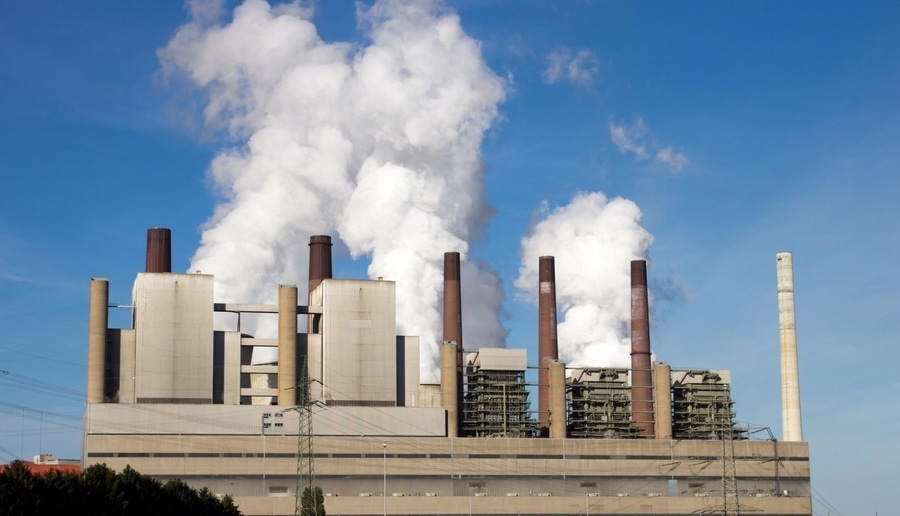
#Industry News
Customer Stories: FPI Provide Pollution Monitoring Service for Power & Steel Plants in India
Case sharing
With the development of Industrial manufacturing, more and more environmental damage problems began to appear. Over the past decade, carbon dioxide emissions from industrial activities have increased by 25%, while global temperatures have risen by 0.8°C.In addition, air pollution from industrial processes has caused respiratory diseases and other health problems in humans and animals. The burning of fossil fuels has also led to an increase in air pollutants such as ozone and particulate matter, which can damage crops and reduce crop yields. It is clear that industrial manufacturing has had a detrimental effect on the environment, and it is essential that we take steps to reduce its negative impacts on our planet.
Noticing these problems, the Indian government is becoming more focused on the environmental protection sector. To reduce the formation and emission of pollutants from the source and production process, it has successively promulgated environmental emission regulations, requiring local governments and Power plants to increase the control of conventional pollutant emissions, switching from unorganized emissions to centralized collection and treatment. In accordance with this requirement, BPSL intended to acquire a flue gas online monitoring system to track pollutant emissions in real-time in response to a request from the local government. This is exactly what FPI excels at.
Case Background
Bhushan Power and Steel (BPSL) is now officially know as JSW is a leading manufacturer of flat and long Steel products and has state-of-the-art plants at Chandigarh, Derabassi, Kolkata, and Orissa in India. These plants manufacture value-added products covering the entire steel value chain right from Coal Mining to manufacturing Pig Iron, DRI, Billets, HR Coils, CR Coils, GP/GC Sheets, Precision Tubes, Black Pipe/GI Pipe, Cable Tapes, Tor Steel, Carbon, and Special Alloy Steel Wire Rods and Rounds.
At each stage of the process, emissions such as dust, smoke and noise will be released into the air quality. The dust may contain harmful substances such as heavy metals, harmful gas SO2 ,CO,NOX which can lead to air pollution and even cause health problems.
In this context, BPSL responded to the call of the local government and planned to purchase an online flue gas monitoring system. FPI is an enterprise that provides them with professional customized solutions.
Difficulties of the Project
After analyzing user requirements, FPI summarized the difficulties of this project as the follows:
1. Adaptability of outdoor environment
During the rainy season or on sunny days there the region around the BPSL facility is frequently hot and humid, with exceptionally high temperatures when exposed to direct sunshine. Higher standards for the degree of protection, high temperature resistance, and corrosion resistance of outdoor equipment components are imposed by this climatic environment.
