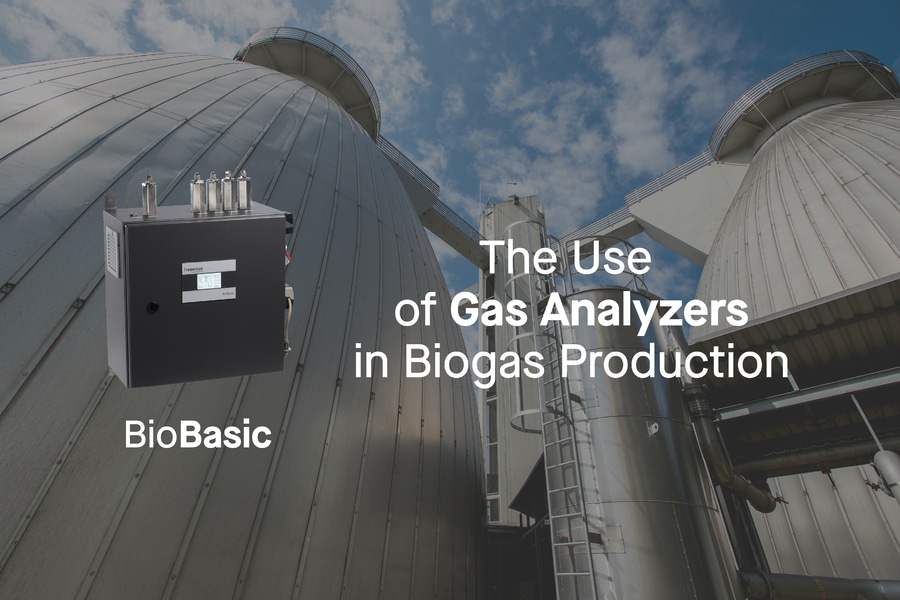
#White Papers
The Use of Gas Analyzers in Biogas Production
A Comprehensive Analysis of Benefits and Advantages
Biogas production is a cornerstone of renewable energy generation. Ensuring the efficiency of this complex process—from the fermentation of organic substrates to energy utilization or grid injection—requires precise measurement and control technologies. Gas analyzers play a pivotal role in this by continuously monitoring gas quality and composition in real time. This technical article provides an in-depth examination of how modern gas analyzers optimize process stability, economic viability, and sustainability in biogas plants.
1. Biogas Production: Why Gas Analysis is Indispensable
The biogas process consists of multiple stages, from microbial fermentation of organic materials to gas upgrading and utilization. The monitoring of the following key components is crucial:
Methane (CH₄): Primary energy carrier and a critical factor for economic feasibility.
Carbon Dioxide (CO₂): Indicator of fermentation efficiency.
Hydrogen Sulfide (H₂S): Corrosive contaminant with environmental risks.
Oxygen (O₂): Disruptive element in anaerobic processes at elevated concentrations.
Hydrogen (H₂) and Nitrogen (N₂): Early indicators of process instability.
Gas analyzers provide highly accurate measurements of these components, forming the basis for data-driven process optimization decisions.
2. Key Advantages of Gas Analyzers in Detail
2.1. Process Stability Through Real-Time Monitoring
Modern gas analyzers enable continuous monitoring of gas composition. Deviations in critical parameters—such as declining methane content—serve as early indicators of disruptions such as:
Substrate overload,
pH fluctuations,
Unwanted oxygen ingress.
Example: A sudden drop in methane concentration may indicate a fermentation imbalance. By implementing corrective actions, such as adjusting substrate feed rates, process stability can be restored swiftly.
2.2. Maximizing Methane Yield
The profitability of a biogas plant is directly linked to methane yield. Gas analyzers contribute to optimization by:
Fine-tuning fermentation conditions (temperature, pH levels),
Identifying optimal substrate mixtures,
Adjusting retention times in the digester.
Benefit: Precise process control can increase methane production by up to 15%, significantly boosting energy output.
2.3. Contaminant Reduction and Equipment Protection
Elevated hydrogen sulfide (H₂S) concentrations cause corrosion in pipelines, gas storage systems, and CHP engines. Gas analyzers detect critical H₂S levels early, enabling countermeasures such as:
Dosing iron chloride for precipitation,
Implementing biological or chemical desulfurization processes.
Additionally, they monitor the formation of other harmful gases like ammonia (NH₃), preventing environmental damage and excessive purification costs.
2.4. Cost Reduction Through Efficient Operation
The deployment of gas analyzers systematically reduces operational costs by:
Substrate optimization: Preventing overdosing and defective batches.
Asset longevity: Early detection of corrosive gases protects expensive components.
Energy efficiency: Monitoring gas quality minimizes losses in CHP systems.
Example: Precise H₂S monitoring extends engine maintenance intervals by up to 30%, resulting in five-figure annual savings.
2.5. Regulatory Compliance and Safety
Gas analyzers ensure compliance with legal requirements, including:
Emission limits for SOₓ and NOₓ,
Gas purity standards for grid injection (e.g., DVGW G260/G262),
Explosion prevention through oxygen level monitoring.
Documented analysis data also serves as official evidence for regulatory authorities, preventing fines and legal risks.
3. Applications in Downstream Processes
3.1. Biogas Upgrading to Biomethane
For grid injection, biogas must be upgraded to contain over 95% methane. Gas analyzers regulate:
CO₂ removal: Optimization of absorption or membrane separation processes.
O₂ and H₂S control: Compliance with gas network specifications.
3.2. Efficiency Optimization in CHP Units
Gas quality directly influences the efficiency and longevity of CHP engines. Gas analyzers ensure:
Consistent combustion properties,
Protection against sulfur contamination in engine oil,
Minimization of methane slip (unburned CH₄).
3.3. Emission Monitoring and Environmental Reporting
Modern analyzers track not only process gases but also exhaust emissions such as CO, NOₓ, and methane slip, enabling:
Real-time compliance with TA Luft regulations,
Reduction of CO₂ footprint through minimized methane emissions.
4. Economic and Environmental Balance
4.1. Economic Benefits
Increased revenues: Higher methane yields enhance power and heat generation.
Lower OPEX: Early fault detection reduces downtime and repair costs.
Future-proofing: Compliance with tightening environmental regulations secures long-term operating permits.
4.2. Sustainability Benefits
Climate protection: Reduction of methane slip and sulfur emissions.
Resource efficiency: Maximized energy output per substrate unit.
Circular economy: Digestate as a sustainable fertilizer replacing mineral alternatives.
5. Conclusion: Gas Analyzers as a Strategic Lever for the Energy Transition
Gas analyzers are not merely measurement instruments; they are central components of a digitalized, efficient biogas production system. They enable:
Process security through real-time data and AI-driven predictive models,
Competitive advantages via optimized operational costs and increased energy yields,
Regulatory compliance in a dynamic legal framework.
Investments in high-precision gas analysis technology often pay off within two years—a clear business case for operators aiming to future-proof and sustainably manage their facilities. In an era of increasing energy efficiency and climate neutrality demands, gas analyzers are indispensable enablers of green energy production.