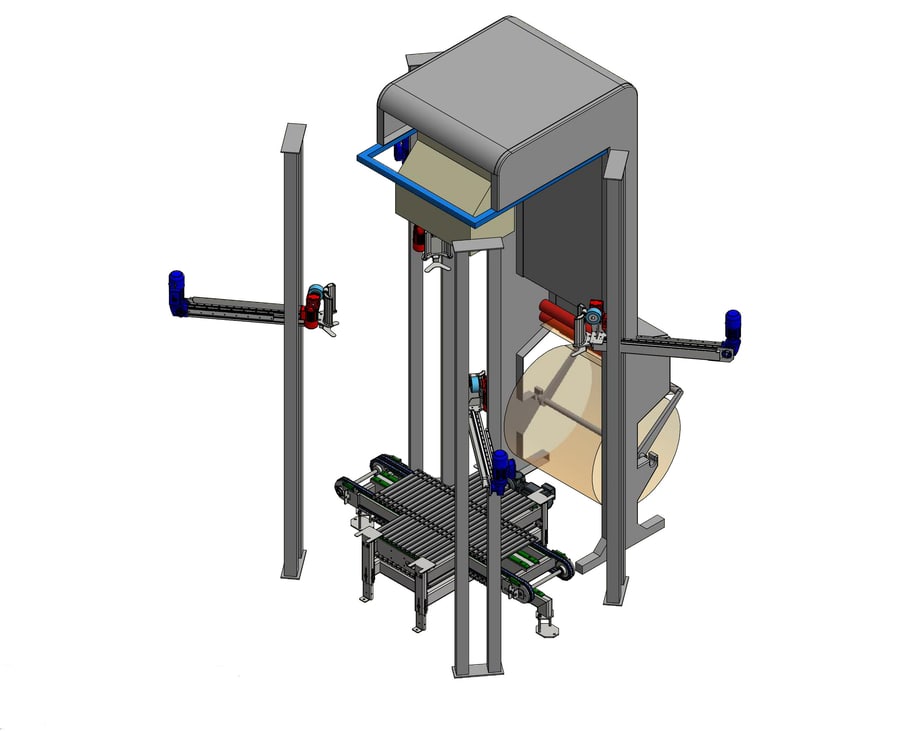
#Product Trends
Dino Stretch Hood FLEX
new stanard in stretch hood technology
The most compact Stretch Hooder available. The patented FLEX concept let’s stretching arms, who stretch and place the stretch hood over your product, work independently in freestanding guide poles. The lack of framework in which traditional stretching arms are linked, brings flexibility in implementing your Dino Stretch Hood FLEX.
Project specifications determine the position of the guide poles. FLEX adapts to your specifications.
It opens the possibility to process pallets from two directions making a corner lay-out possible.
FLEX is cost conscious and completely standardized. The new standard in Stretch Hood technique!
No pneumatics or hydraulics are used in the machine. By excluding these energy-consuming techniques, energy consumption is kept to an absolute minimum. You’ll save significantly on operating costs, on average, € 3500 / year. It further reduces your carbon footprint as a company.
Innovative machine movements ensure that each pallet is packed under the most ideal circumstances. This not only guarantees the reliability of the DINO, but allows a high degree of flexibility and reduces maintenance costs.
Changing a reel of film, inspection work or exchange of wear parts are all feasible at ground level working height. Moving machine parts for special maintenance or film changeover positions are superfluous avoiding unnecessary delays.
More information can be found online: www.dinostretchhood.com