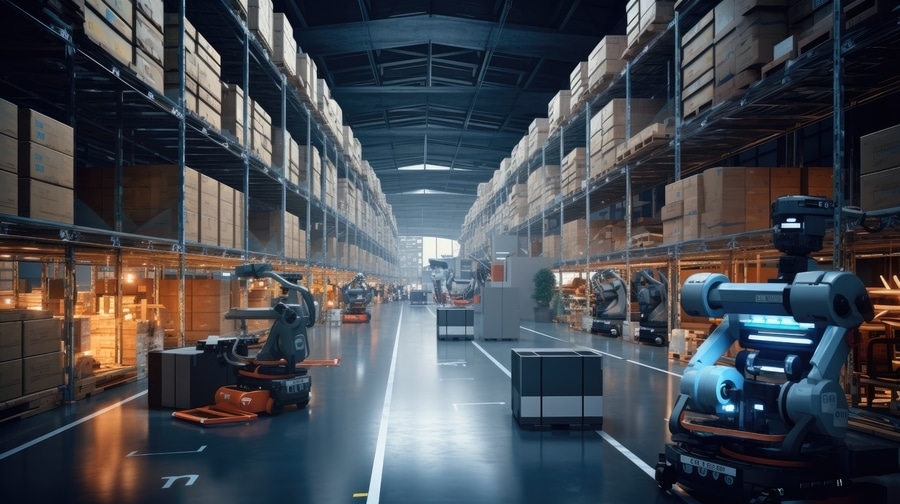
#Industry News
Automated Material Handling
Automated material handling (AMH)
Automated material handling (AMH) continues to revolutionize the way goods and materials are made, moved, packed, stored, and shipped around the world. It continues to evolve through innovations in robotics, AI, machine vision, and RFID technologies.
AMH optimizes logistics and manufacturing operations in several ways. AMH significantly increases efficiency by reducing the need for human labor, enabling faster and more precise material movement. It enhances worker safety, as physically demanding and hazardous tasks can be performed by robots.
AMH increases accuracy by reducing human errors such as picking the wrong item or quantity. AMH helps companies utilize space as efficiently as possible.
AMH and warehouse management systems provide real-time data on operational performance, material flow, and inventory levels. These insights can benefit the entire organization, from procurement to accounting.
Components of AHM systems
The mechanical equipment used in AMH systems includes check-in machines, sorters, conveyors, stackers and unstackers, totes, bins, and trolleys. Somewhere in the process there must be a scanner to read the bar code or a reader to read the RFID tag (or both.)
Circular connectors in AMH applications
Connectors used in material handling systems must meet several criteria. They must be robust enough to withstand harsh conditions such as extreme temperatures, dusty or moist environments, vibration, and other mechanical stress. Connectors should be constructed from corrosion-resistant materials and have a protection rating of IP67 or higher to guard against dust, moisture, and other contaminants.
A reliable locking mechanism helps to prevent accidental disconnection to ensure stable and secure electrical connection. Connectors should also align with the IEC 60512 standard, and be resistant to shock, vibration, and impact. rough handling, especially if the material handling applications are involved in dynamic movements.
Connectors must provide low resistance and impedance to minimize power loss and ensure efficient energy transmission. They should also have minimal signal interference to maintain reliable data communication. Some applications in material handling require electromagnetic interference (EMI) shielding because they may have sensitive electronic components that can be affected by electromagnetic interference. Connectors with proper shielding can reduce the impact of EMI on nearby electronics.
Compatibility in terms of the electrical and mechanical specifications of the equipment is another important aspect to ensure easy integration and interchangeability. Standardized options such as the M12 connector are a good choice. The installation should be seamless and straightforward to minimize downtime during maintenance.
Since material handling is applied in various industries, the connectors must comply with relevant industry standards and safety regulations. Examples of such certifications include UL, CE, or RoHS, which provide more insight into the connector's compliance. By meeting these essential requirements, connectors in material handling systems can ensure a reliable, safe, and efficient operation, contributing to the overall success of the material handling process.