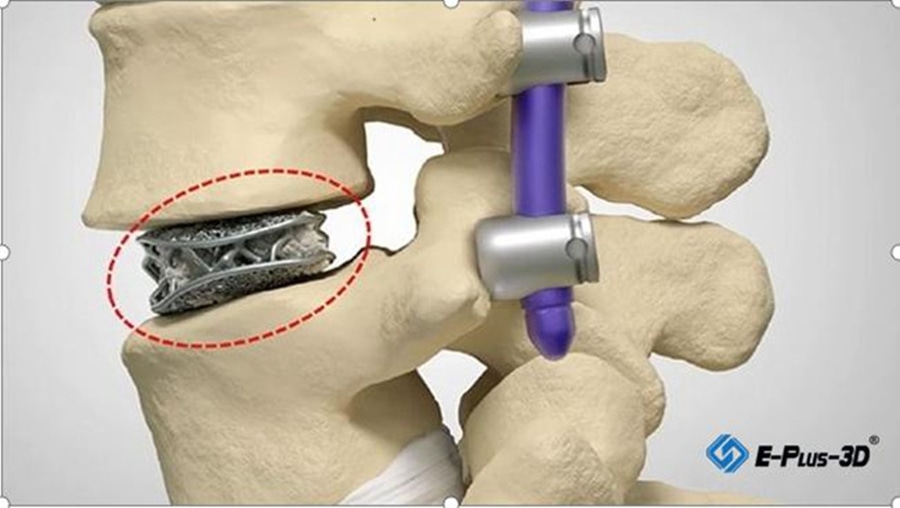
#Industry News
Spinal Implant Manufacturing Using EP-M250 Metal 3D Printer
Eplus3D Metal 3D Printers Provide Solutions for Spinal Implant
Customization of processing by additive manufacturing
As additive manufacturing technology continues to advance, so does its application and accessibility. Rapid prototyping and tooling are at the forefront of 3D printing, but the goal has always been to be able to print directly for production or directly for manufacturing. The medical world is no exception. Although the first 3D printing applications in the medical field were prototyping and visualization guides, this technology has finally reached the stage of custom implants using state-of-the-art 3D printers.
Eplus3D remains true to its vision of providing a personalized 3D solution for everyone. With its latest line of metal 3D printers, Eplus3D is drawing the attention of medical partners who are incredibly leveraging this technology. One of the pioneering partners in the creation and use of medical implants is MANTIZ.
MANTIZ is a medical device company that uses superior engineering and technology to achieve an active and painless life for all patients with spinal disorders. MANTIZ has obtained KFDA certification (medical device approval) and is listed on the HIRA (Health Insurance Review and Evaluation) list in South Korea. MANTIZ began developing 3D printed cage implants in 2018 with government approval and funding. In May 2019, they launched a 3D printed PANTHER cage system for PLIF (Poster Lumbar Interbody fusion) / TLIF / OLIF / ALIF surgery. This process uses 3D printed cage implants without outsourcing the manufacturing process to a third party. This saves customers time and money and reduces the chance of production errors. MANTIZ uses Eplus3D's EP-M250 metallic 3D printer to manufacture cages printed in titanium 3D for use in implant surgery. The entire process of shaping the implant is done internally by MANTIZ. The cage is designed according to specifications. Size, material, shape and porosity are essential to the effectiveness of the implant. The complete design of the cage is loaded into the printer software, where it is ready for printing. The large print bed of EP-M250 can be used to print more than 50 individual implants in one structure. Upon transplantation, the bone and surrounding tissue begin to fuse with the implant, creating a strong structure in the patient's spine. Hongwon Yoon (CTO of MANTIZ) the inventor of MANTIZ's PANTHER 3D print cage system, said: "We have completed the development of a more improved titanium 3D printed cage implant using the EP-M250 3D metal printer. Mechanical test results prove the safety and functionality of the implant. 3D printing The average closed pore ratio of the solid titanium component is 3%, which promotes the binding of the protein for bone fusion to the mesenchymal stem cells.”
Please check the images below to see the whole process from design to printing, printing to embedding. The world of 3D printing is constantly evolving, and as technology advances, so does direct application. Customization at your fingertips, more affordable than ever. The automotive, aerospace, and medical industries are now 3D printing directly into production, which is only part of the technology's capabilities. Contact Eplus3D directly (info@eplus3d.com) for more information on how to incorporate additive manufacturing into your daily workflow.
3D design and printing process:
Integrated design with professional 3D software
Prepping the parts in 3D printing software
Using Eplus3D’s EP-M250 for 3D printing
Metal 3D printing process in the chamber
3D Printed cages
Post processing including heat treatment, removal of supports, surface treatment, disinfection, etc.
Only after a series of mechanical tests, the 3D Printed cage can be applied in surgery.
Through the process of “design-3D printing-post-processing-testing”, the PANTHER can be ready for operating surgery. Currently, the PANTHER has already been applied in treatment for patients.
Advantage of Titanium 3D Printed Cage:
PANTHER has been formulated to optimize bone growth during spinal procedures, with an average pore size range of 630-730μm in the contact surface of the spinal end plates and an average porosity of the mesh section in the range of 70% -80%.
Potential is average
About Eplus3D
Eplus3D was founded in 2014, the core technical team has more than 25 years of AM technology accumulation, has been engaged in research and development of industrial-grade Additive Manufacturing systems and application technologies, with MPBF™ (Metal Powder Bed Fusion) , PPBF™ (Polymer Powder Bed Fusion) and Stereo lithography 3D printing technology, provides professional application solutions for the fields of Aerospace, Automotive, Tooling, Health, Dental, Consumer Goods, Precision Manufacturing, etc.
