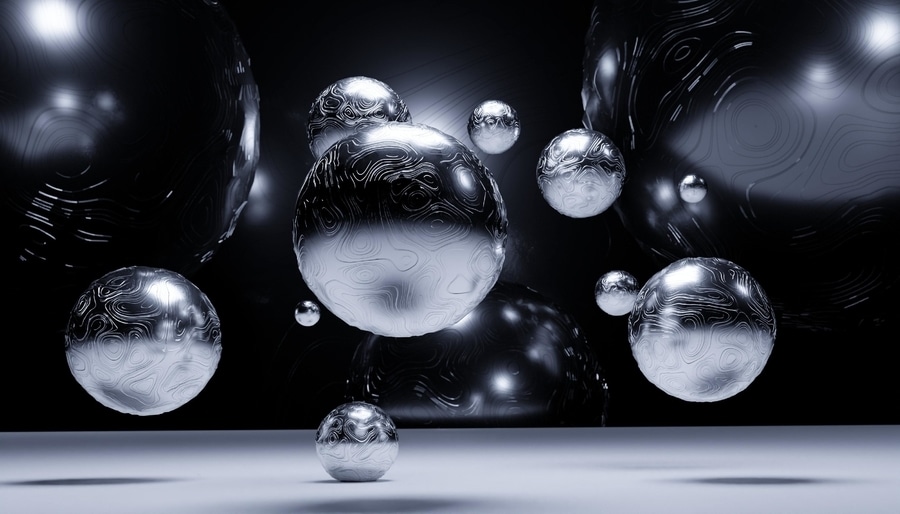
#Industry News
Development Status of Metal 3D Printing with Aluminum Alloy Powder Materials
The Development of metal material.
Aluminum alloy materials are characterized by lightweight and ease of processing, and have broad prospects in the field of lightweight manufacturing. However, they also have characteristics such as high thermal conductivity, easy oxidation, and high laser reflectivity, which cannot be applied to all heat sources in metal 3D printing.
For laser 3D printing, the Al-Si series alloy powder has better adaptability than the Al-Cu series and the Al-Zn-Mg-Cu series because of its good flowability and excellent casting and welding properties. It can withstand the large internal stress generated during the rapid heating and cooling process of metal 3D printing using laser as a heat source. If the Al-Cu series and the Al-Zn-Mg-Cu series are not modified by adding other elements, they will suffer from thermal cracking and cannot be used in metal 3D printing using laser as a heat source.
The material used in arc 3D printing technology is wire, and the Al-Cu series and the Al-Zn-Mg-Cu series are less susceptible to internal stress when used in telephone 3D printing compared to laser 3D printing. They also have better formability. However, Al-Si series alloys are difficult to prepare as wires due to their hardness, making it difficult to process them through arc 3D printing.
Currently, the most widely used 3D printing technology uses laser as a heat source, so aluminum-based materials used in metal 3D printing are mainly Al-Si series.
The development direction of aluminum alloy materials in the field of metal 3D printing
Based on the development direction of metal 3D printing technology, the main development direction of aluminum alloys used for 3D printing is high-strength aluminum alloys that can adapt to laser additive manufacturing technology. Currently, many aluminum alloy materials specifically for metal 3D printing have appeared abroad. These materials are generally prepared by adding elements such as Sc, Zr, and Ti, which allow aluminum alloy materials to form Sc, Zr, and Ti particles during the rapid heating and cooling process, avoiding thermal cracking of the structure.
In addition, improving the utilization rate of aluminum alloy wire materials applicable to arc 3D printing and reducing their preparation costs is also a research direction, which is gradually being applied.
At present, 3D printed aluminum alloy parts have been widely used in the aerospace field, mainly for lightweight and complex parts, such as pressure vessels, manifolds, brackets, heat exchangers, etc.
It is believed that with the continuous development of new aluminum alloy materials and the continuous improvement of metal 3D printing technology, aluminum alloys will have great potential in the field of lightweight manufacturing.