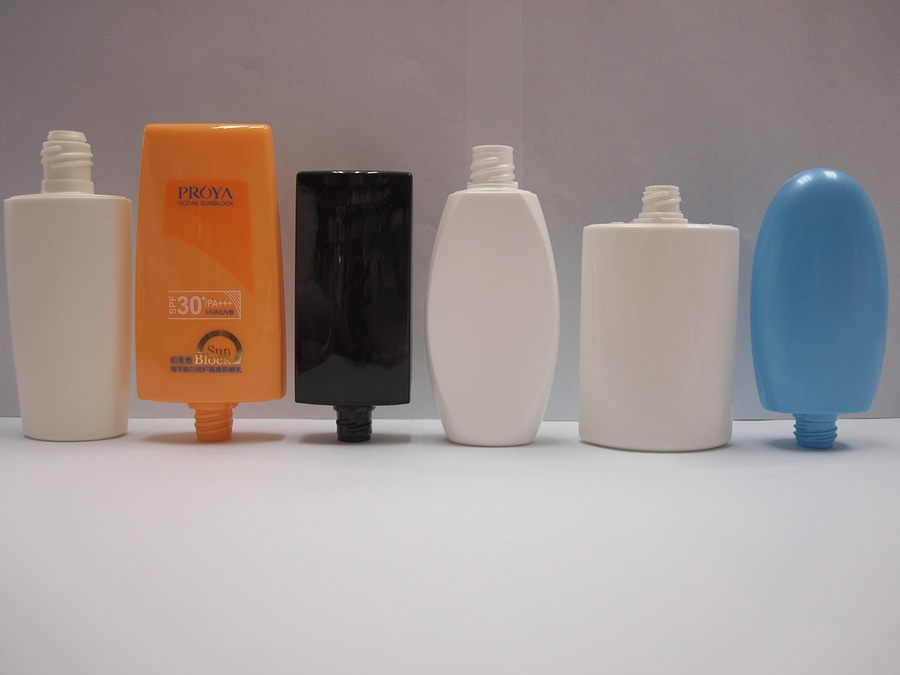
#Industry News
The Introduction of extrusion bottle blow molding production process
Extrusion blow molding (EBM) is a hollow extrusion blow molding process.The process principle is that through the extrusion system of the blow molding equipment, the resin is heated to a molten state and then extruded from the die to form a tubular parison, which naturally droops into the mold to form a blow molding parison.
Extrusion blow molding (EBM) is a hollow extrusion blow molding process.The process principle is that through the extrusion system of the blow molding equipment, the resin is heated to a molten state and then extruded from the die to form a tubular parison, which naturally droops into the mold to form a blow molding parison.After the mold is closed, the blowing air rod blows compressed air into the interior of the parison through the air nozzle to inflate the parison, and then relies on the mold to cool and shape to obtain the required hollow product. After the product is formed, it is automatically trimmed on the machine, or in the later stage. Secondary processing removes edge materials.
Product formation mainly goes through the following four core processes: 1. Resin plasticization and melting; 2. Extrusion of tube blanks; 3. Blow molding; 4. Product demoulding; 5. Automatic shearing of edge materials; 6. Product and edge materials Sorting export.
Extrusion blow molding is divided into two major steps: extrusion and blow molding:
step1: extrusion parison-mold closing
- The extrusion device continues to squeeze to form a hollow tubular parison
- When the parison is extruded to a predetermined length, the top end of the parison is cut to a suitable length for a single piece, and the molds on the left and right sides are closed
step2: Air import-Trimming and finishing
- Compressed air is injected into the parison through the mandrel for inflation.
- When the parison is extruded to a predetermined length, the top end of the parison is cut to a suitable length for a single piece, and the molds on the left and right sides are closed.
Characteristics of extrusion blowing process
Advantage:
1. The product is formed in one step, the technology is mature and reliable, and the multi-station extrusion blow molding machine has higher production efficiency and strong versatility.
2. It is suitable for the blow molding production of various raw material resins. The molecular weight of blow molding grade plastics (such as PE, PP) is high. The product has high impact toughness and high environmental stress cracking resistance.
3. Product appearance design has high degree of freedom, mold design and development cycle is fast, and mold cost is relatively low.
4. Extrusion blow molding can form products with complex, irregular and integral shapes. Special-shaped die can be used to produce products with a large flatness ratio. Such as 4L and larger hollow containers with hollow handles.
5. The net weight and wall thickness of the product can be randomly fine-tuned according to process needs without trimming the mold. It is easy to meet the minimum wall thickness requirements of products and save raw material costs.
6. Suitable for the application of multi-layer co-extrusion technology to meet the production needs of high-barrier (2-6 layers) products.
Limitation:
1. There will be a mold closing line at the mouth or bottom of the product bottle, which will slightly affect the appearance.
2. During the extrusion blow molding process, conventional products will have 20-30% scraps, which need to be recycled and reused.
3. The dimensional accuracy of the product bottle mouth is not as good as that of injection-blown products.
Summarize
- Injection blowing and extrusion blowing are different hollow container forming processes
- Each has advantages and limitations
- Apply to different usage conditions according to their respective characteristics
- The two processes coexist and cannot simply replace each other.