2. High dust severe conditions
BPSL is only separated from the National Highway by a wall. The air of the factory is constantly impacted by the dust that is created by vehicle activity on the highways and also production of plant it builds up in outdoor areas like the plant's rooftops. The dust is flying in sunny days and muddy, which also puts forth higher requirements for the, heat dissipation and ventilation efficiency of the equipment.
3. Complex maintenance work
Flue gas emission continuous on-line monitoring systems are precise instruments that require frequent calibration, inspection, and consumables replacement work. They also require additional labour, material resources, and technical assistance. The following task will require significant expenditure and take a long time to accomplish if international corporations pick transnational assignments. It cannot react quickly when on-site assistance is required. Product-related assistance is difficult to ensure when taking into account issues with cross-language communication and other factors.
Project Proposal
1. Overall objective
The project will set up an ongoing online monitoring system for pollutant discharge at important points, including DRI, DHRB, PILLAT PLANT, SINTER, BLAST FURNISE, POWER PLANT, SMS, COKEOVEN outlets and dust collection outlets, in accordance with local regulations and EPA guidelines. It will also finish uploading the data from measuring points as necessary to help local environmental safety departments manage ambient air quality.
Establishing certain production process parameters for the factory will enable users to better manage the production process and comprehend the production's energy, raw material, and final product losses. This will allow the factory to deal with any potential excessive emissions in advance.
2. Solution Architecture
FPI adapts the monitoring scheme for the user by comprehending the real monitoring needs of measurement points: WHRB 10 numbers, PILLAT PLANT- 2 numbers, DRI DEDUSTING 05 numbers SINTER 01 numbers ; BLAST FURNANCE -2 numbers; POWER PLANT-06 numbers; SMS-5 numbers; COKEOVEN, 04 numbers. Effective dust laser technology monitoring requires a full continuous dust monitoring system. After first purchasing 20 dust analyzers, the customer decided to place orders for additional 20 dust analyzers, 1N mercury analyzer, and 1 set of AQMS after seeing our team's commitment to the task.
3. Equipment FPI provided
FPI provides complete monitoring systems for process points in BPSL, and all equipment meets environmental standards.
Measures for Difficulties
1. Difficulties at the time installation
According to the local temperature and environment features of, FPI has made targeted optimization,better suitable to the local climate and working environment after beginning the installation our team experiences several challenges like distance of the analyzer covers . 7 meters, but the stack's outside diameter is 2 meters, therefore the issue was resolved after struggling a lot.
2. Complex maintenance work
Building and educating local technical service teams that are able to both carry out routine equipment maintenance and traditional equipment fault diagnostics is a priority for FPI. One of them is the regional technical group in Odisha called GREEN ENVIRO. As a result of the technical staff of GEIPL, FPI is able to execute local equipment installation instructions, equipment inspection and maintenance, and quick reaction to potentially unexpected problems.
Field Implementation
1. Main Goals
The following are the primary aims of the project's field implementation and training: Complete equipment installation guidance and commissioning, so that the equipment can fulfil the needs of typical operation. To submit environmental protection data, connect systems to the local environmental protection department's (OSPCB) portal.Provide required assistance for fine production through monitoring data to help firms discover the optimum advantage between production and environmental protection Synchronize monitoring data with DCS to enable enterprises deal with any excess emissions rapidly.
2. Equipment Installation and Commissioning
Location selection: The technical engineer of BPSL and the FPI field service engineer communicated. After thoroughly analyzing the plant's geography, the analyzer room was decided upon as the working space close to the sample site. After confirming the sample sites of each measurement point with the regional pollution control board agency, plant employees in Odisha are directed to finish the fixed work of the pertinent equipment to installation flanges in accordance with local legislation and equipment tapping requirements.
Instrument equipment installation and debugging: The installation and commissioning of the instrument equipment was started by the FPI on-site service engineer once the basic preparation work was finished . The equipment with 46 measurement sites was successfully put into use, and it finished uploading the required amount of data.
