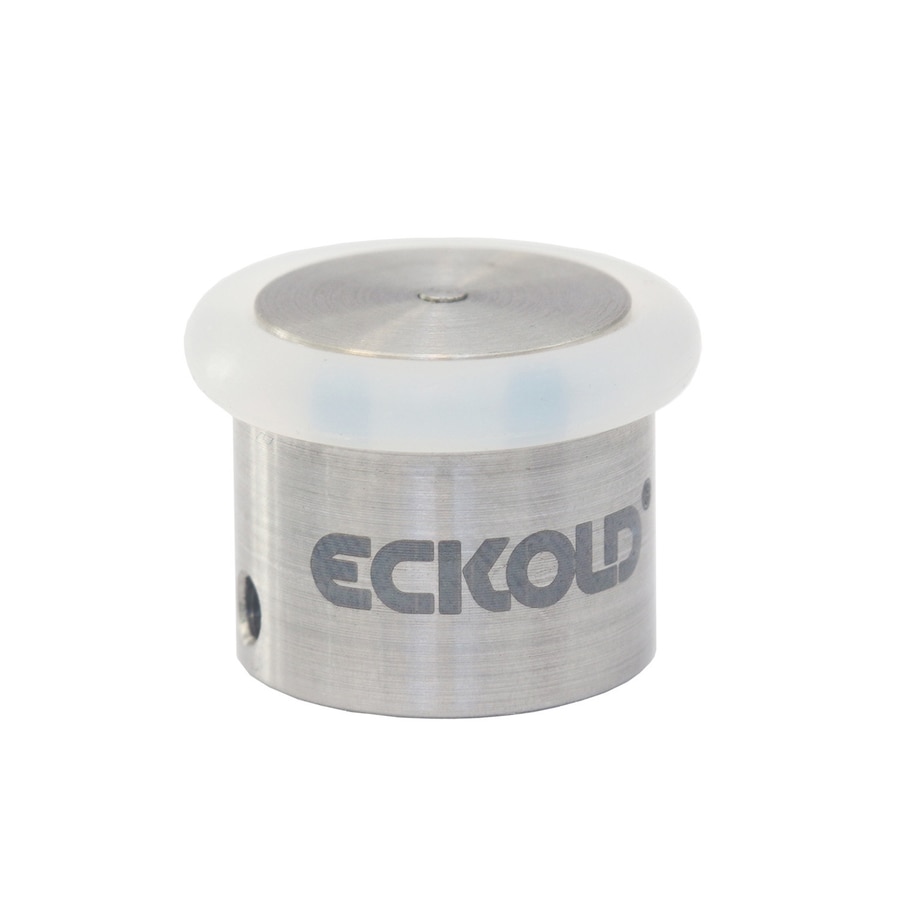
#Industry News
ECKOLD revolutionises teach-in of robot clinching frames
Time and cost savings of 50 % and more
Teaching robots and devices attached to them can be a time-consuming process, be it during commissioning or subsequent maintenance. However, correct teach-in is indispensable for automated and cost-efficient production.
This obviously also applies to ECKOLD clinching frames – tools that are widely used in automated car body production by virtually all renowned car manufacturers. Of particular importance here is the exact angle position of the die relative to the sheet metal. Required is an angle of 90° ± 1°, and deviations have significant negative effects on both the joints and the service life of the tools.
Up to now, such precise angle positions could generally only be achieved by taking extra measures, as the actual joining points are often concealed during the teach-in process. Programmers therefore resorted to feeler gauge tapes and torches.
Luckily, there is now a tool available to optimise the teach-in process: the new ECKOLD TeachCap. This aid caters for all clinching die types most commonly used in automated production. For robot teaching, the clinching die is simply replaced by a TeachCap of the same geometric size. The programmer can thus focus on moving the robot tool to the optimum positions without having to worry about secondary faults. As the die and the TeachCap are of the same height, there is also no problem as regards distances, and a rubber ring keeps the TeachCap away from interfering edges and radiuses. The main innovative feature of the TeachCap is of course that is lit the moment the optimised angle position is reached.
