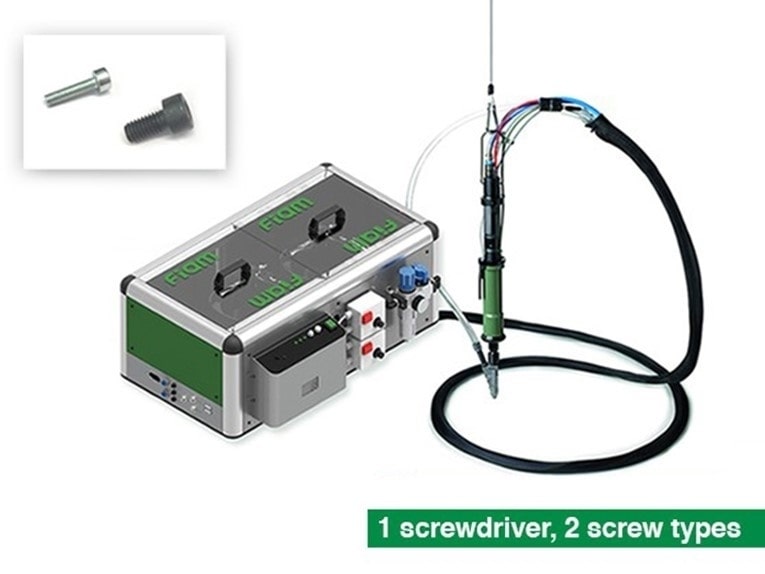
#Industry News
To tighten two different types of screws
With a single automatic screwdriver
More and more in production lines the components to be assembled contemplate numerous variants which imply, in turn, the use of different types of screws; the manual workstations managed by operators therefore require extreme production flexibility as well as fundamental precautions to reduce fatigue not only physical but also mental due to the continuous monitoring of the operations to be performed.
To speed up production cycles and facilitate the activities of the operators, semi-automatic tightening systems are effective. These ones, thanks to the continuous refilling of the screws, which are shot automatically and therefore to the elimination of the manual phases of screw pick-up and its positioning on the blade or on the piece, are able to cut cycle times by over 30%.
With different types of screws the production rate can be further accelerated by using screwdrivers capable of tightening automatically 2 different screws which are then processed by a single feeder equipped with two bowls.
If these tightening systems are also equipped with an ergonomic arm with a guided positioning device, then we can obtain the maximum productivity: fast and effective cycles not only thanks to performing machines, but also to operators who work with these devices without fatigue and supported from poka yoke systems.
Let's see in detail the features of a typical configuration:
Screw feeder with two bowls
The two vibrating bowls, with a diameter of 240 mm and a capacity of 1 liter each, feed different screws but with similar geometries: for example different lengths between 10 and 35 mm or made of different materials (for example stainless steel / burnished steel). The feeder is equipped with an integrated PLC, which controls all the machine parameters according to the assembly needs and can interface with the line PLC or the automated production systems (Industry 4.0).
Auto feed manual screwdriver
It can be an air or electric screwdriver, the screw arrives directly on the screwdriver head and the operator can select the type of screw through the selector placed in a comfortable position in the handle itself; the choice of the screw can also be managed by the PLC of the feeder through an external signal.
Ergonomic arm with positioning device
The screwdriver can be installed on an ergonomic arm equipped with a device for detecting the position and the type of the various screws on the piece and, once the sequences have been memorized, automatically enables not only the screwdriver but also the correct screw to be screwed on that position. In addition to all the ergonomic advantages for the operator's hand-arm system, this system guides the operator during tightening operations.
Cutting-edge technologies that make the factory interconnected, intelligent and more performing thanks to better man-machine collaboration. For a true Smart production.