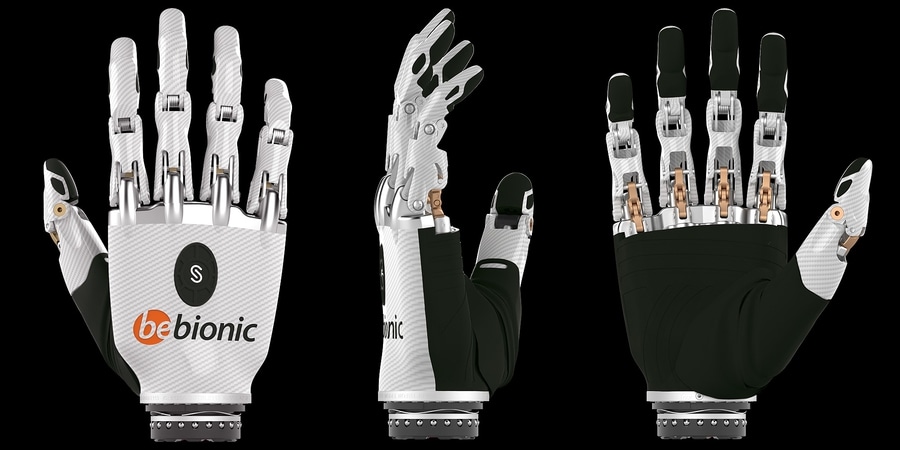
#Product Trends
Innovation goes hand in hand
Tie shoelaces, fold bed linen, tear open a bag of crisps - the list of things that are difficult to do with one hand goes on and on.
People with a Congenital amputation or who have lost a hand through an accident or illness are confronted with such obstacles every day. To make daily life easier, the British company Steeper developed the bebionic myoelectric hand prosthesis. It is controlled by myoelectric signals generated from muscle contractions in the arm and can perform multiple different grip patterns selected by the user. The most recent innovation brings to the market the small bebionic hand suitable women, men of a smaller stature or teenagers. FAULHABER high power density motors ensure that the prosthesis can grip smoothly, quickly and firmly and retain the grip force without relaxing.
Functional prostheses are known to most of us only in science fiction films which give the artificial extremities superhuman strength. By contrast, bionic hand prostheses do not make the wearer a superhero in real life. But they can make many things possible for them which are normal for most people. Nicky Ashwell, the first user of the small bebionic hand is delighted to finally be able to ride a bike: “I never tried it before because I was afraid of falling off the bike on uneven surfaces or putting my back under the wrong kind of strain.”
Intuitive movement
The bebionic myoelectric prosthesis weighs between 400 and 600 grams and is about as heavy as a natural hand. It is controlled using the tiny electric signals in the body. These are generated when a muscle contracts and can be detected with electrodes on the skin
- the same way as an ECG in heart diagnostics. Two electrodes are integrated into the prosthesis socket, which detect the myo electric signal and are forward them to the
control electronics. These signals are amplified and used to activate the five small electric motors (one for each digit), which move the fingers and thumb causing the hand to open and close . As a result, the strength of the muscle contraction controls the speed and the gripping force: a weak signal generates a slow movement, a strong signal generates a quick movement. The muscles which are used to open and close the hand prosthesis are actually responsible for the movement of the wrist in a natural hand. Its wearer must learn that it now has a different function. “The human brain is unbelievably adaptable. After a short amount of time, people perform the movement intuitively like how car drivers step on the brake when they want to stop,” says Ted Varley, Technical Director at Steeper.
Additional motors for more control
The first myoelectric hand came onto the market at the start of the 1980s. They were driven by a single motor and only had a simple gripping mechanism: thumb, index and middle fingers could be closed for a pincer grip. Ring and small fingers were only available for cosmetic reasons and had no gripping force. This concept was fundamentally changed for the bebionic around ten years ago. “We determined that people accept lower gripping force per finger if they get more flexibility,” explains Ted
Varley. To control the individual fingers, each finger on the bebionic hand is equipped with its own electric motor. The four motors for the fingers are located in the palm of the hand, the fifth located in the thumb itself. Encoders are integrated into the motors which precisely detect the position of the finger at any time.
Thanks to individual control, the fingers can be arranged into a total of 14 different grip patterns. The key grip, which moves the thumb up and down with the fingers flexed enables you to hold flat items such as plates, keys or bank cards. The hook grip enables heavy loads of up to 25 kilograms to be carried, and in the case of the outstretched index finger the use of keyboards and remote controls is permitted. With the power grip, the thumb is in the opposite position and all fingers close until they
encounter resistance. This is used to clasp irregularly shaped objects such as wine glasses. “This position looks much more natural than a pincer grip and provides a much more stable grip when all fingers are used,” stresses Varley.
