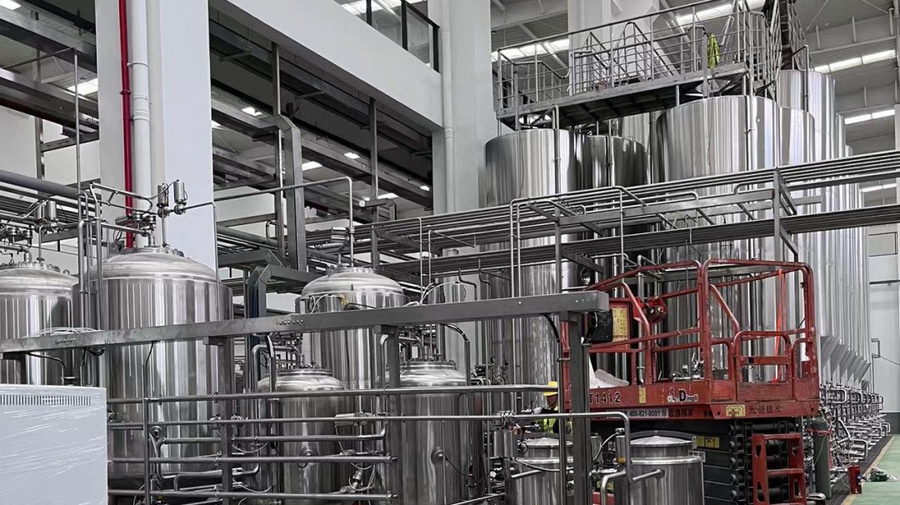
#Trade Shows & Events
Canned solutions
Ensure production and monitor operating status in real time
In the modern canning industry, ensuring the safety and efficiency of the production process is crucial.
With the development of intelligence and digitization, traditional analog signal transmission faces many challenges, including reduced measurement accuracy, signal interference, and increased cost. Therefore, it is particularly important to adopt more advanced digital signal solutions.
Pain points of the canning industry:
1.Measurement accuracy: Traditional sensors require multiple conversions to obtain final digital and analog data, which may lead to inaccurate measurement values and thus affect production safety.
2.Signal transmission interference: Analog signals rely on shielded cables, which not only increases material costs, but may also be subject to external electromagnetic interference, affecting the stability of data transmission.
3.Equipment space and cost: Equipment using analog signals often requires expensive input cards and takes up valuable space in the control cabinet
With the advancement of digitization and intelligence, analog signals are gradually replaced by digital signals that are more resistant to interference and have long-distance transmission capabilities.
By introducing digital signal transmission technologies such as IO-Link, the canning industry can realize significant advantages. IO-Link analog adapter can connect traditional analog sensors (such as pressure, temperature, liquid level sensors) to the IO-Link network to convert analog signals to digital signals, thereby achieving more flexible and intelligent control.
Advantages of IO-Link transmission solution:
1.Efficient data transmission: IO-Link technology uses 24V signals to send fully digital signals, ensuring that the sensor output only needs to be converted once during transmission. This feature avoids the complexity and signal loss caused by multiple conversions, thereby improving the accuracy and reliability of data transmission.
2.Strong anti-interference: IO-Link signals are not sensitive to external environmental influences, and IO-Link can operate stably even in complex industrial environments. Digital output can be achieved through ordinary cables, simplifying wiring requirements and reducing the complexity of system implementation.
3.Reduce costs and save space: Using IO-Link technology, enterprises do not need to invest in expensive analog input cards, significantly reducing equipment procurement and maintenance costs. At the same time, this also frees up space in the control cabinet, making the control system cleaner and more efficient, and facilitating subsequent expansion and upgrades.
4.Real-time monitoring and remote management: IO-Link technology enables digital transmission of measurement values, allowing accurate measurement data to be sent directly to the controller. This includes the sensor's self-diagnosis function to facilitate real-time monitoring of equipment health; remote parameter setting to quickly adapt to production needs; and usage frequency reading to help companies optimize the production process and improve efficiency.
Summarize
The application of IO-Link not only improves the stability and reliability of data transmission, but also provides strong support for the automation and intelligent transformation of the canning industry. By adopting this advanced technology, canning companies can better control the production process, improve overall operational efficiency, and ensure production safety.