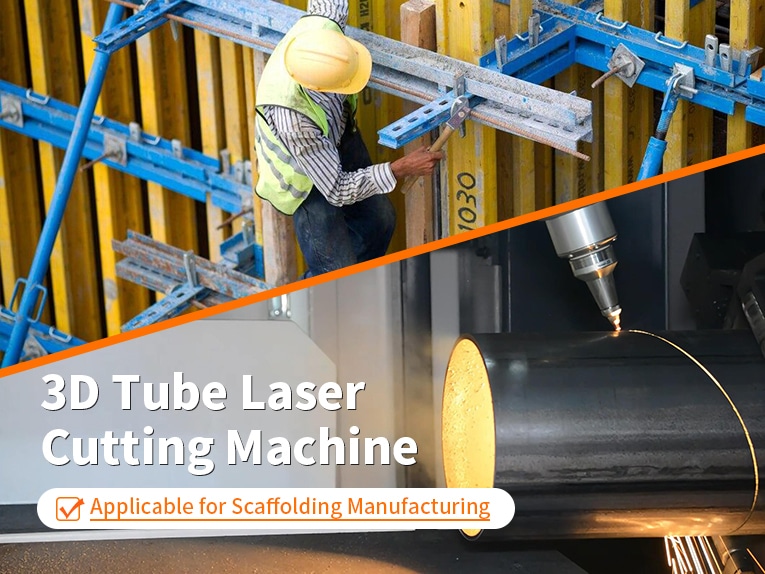
#Industry News
Why Did the Scaffolding Manufacturer Choose Golden Laser 3D Tube Laser Cutting Machine?
Full Laser Services From Ideas to Delivery
Metal scaffolding usually uses carbon steel, stainless steel, aluminum, and other materials. Common scaffolding types include Tube-and-Clamp Scaffolding, Cuplock/System Scaffolding, Frame Scaffolding, and Mobile Scaffolding (Aluminum). 3D laser cutting allows for complex angles, which is useful for joints in scaffolding. Precision is key because scaffolding requires accurate joints for safety. The 3D capability allows complex cuts, which is important for the angles and connections in scaffolding. Efficiency factors like automation and speed would reduce production time. Versatility in handling different metals (steel, aluminum) and thicknesses is a plus. Cost savings from reduced waste and labor.
Golden Laser 3D Tube Laser Cutting Machine is a top-tier choice for cutting metal scaffolding tubes due to its advanced technology, precision, and efficiency.
1. 3D Tube Cutting Capability for Complex Geometries
Scaffolding often requires angled cuts, notches, and holes for joints, brackets, or connections.
The machine’s rotary axis and 5-axis (or 6-axis) motion enable 3D cutting on round, square, or rectangular tubes, producing weld-ready joints without secondary processing.
Example: Cut beveled edges for seamless welding of diagonal braces or endplates.
2. High Precision and Repeatability
Laser cutting accuracy (±0.1 mm) ensures tight tolerances critical for scaffolding assembly. Misaligned holes or uneven cuts can compromise structural integrity.
CNC automation guarantees identical cuts across thousands of tubes, ideal for the mass production of standardized scaffolding components.
3. Material Versatility
Tube laser Cuts steel (mild, galvanized, stainless) and aluminum, the two most common metals used in scaffolding.
Handles a wide range of thicknesses (1–12 mm for steel, 1–8 mm for aluminum), accommodating everything from lightweight mobile scaffolds to heavy-duty industrial systems.
4. Speed and Productivity
High-speed laser cutting (up to 3 m/min for steel) reduces cycle times compared to plasma cutting or sawing.
Automatic feeding systems (optional) allow continuous processing of long scaffolding tubes (up to 12 meters), minimizing downtime.
5. Minimal Material Waste
Nesting software optimizes tube layouts to maximize material usage, crucial for cost-effective scaffolding production.
Reduces scrap by up to 30% compared to traditional cutting methods.
6. Superior Edge Quality
Fiber laser technology produces clean, burr-free edges, eliminating the need for grinding or deburring.
Smooth edges ensure safe handling and reduce wear on scaffolding joints during assembly/disassembly.
7. Cost Efficiency
Low operating costs: Fiber lasers consume less power than CO₂ lasers.
Reduced labor costs: Automation minimizes manual intervention.
Long-term ROI: High durability and minimal maintenance (e.g., no consumable parts like blades or electrodes).
8. Safety and Compliance
Fume extraction systems integrated into the machine safely remove toxic fumes (e.g., zinc oxide from galvanized steel).
The enclosed tube cutting area protects operators from laser radiation and sparks.
9. Software Integration
Golden Laser’s proprietary laser software supports CAD/CAM file formats, enabling a seamless transition from design to production.
Simulates pipe laser cutting paths to avoid collisions and optimize workflow.
10. Adaptability to Scaffolding Standards
Customizable programs for global scaffolding systems (e.g., cuplock, ringlock, tube-and-clamp).
Easily adjusts to regional specifications (e.g., EN 39, BS 1139 standards for tube dimensions).
3D Tube Laser Ideal Applications
• High-volume scaffolding manufacturing (e.g., factories producing modular systems).
• Custom scaffolding for complex structures (e.g., curved or angled designs).
• Repairs/refurbishment of damaged scaffolding tubes (precision cuts for replacements).