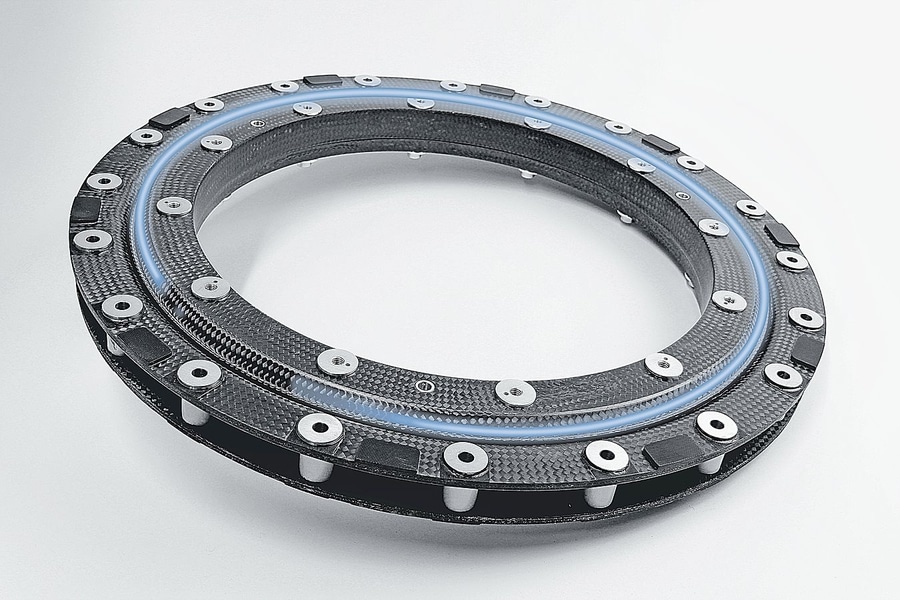
#Product Trends
The ultra-lightweight carbon bearing:
The Wire Race principle enables the construction of extremely compact bearings that fit even the smallest installation spaces and offer a variety of design options. In a specially developed grinding process the race rings get their final shape with raceways precisely adapted to the ball diameter. Thus, the rolling process does not accur directly between rolling elements and the mating structure, but rather smoothly on the four race rings. Wire race bearings can be adjusted in almost all dimensions to customer specifications. Parameters such as load capacity, stiffness, preload and adjustment can be just as variable as height, width or bore shape. Freedom of choice is also in the determination of the material for the housing parts. Irrelevant whether steel, aluminum, stainless steel, plastic or brass - the integrated wire-race bearings takes on the burden and ensures consistently precise and reliable movement. With the integration of the wires directly into the mating structure, components, assembly times and costs are significantly reduced.
What is therefore more obvious in the era of lightweight and alternative materials than testing modern materials of today''s production technology to their suitability for the integration of wire race bearings? The example of a bearing assembly with housing parts made of laminated CFRP (carbon) shows clearly that the issue of lightweight construction is not yet exhausted in bearing technology.
Design and configuration of the bearing rings was performed using 3D-CAD models. The fiber pattern was designed in a way that the subsequent load is only in tension and compression. All components are made extremely thin. Race ring bed, holes for mounting and fastening and centering diameter were placed in a single setup on a machining center.
The inner ring of the bearing assembly is divided, the outer ring is constructed in one piece. The adjustment of the bearing is done using washers. In the bores for the assembly and fastening screws metal cans were installed. This way material could be saved. The fully assembled bearing went through the same laboratory tests as its predecessors. Ordinary stress tests but also Shaker, air chamber and intake test stand were available for the study of the development laboratory. After an eight-hour running-in-process with alternating compressive and tensile load performance the results were analogous to aluminum bearings. Tests in a climate chamber with large temperature differences, and studies of hot and cold running behavior showed normal behaviour. And the weight? - The carbon bearing assembly with 300mm diameter weighs a whopping 1,800 g.