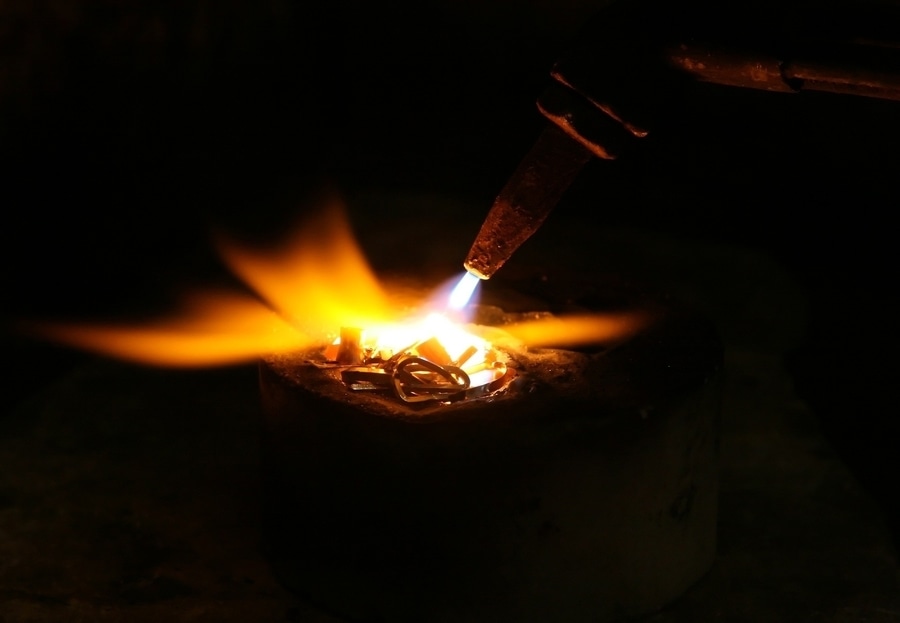
#Product Trends
3D Printing Metal Materials: the Importance of Weldability for Post-processing
Weldability refers to the ability of a material to be welded into components specified in the design requirements and meet the predetermined service requirements under the specified welding conditions.
Metals with good weldability, welded joints are not prone to cracks, pores and slag inclusion defects, and have high mechanical properties.
Weldability refers to the degree of difficulty of obtaining high-quality welded joints under the conditions of certain welding methods, welding materials, process parameters and structural types.
There are many factors affecting the weldability of metal materials, mainly including four aspects: metal materials, structural design, process measures, and service environment.
Material
The material factor refers to the wood itself and welding materials, including the chemical composition of the material, smelting and rolling state, heat treatment, organizational state and mechanical properties, etc.
Processing
The process factors include the welding method used in construction, the welding process specification (such as welding heat input, preheating, welding sequence, etc.), post-weld heat treatment, etc.
Environment
Environmental factors refer to the working temperature, load conditions (such as load type, mode of action, speed, etc.) and working medium of the welded structure.
Structure
Structural factors include the form, stiffness, and stress state of welded structures and welded joints, which will affect the mechanical properties of the joints and produce welding defects.
Welding is also another post-processing process for metal 3D printing, which considered as a manufacturing process and technology for joining metals or other thermoplastic materials such as plastics by heating, high temperature or high pressure.
In metal 3D printing, sometimes high and thin parts are encountered. In order to achieve printing and save costs, it needs to be cut into multiple sections for printing, and finally spliced all parts together. For example, for the printing of trophies, vertical printing is the most ideal printing method, but the model is high, and vertical printing will be very time-consuming, so it is more appropriate to decide to cut and print.
As for the aesthetics of the welds, that's a real problem, but it can be solved nicely by polishing. The polished metal print has no traces of welding, just like it was printed in one piece!
Another solution for high parts is to choose a large-format and high volume metal printer with a high molding chamber, which can directly print samples at one time without cutting and printing, saving file design time and post-processing time.
Eplus3D Metal Additive Manufacturing System EP-M450H
With a building chamber size of 456x456x1080 mm³, Eplus3D Introduces EP-M450H to the successful line of MPBF 3D printers. The new EP-M450H is a marvelous metal printer that makes the production of reliable and high quality large metallic parts viable on industrial scale without requiring any tools.