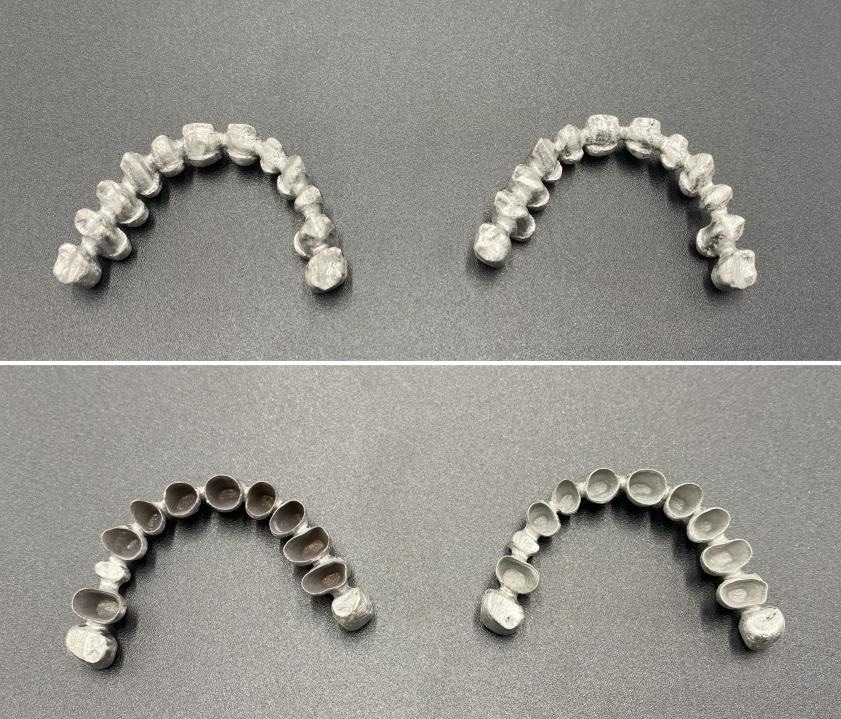
#Product Trends
Advantages of Metal 3D Printed Porous Titanium Dental Implants
Bones have a porous and anisotropic structure, which means that the density of bones varies with the length, width and height.
Bones have a porous and anisotropic structure, which means that the density of bones varies with the length, width and height. The porosity of the bone helps to grow inward, and the size of the pore helps the cell to proliferate. In addition, different pore shapes may change the permeability, which can lead to different inward bone growth. The inward growth of bone produces efficient mechanical properties. The compressive strength can be changed by simply porosity controlled, pore shape and size of the scaffold.
Dental implants manufactured in the traditional way are made of titanium rods with surface modifications, in order to achieve the desired surface properties to facilitate osseointegration.
Metal 3D printing builds complex geometric porous structures layer by layer, and eliminates complex post-processing steps, greatly shortening the production process.
One of the benefits of metal 3D printed titanium dental implants is the biomechanics advantage over traditional implant techniques. Several studies have mentioned that enhanced osseointegration, cell proliferation and attachment are beneficial outcomes. Porous structures with surface roughness and biomimetic porosity show enhanced cellular responses and mineralization in vitro.
Another often mentioned advantage of metal 3D printed dental implants is that the method has sufficient accuracy to be used to fabricate implants of any desired shape and size. Metal 3D printed dental titanium implants are fabricated according to a digitally preset structure. One of the advantages of this process is that multiple parameters can be combined to achieve the desired mechanical and biological properties. These parameters are controlled by pore size, shape, distribution and percentage porosity. The printed titanium is more favorable to the plastic deformation of the milled samples under static tensile and bending tests.
Eplus3D has cooperated with multiple dental labs and companies to streamline dental workflow and is committed to helping more dental laboratories and companies realize 3D digital transformation. Welcome to contact Eplus3D.