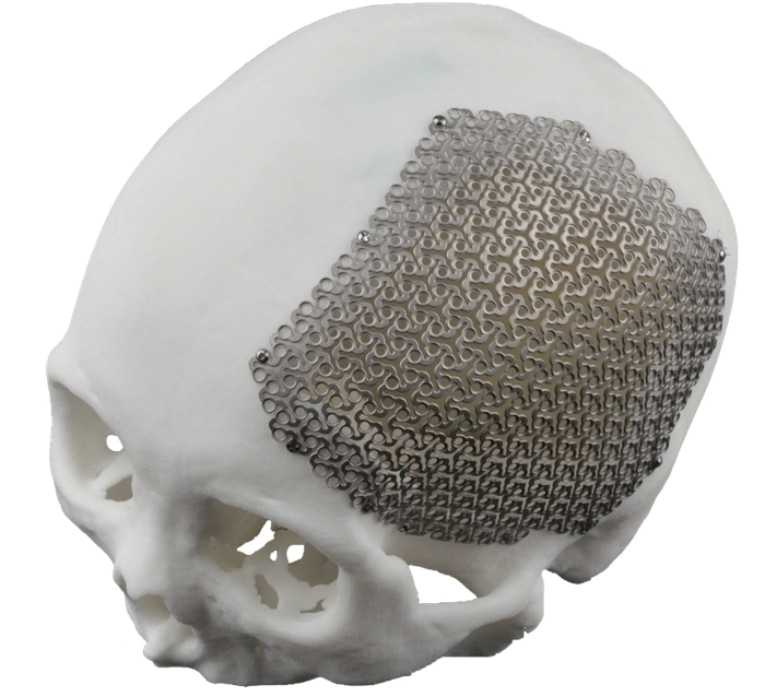
#Product Trends
Manufacturing and Materials of 3D Printed Cranial Plates
Eplus3D provides the AM solution for both Titanium and PEEK materials
Patient-specific cranial plates are mainly used to replace absent portions of cranium for reconstructive surgery, to shield the unprotected brain from external impact, pressure, and infections. Implants in particular must be made of materials that are likely to be accepted by recipients’ bodies. Corrosion-resistance is equally as important, as our bodies’ fluids are surprisingly corrosive over time. And because implants need to stand up to heavy long-term use, these materials must be strong, durable and lightweight.
Fortunately, modern 3D printers are compatible with a number of plastics and metals that meet these qualifications. Below, we’ve outlined a few of the most commonly used 3D printed materials for the cranial plates.
3D Printed Titanium Cranial Plates by MPBF Technology
Titanium is the king of biocompatible metals and is the most popular material for medical implants. It is extremely strong, lightweight, corrosion-resistant and non-reactive. It can be 3D printed using metal powder bed fusion technology. The titanium mesh and titanium plate implants can be fixed by the titanium screws, which has become the first choice for reconstructive surgery.
Compared with conventional CNC machining method, the benefits of 3d printed titanium cranial plates are mainly as follows: shorten the lead time, the implant can be manufactured within 1-2 days. The porous structure is similar to human bones, which can effectively overcome the common problems of stress shielding and low biological activity of implants, and at the same time minimize the heat dissipation in the cranial cavity and maintaining a normal thermal conductivity.
3D Printed PEEK Cranial Plates by PPBF Technology
Polyether Ether Ketone (PEEK) is a kind of polymer material with good biocompatibility, wear resistance, fatigue resistance and stable chemical properties, which can be sterilized by high -temperature steam or gamma irradiation. It has been mainly used in the reconstructive surgeries as a reliable alternative to other alloplastic materials for the fabrication of patient-specific implants. 3D printing of PEEK using PPBF allows construction of almost any complex design geometry, which cannot be manufactured using other technologies.
PEEK has a high melting point (glass transition temperature 143 ° C, melting point up to 343 ° C), which makes it difficult to process. At present, the processing methods for PEEK cranial plates mainly include CNC machining and rapid prototyping.
CNC machining usually starts with a blank block of PEEK material that is slowly shaped into the final part. The computer controls the tools needed for fabrication of the part by controlling the lathes, mills routers, and grinders used in the process. In addtition, additional post-processing work is required after fabrication. This technique is time consuming, resulting in substantial waste generation and is far more expensive than AM.
Compared with CNC machining, 3D printing improves the flexibility of PEEK manufacturing, overcomes the difficulties such as material waste and difficult machining, and the lead time is significantly decreased.
Eplus3D provides the AM solution for both Titanium and PEEK materials, welcome to contact us for more information.
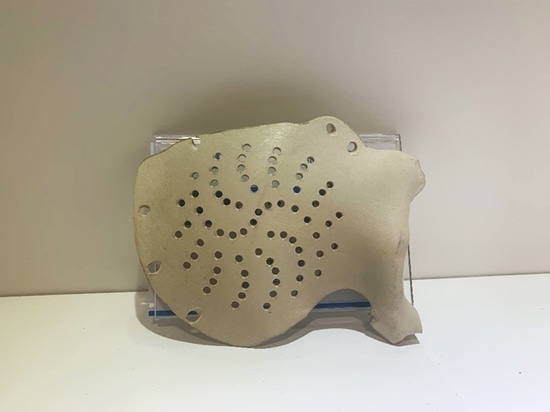