The ECKOLD TeachCap significantly shortens the teach-in time. In addition, it prolongs the service life of clinching tools thanks to optimised joining angle programming.
Current users report a reduction in the setup and commissioning time of 50% and more. Teaching with the ECKOLD TeachCap often produces already good results after only one programming run along all clinching points, reducing the total number of runs required to complete the teach-in process.
The TeachCap pilot project was supervised by Andreas Seiffert, head of production at ECKOLD, and Florian Auernhammer from VW, who brought the innovative method to market. Final testing was completed in cooperation with Thomas Redler, project manager at AUDI.
Advantages and characteristics at a glance
• Shorter setup and programming times
• Faster teaching of robots
• Improved quality of initial teach-in processes
• Rubber ring serves as distance guide to interfering edges and radiuses
• Prolonged tool service life
• Easy handling: simply replace the die with the TeachCap
• Efficient optimisation of production process
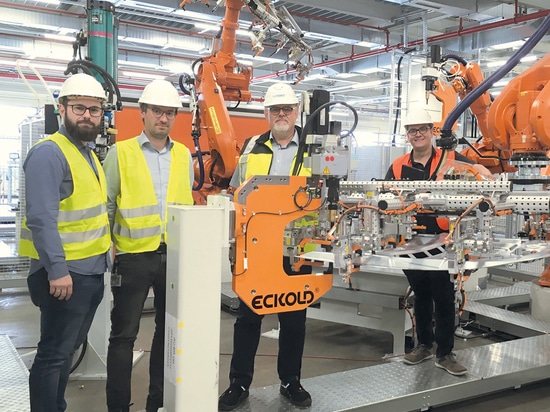
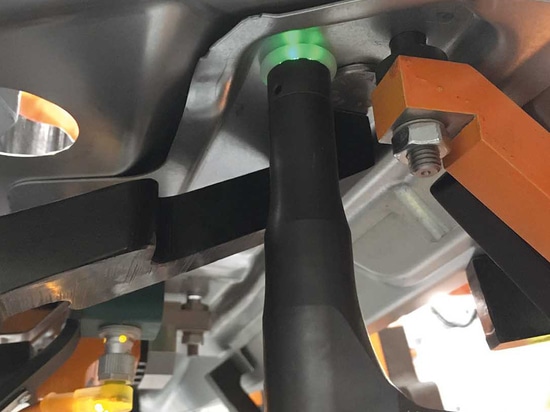
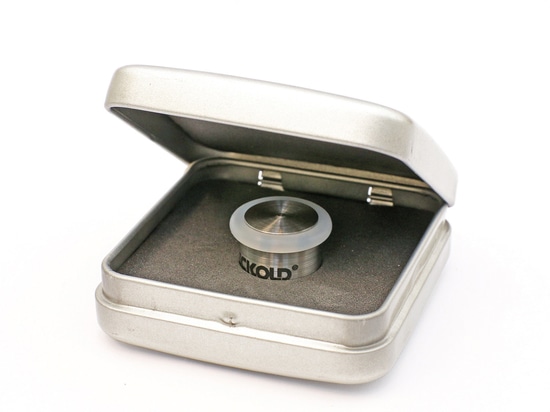
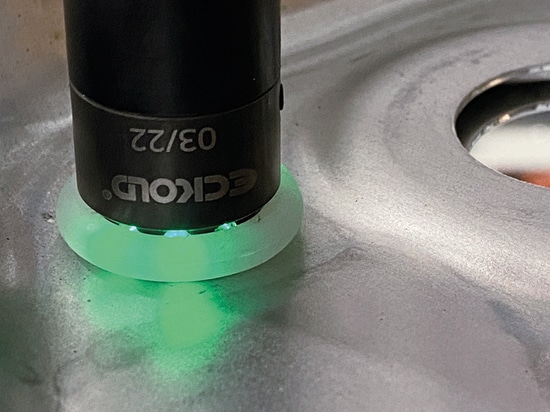