing, chemical, agri-food and many others.
For sure, one of the most innovative application fields is 3D printing. Indeed, among the powders used by these state-of-the-art machines are some highly explosive metal powders. Using a Delfin industrial vacuum makes it possible to remove the excessive dust during the printing process. This enables the operator to reuse the same powder while guaranteeing his/her safety and the printer and the environment’s total cleaning.
Many international key players manufacturing 3D printers have already chosen Delfin to combine their machines to an industrial vacuum to increase both efficiency and safety during their use.
Same for material handling: with a wide range of ATEX certified pneumatic conveyors, Delfin ensures the maximum operators’ safety in the working environment. In the meantime, a pneumatic conveyor, as an integration of the production plant, can ease material transfer within the plant while eliminating any risk of cross-contamination or powder dispersion, even in an ATEX area.
For immediate information, contact us for the most suitable machine for your specific requirements.
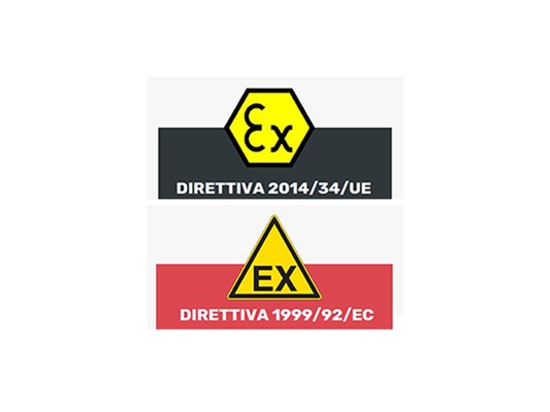