Benefits obtained
The technical engineers of BPSL conducted a study on the correlation between pollutant emissions and factory output following the installation of environmental monitoring equipment in order to identify the most complete benefit after combining economic and environmental advantages. The user had performed technical optimization based on the pollutant levels supplied by the environmental monitoring apparatus provided by FPI. through tightening fuel regulation, altering the ratio of raw materials, and implementing other technological changes. The quality of coal was effectively determined by measuring the quantity of particulate matter emissions, and efforts were made to raise coal quality in order to reduce emissions from the factory's chimneys. Environmental protection boosted interest in considering our own environment for the future and helped people recognize that it was a win-win scenario.
Conclusion
In this case, the FPI’s pollution monitoring instruments are the major problem-fixer with the following features:
· Higher adaptability to harsh natural and working environment
· Higher HMI visualization degree
· Lower system complexity
· No dependent on external equipment upload
· Simpler maintenance jobs
· Reasonable price
· Local service team standing by
With more than 20 years of experience, FPI is committed to advanced technology to provide customers with more reliable monitoring instruments. It also provides excellent customer service and offers innovative technology through a globally accessible network.
For more information, please visit: online.fpi-inc.com/
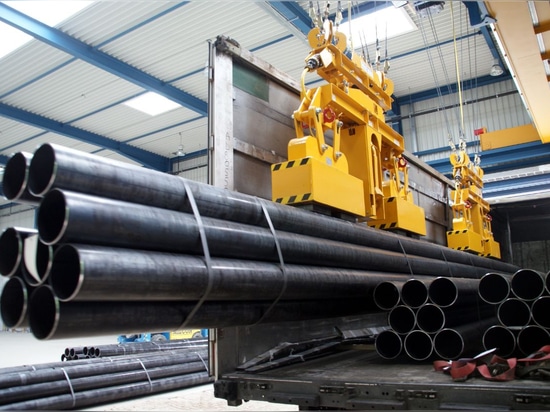
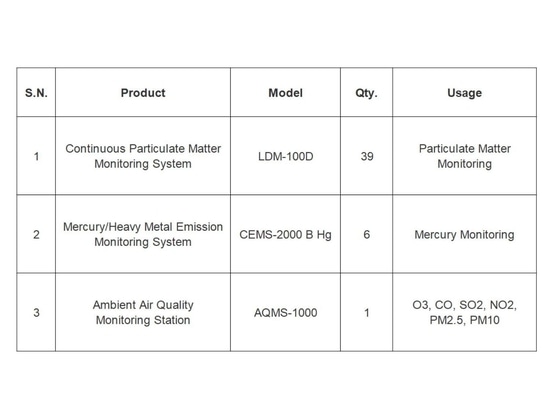
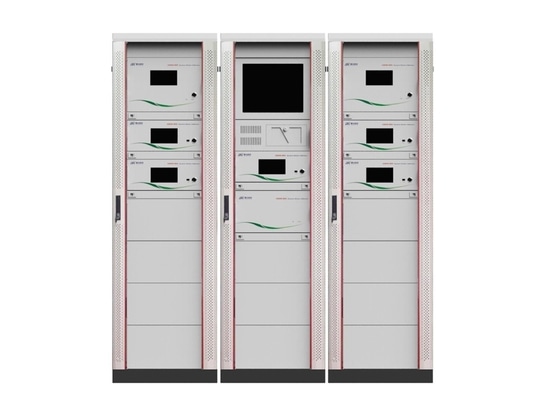
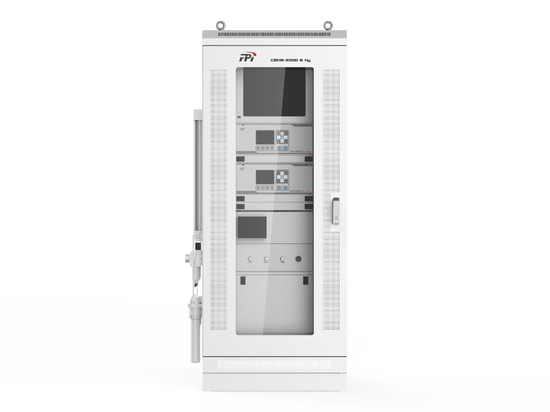