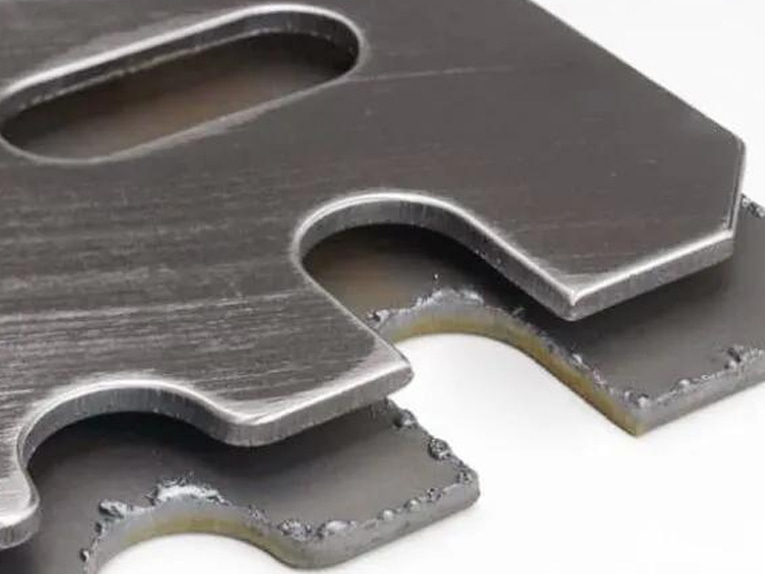
#Industry News
How To Solve the Problem of Edge Burrs in Metal Fiber Laser Cutting?
How To Solve the Problem of Edge Burrs in Metal Fiber Laser Cutting?
Fiber laser cutting technology is renowned for its high precision and efficiency in metal processing, but achieving flawless cutting edges is undoubtedly one of the core challenges in guaranteeing the superior quality and functional integrity of the final product. Edge burrs, a common problem encountered by many manufacturers, not only erode the aesthetics of a product, but can also affect its dimensional accuracy and even its core functionality, which is directly related to customer satisfaction and market competitiveness.
Therefore, if you want to know how to avoid the edge burr problem in the use of metal fiber laser cutting please read this article. This article provides you with the root causes of edge burr and a series of scientific and practical solutions.
Understanding Edge Burr in Fiber Laser Cutting
First of all, let’s first understand what is edge burr. Edge burrs are small, raised metal particles that form along the cut edge of a workpiece during a laser cutting operation. They vary in size and shape from tiny filaments to larger rough protrusions. While their formation is somewhat unavoidable, excessive burrs may indicate a problem with the cutting process, machine settings, or material properties. At this point, the user can then rely on considering whether the problem is with the machine itself or whether he or she is behaving inappropriately during operation, for example.
Root causes of edge burrs
Excluding the problem of the machine itself, when using the fiber laser cutting machine in the process of daily operation, what are the improper operations that result in burrs? The following is a list of 5 points:
Improper cutting speed and power settings: Incorrect laser power or cutting speed can lead to incomplete melting of the material, resulting in burrs.
Gas pressure and flow rate: Insufficient or excessive pressure and flow rate of the auxiliary gas (usually nitrogen or oxygen) can affect the quality of the cut and lead to burr formation.
Focus Adjustment: Incorrect focusing of the laser beam on the surface of the material can result in uneven heating and melting, which can lead to burrs.
Material Properties: The type, thickness, and surface condition of the metal can have a significant impact on the cutting process and burr formation.
Machine calibration and maintenance: Poorly calibrated machines or worn parts such as lenses and nozzles can reduce cut quality.
Solutions to reduce and eliminate edge burrs
Once the causes of edge burrs are understood, what can be done to avoid them? This article offers the following solutions:
1. Optimize cutting parameters
Adjust laser power and speed: Carefully calibrate the laser power and cutting speed to match the properties and thickness of the material. Thicker materials may require higher power and slower speeds, while thinner materials may require lower power and faster speeds.
Fine-tune gas settings: Experiment with different gas pressures and flow rates to find the best setting that promotes a clean cut. Oxygen can increase cutting speed, but may increase burrs on some materials; nitrogen is usually preferred for burr reduction.
2. Improving focus positioning
Ensure precise focus: Periodically check and adjust the focus of the laser beam to ensure that it is precisely aligned with the material surface. This ensures uniform heating and melting, which greatly reduces burr formation.
3. Addressing Material Factors
Material Preparation: Ensure that the workpiece is clean, flat, and free from impurities or surface defects that would affect the quality of the cut.
Material Selection: Consider the suitability of the material for laser cutting and select a grade of material that produces a cleaner cut with minimal burrs.
4. Enhanced Machine Calibration and Maintenance
Regular Calibration: Perform regular machine calibration to ensure that all components are functioning properly and aligned accurately.
Preventive maintenance: Implement a robust maintenance programme that includes cleaning lenses, replacing worn nozzles, and checking the overall condition of the machine’s mechanical and electrical systems.
5. Utilising advanced technology
CNC programming: Advanced CNC programming software is used to provide precise control of cutting parameters and path optimization, reducing the likelihood of burr formation.
Automated quality control: Integration of an automated quality control system to check cutting edges for burrs and other defects so that corrective action can be taken immediately.