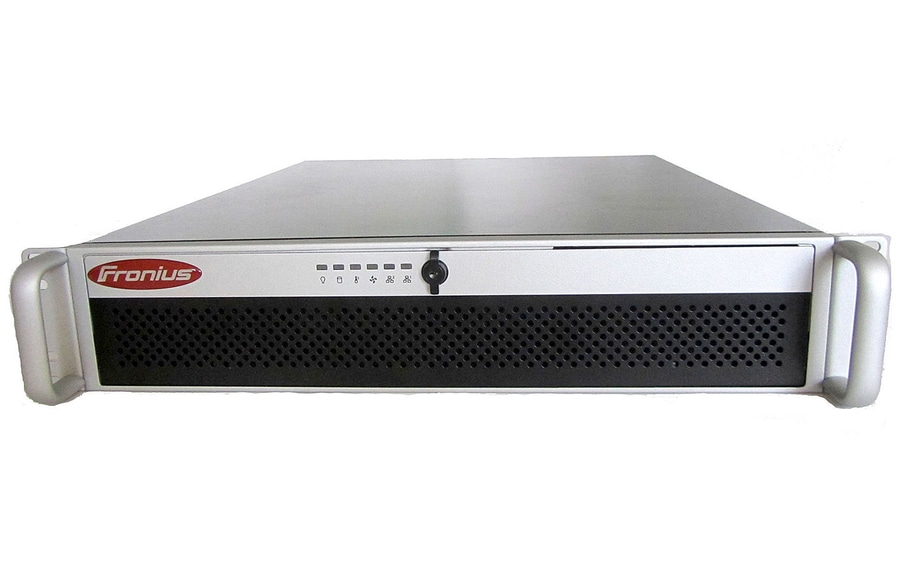
#Product Trends
Fronius presents WeldCube, a new documentation and data analysis system
Keeping an overview of all welding technology data at all times
The documentation and analysis of process data is gaining increasing significance for welding technology. After all, it is only with complete accuracy and transparency that targeted optimisation can become a possibility. With this in mind, the international welding technology specialist Fronius has developed WeldCube, a documentation and data analysis system. WeldCube connects up to 50 power sources and makes accurate and continuous quality assurance and evaluation of countless parameters possible. As a result, users are able to significantly improve the output and reliability of their production operations.
Wels, 12/04/2015 - The WeldCube solution is based on an industrial PC (IPC) with integrated software, which is used to connect up to 50 power sources via the network. The system is compatible with all digital Fronius series, the resistance spot welding system DeltaSpot and the intelligent welding system platform TPS/i. This enables the user to document and evaluate a wealth of data - including current, voltage, wire speed, welding speed and time, arc length and dynamic correction, and job numbers - during both manual and robot-assisted welding processes. This data is visualised in order to achieve an accurate analysis, then output via a web browser, which enables the results to be accessed conveniently from any computer or mobile device.
Thanks to the Plug & Play principle, installing the WeldCube is extremely easy. Once the system is up and running for the first time, virtually zero maintenance is required to keep it going. As Fronius further develops and hones the technology, updates will be provided that the user can install themselves. Individual adjustments and programming are easily implemented thanks to a range of packages that can be added to the standard functions. As a result, customised solutions tailored to meet the customer's exact requirements can be delivered.
The extensive functions of the WeldCube ensure a wide range of different uses are possible. The actual values for each power source can be documented both in relation to the machine and overall – and in real-time too. The user is also able to continually monitor and evaluate additional data, including consumption data relating to gas, wire and energy consumption. Set values, such as job data, can also be observed and are recorded by the system for the entire service life of a welding system. When used in combination with Fronius' new TPS/i welding system platform, it is also possible to edit jobs and make comparisons across power sources. All the values can be exported in different file formats or printed out from the IPC directly.
A range of analysis tools are available for fast and reliable troubleshooting, enabling Fronius customers to monitor - and, if necessary, optimise - the quality and output of their welding processes. Continuous data analysis can also prevent production downtime and increase reliability. Different service packages ensure that the user can depend on a system that has been perfectly installed, meets their precise needs, and has a high level of availability – and which can be operated without any difficulty.