
#Industry News
Additives in the textile industry
A dormant danger?
Additives in the textile industry improve product properties or simplify processing. During the manufacture of textile fibres and the production of the garments made from the fibres, they pass through a great number of processing steps in which a large number of chemicals are also used. Ideally, only the finishing chemicals, as well as the dyes, remain in the final product, but other chemicals that can have harmful effects on health have also been detected in textile pieces. FRITSCH offers the possibility to grind textiles and protective masks with the Universal Cutting Mill PULVERISETTE 19 and thus prepare them for further analysis.
Processing of textiles
The task was to comminute textiles and FFP2 protective masks with the PULVERISETTE 19. In the first step, the textiles were manually pre-shredded to a size of approx. 7 x 8 cm.
First test
The PULVERISETTE 19 was equipped with the standard rotor with V-cutting edges in hardened stainless steel, and a sieve cassette 2 mm square perforation. In order to achieve a better throughput, the high-performance Cyclone separator made of stainless steel was connected. The textile samples were comminuted in less than one minute. For the larger textile pieces (skirt and T-shirt), it took about 2 minutes, for a yield of 105 grams of ground material. It should be noted that the volume of the ground material is about 30 % higher than the original sample pattern, due to the structural change of the particles. The residue in the grinding chamber was 5-10 % sample material.
Second test: comminution of FFP2 masks
The second test documents the shredding of FFP2 protective masks. Metal parts which were on the masks had to be removed prior to the comminution process. The PULVERISETTE 19 was equipped with the standard rotor with V-cutting edges, as well as a sieve cassette 4 mm square perforation. The grinding time was 45 seconds.
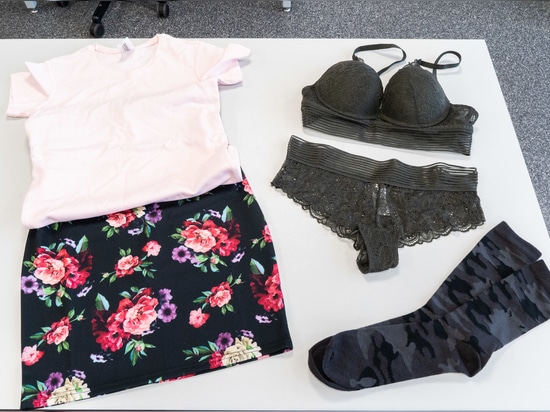


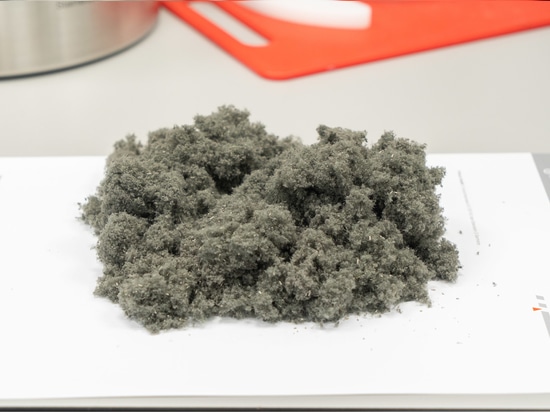