Eplus3D has two facilities in Beijing and Hangzhou, with annual scientific research investment of more than 20% of the revenue with comprehensive invention patents, utility model patents, software copyrights, and appearance patents. It has made great achievements in the design, equipment, process, software, materials and post-processing for the additive manufacturing, with equipment has been exported to more than 40 countries and regions such as Europe, America, Japan, South Korea and Southeast Asia, etc.
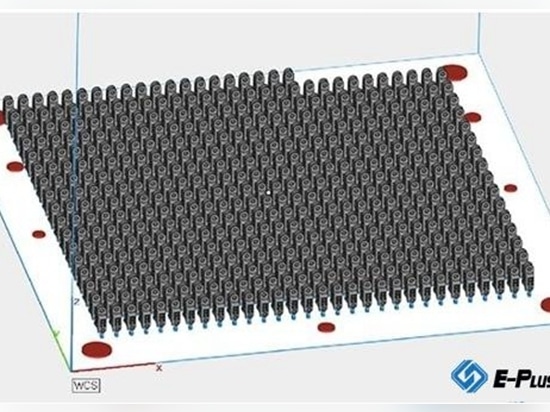
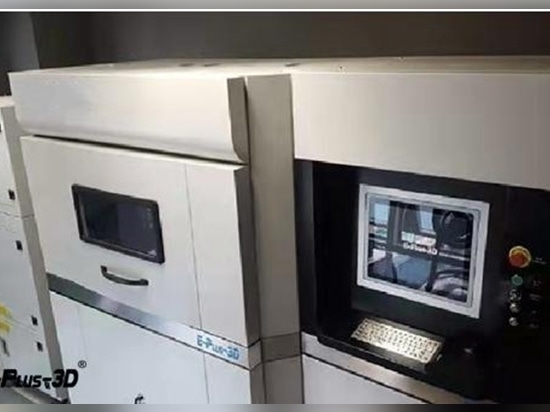
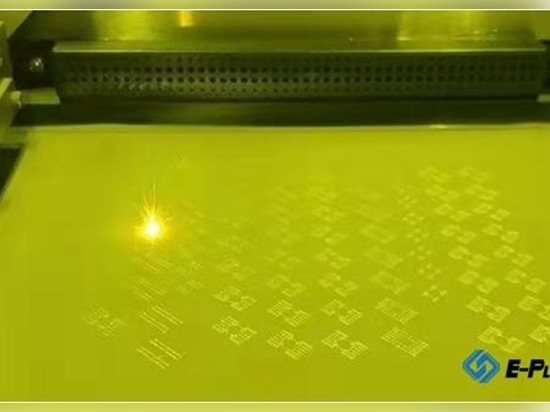
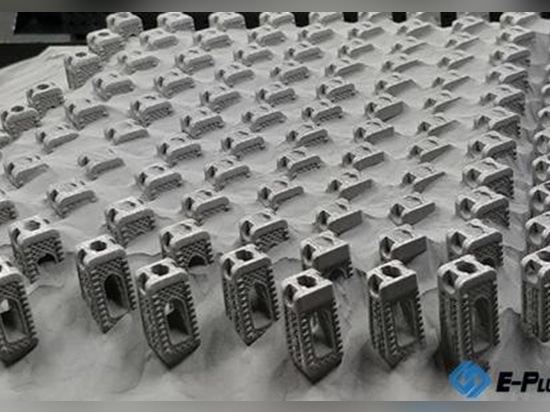
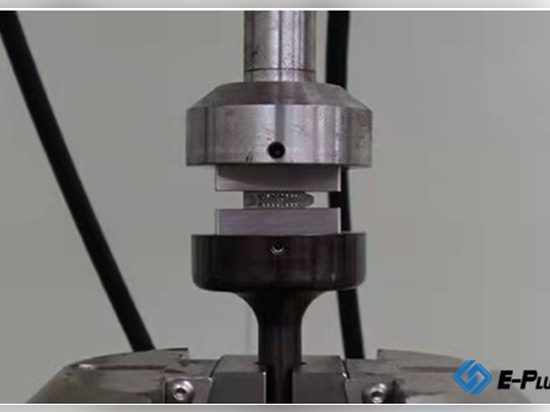
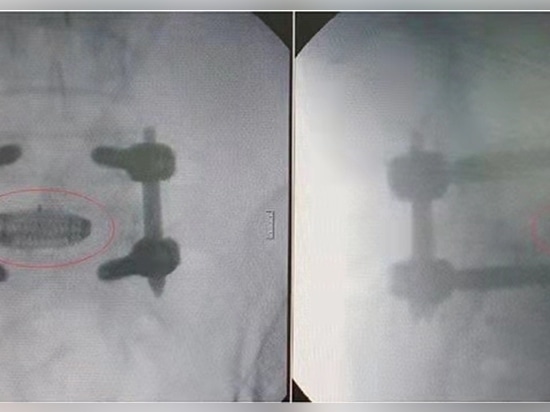
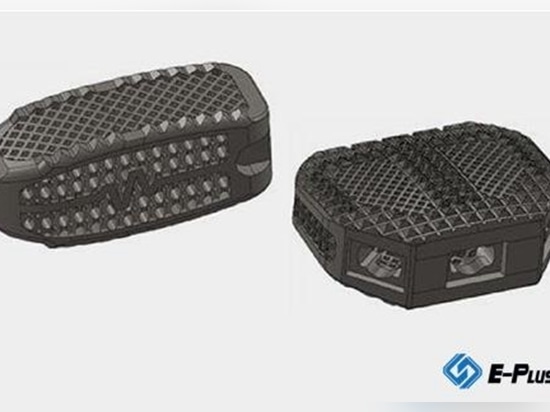