To change between the individual grip patterns, the bebionic wearer also uses the arm muscles. If another “open” signal is given when the hand is already open, the prosthesis changes into the next mode. An additional signal is provided by the thumb which is either moved to the side of the fingers or can be
moved into the opposite position. Different grip patterns are available depending on which thumb position is chosen. Thereby, the hand owner can decide for themselves which of the 14 possible grip types they want to use and in which order they are requested and using software they can program the prosthesis individually.
Increased self-esteem
The bionic hand makes many everyday activities easier. “Actually, it is often the small things which become easier with the prosthesis. To sum up, it leads to a clearly improved quality of life,” explains Ted Varley. Furthermore, the artificial hand also has a big psychological effect: “Many users report that their feeling of self-esteem is increased with the use of a bebionic hand with the high-tech prosthesis attracting interest and fascination.”
In this context, the attractive design of the prosthesis also plays an important role with the use of aluminium and stainless steel resulting in an appealing design. Furthermore, the exterior design has also been adapted as closely as possible to the natural appearance. “Our approach was rather unusual in prosthetics with the development of the third generation of bebionic: We first developed the housing and then searched for solutions such as how the individual components could be
integrated,” emphasises Varley. “Five years ago, this would not have been possible for the small hand - the technology wasn’t advanced enough.” Also, the DC- micromotors of series 1024 SR that were predestined for this application were still in the development phase when Steeper turned to FAULHABER with this project in 2013. The project teams on both sides then expedited the development of the motor series and hand prosthesis at the same time. Regular meetings of the STEEPER
and FAULHABER development teams took place in the UK and Switzerland together with and facilitated by Electro Mechanical Systems (EMS), the exclusive distribution partner of FAULHABER in Great Britain. This intensive cooperation resulted in a motor with an exceptional power-volume ratio for the fingers and a bespoke actuator for the thumb bringing this extensive development cooperation to a successful conclusion.
Top marks for performance
The new DC-micromotor of series 1024 SR is genuinely best in class and the most powerful for its size in the market. With a diameter of 10 mm and a length of 24 mm, it delivers a stall torque rating of 4.6 mNm. Furthermore, it offers consistently high torque across the entire speed range resulting from the flat speed/torque curve. The strong performance, among others, is made possible by the development of a new coil design which contains 60 percent more copper than its predecessor and has
been combined with a powerful rare-earth magnet. In order to make the movement as quiet as possible, the artificial hand uses planetary gearheads based on series 10/1 in customised versions which do not contain any plastic. “A significant challenge was the development of the linear drive system which had to be integrated into the thumb”, says Tiziano Bordonzotti, Sales Manager at FAULHABER MINIMOTOR. Thanks to high-precision 4 points contact bearing from FAULHABER’s subsidiary, Micro Precision Systems (MPS), specialists in very high precision bearings and micro systems, it was possible to make the drive system significantly shorter compared to the
competition. The unique characteristics of the 4 point contact bearing mean that even with a smaller dimension than alternative bearing systems it still withstands the required high axial load in this application. The complete thumb actuator remains within a total length of less than 49mm and can withstand an axial force of up to 300 N.
Ted Varley is excited by the result of the collaboration: “The small bebionic hand is the most lifelike myoelectric hand prosthesis on the market and it would not have been possible to realise this project without the close cooperation of the project team of FAULHABER.”
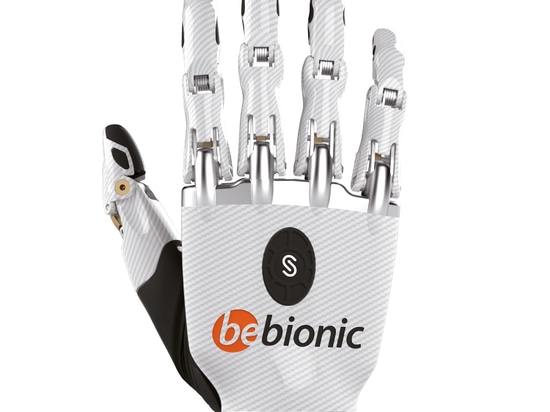



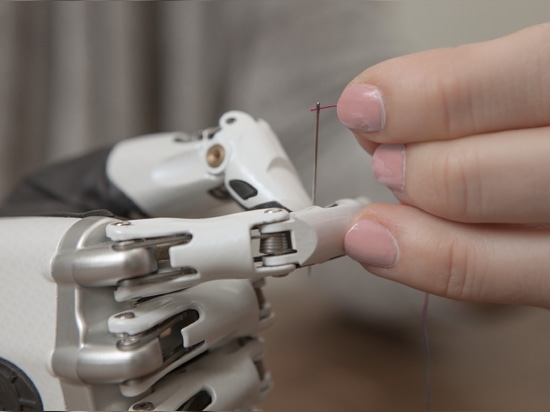