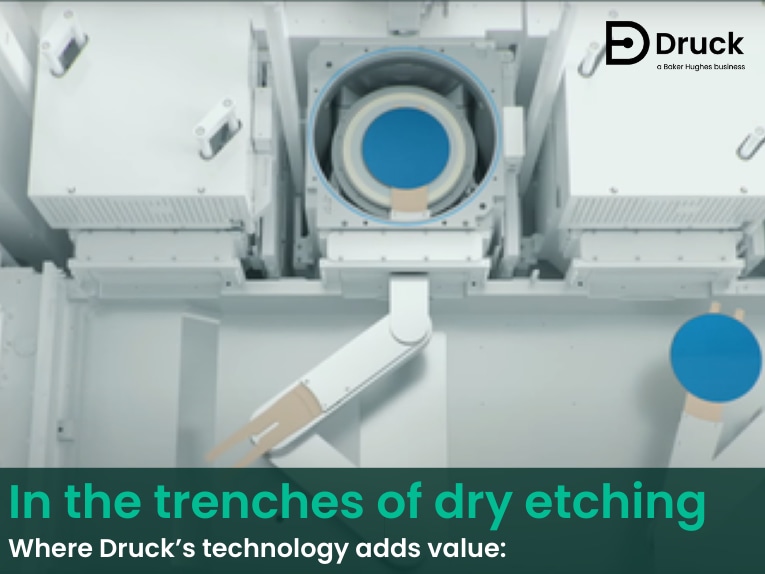
#Industry News
In the trenches of dry etching
Application Stories
Business challenge:
Druck’s customer, located in Japan, is the market leader in manufacturing Semiconductor Dry Etching machines, a major Semiconductor Process Equipment that is used worldwide to help Chip Makers deliver their products with the highest reliability
Customer’s challenge: End-to-end pressure management in critical Semiconductor process:
Dry etching is a key process to concrete the whole geometric integrated circuit structure of chips, that are used in different types of electronic devices ranging from smartphones to personal computers . It is a fully dry process exposing the material to ions, which utilizes the plasma activation for dry gases such as halogenated compounds, oxygen, ozone, hydrogen, hydrocarbons, and nitrogen oxides. The plasma ion selectively reacts the insulation materials like SiO2 and Low-K materials removing unwanted sections from the exposed surface of the wafer, in order to ensure the deep trench to be deposited by the wiring materials or insulation material at the next process, like chemical vapor deposition (CVD).
In recent years, the wafer diameter has gradually increased to improve throughput and reduce cost. In current manufacturing processes, the 300 mm diameters wafers have become the standard. However, with the current state-of-the-art fabrication of 300 mm wafers, there is a new challenge to the chip makers to evenly apply plasma gas to the entire surface of the wafers, compared with the initial 200 mm diameter wafers.
Therefore, dry etching equipment manufacturers are constantly pursuing improvements in the accuracy of the gas supply flow rate toward the vacuum chambers when filled with plasma reaction gas . Currently, mass flow controllers and pressure controllers have been adopted as control devices of the main gas supply system and have been also adapted for the helium coolant supply system.
Dry Etching Dry Etching:
Where Druck’s technology adds value:
The PC system requirement is being elevated for an even better stability and accuracy fully covering temperature control on the 300mm (12” inches) silicon wafers . Druck’s technology keeps evolving to implement new sensors like the DPS530D (shown in Fig. 4). DPS530D is the dedicated pressure sensor for the next generation of Pressure Controllers requiring proper specifications and functionalities, which is characterized as a full digital pressure sensor featuring:
High speed I2C interface (1ms)
High accuracy (0.1%FS Total Accuracy) with digital characterization
Full calibration at the ranges of both temperature and pressure output
These new functions enable PC (Pressure Controller)
Manufacturers to further improve the cost of ownership of their sensors due to eliminating unnecessary calibration onsite. Druck’s electric and pressure connectors are expertly designed for the semiconductor standard, which uniquely positions our products in this industry to deliver reliability and quality outcomes to our customers consistently.
Find out more about Druck’s solutions for the semiconductor industry here: Semiconductor-industry
Find out more information about Druck on LinkedIn here: https://www.linkedin.com/company/druckcompany
Druck’s solution:
For 20 years, Druck has been manufacturing and supplying silicon piezoresistive pressure sensors for pressure controllers (PC) equipped in dry etching systems. PDCR1000 is a small size analog pressure sensor (shown in fig.3) which has been used as one of core devices in PC, accurately measuring absolute pressure and temperature to control helium gas’ flow rate. It contributes to a significant stable analog output that fast respond to a couple of valves in PC from depressurized to pressurized condition
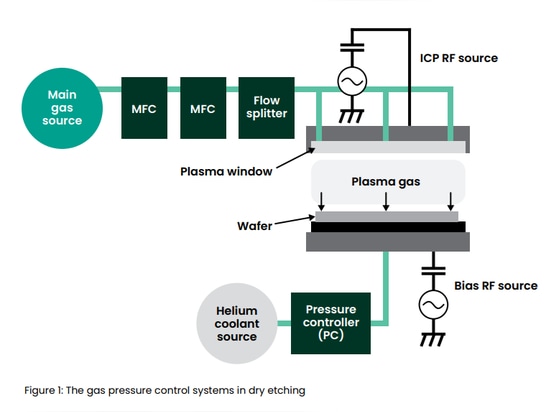
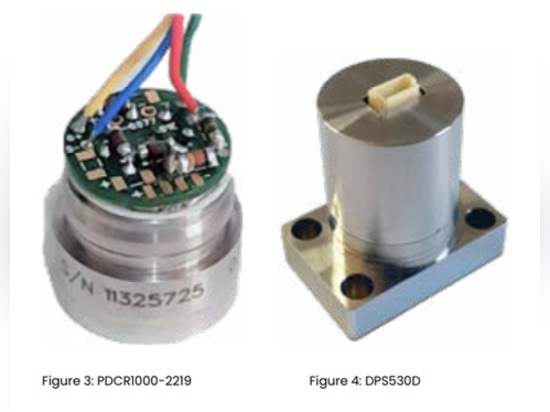