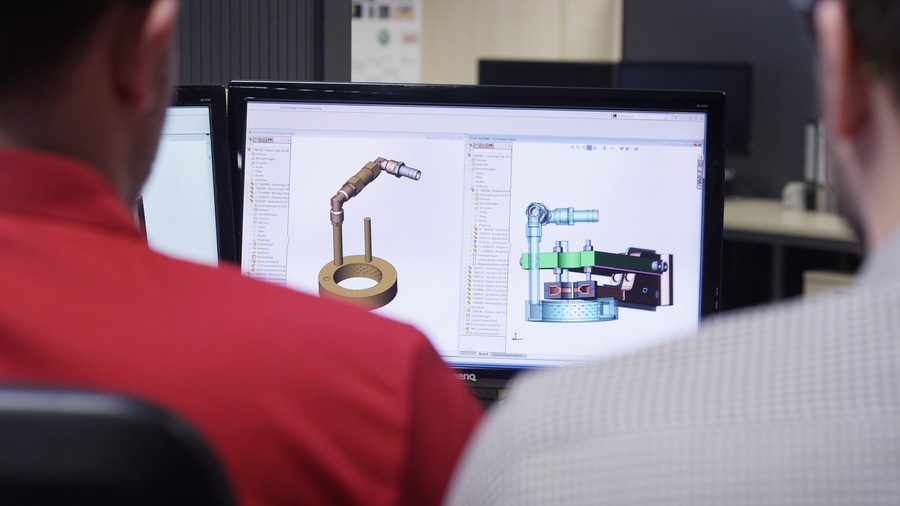
#Product Trends
Inductors from eldec
Inductors from eldec: custom manufacturing for perfect induction heating
Induction heating is a growth sector, and for good reasons. The technique is energy efficient, reliable, reproducible, very fast and its range of possible applications is almost unlimited. For example, induction can be used on parts to heat, join, braze, harden, or even melt them. A critical component in these processes is the inductor. Its design is crucial in determining how precisely a part is heated. Complex manufacturing processes are therefore used to produce this central tool with precision to a tenth of a millimeter—a task perfectly suited to the experts at eldec, with facilities in Auburn Hills, MI USA and in Dornstetten, Germany. The technicians at these EMAG subsidiary have a thorough understanding of the different applications of induction heating. For more than 30 years, they have been developing inductors to match, which are adapted to the geometry of the workpiece with painstaking dimensional accuracy.
The crucial quality in induction heating is best summarized by the word “precision.” The technology is used anywhere where a lot of energy or heat needs to be applied to a workpiece in a very short time. Temperature accuracy plays an important role here and is often process critical – and precise heating is only possible with the right mix of inductor geometry, frequency, power, and magnetic field characteristics. Furthermore, the application of energy through induction ensures fast production processes, minimal workpiece distortion, and economical energy consumption.
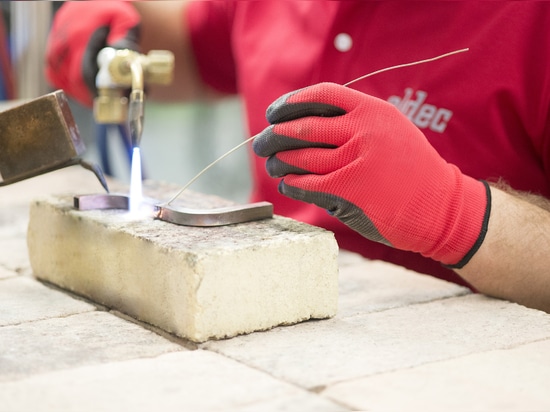
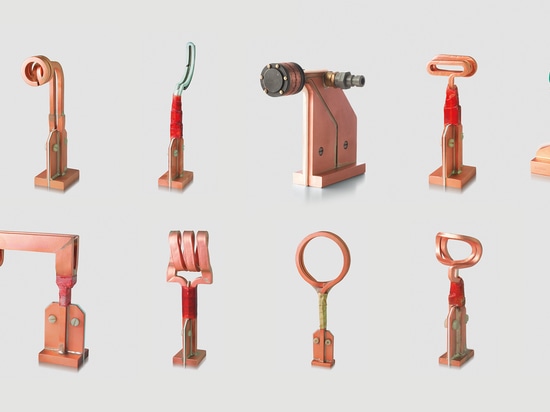
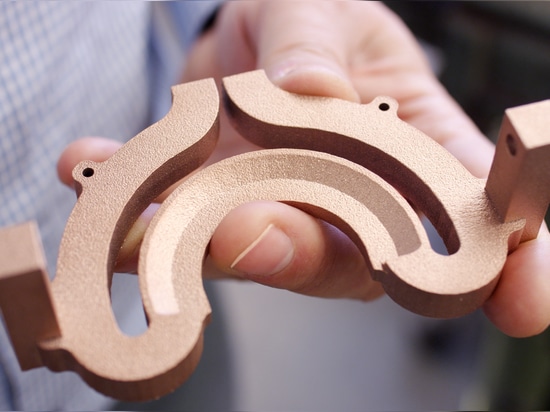