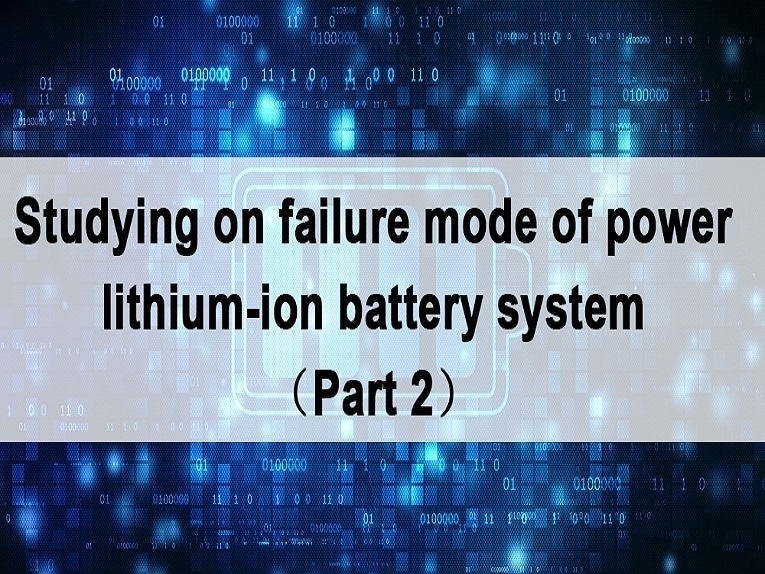
#Industry News
Studying on failure mode of power lithium-ion battery system(Part 2)
Studying on failure mode of power lithium-ion battery system(Part 2)
BMS failure mode
The single failure of the battery is not only related to the battery itself, but also related to the failure of the battery management System BMS. BMS failure mode can also cause serious accidents, including the following categories:
1.BMS voltage test failure causes battery overcharge or over discharge:
The voltage test line fails due to poor connection, wire pressing process or contact. BMS has no voltage information and does not stop when charging. Battery overcharge will cause fire and explosion. Most of lithium iron phosphate overcharge above 5V is just smoke, but once the ternary battery is overcharged, it will explode.
Moreover, overcharging can easily lead to the release of gas from the electrolyte analysis in the lithium-ion battery, resulting in battery bulging and even smoking and fire in serious cases; The over discharge of the battery will lead to the damage of the molecular structure of the positive material of the battery, resulting in failure to charge; At the same time, the battery voltage is too low, resulting in electrolyte analysis, drying up, lithium precipitation and short circuit in the battery. Reliable voltage acquisition line shall be selected during system design, and shall be strictly controlled in the processing process to prevent the failure of voltage acquisition line.
2.BMS current test failure
Hall sensor fails, BMS cannot collect current, SOC cannot be calculated, and the deviation is large. Failure of the current test may result in excessive charging current. If the charging current is large, the internal heating of the cell is large, and the temperature exceeds a certain temperature, the curing capacity of the diaphragm will be attenuated, which will seriously affect the service life of the battery.
3.BMS temperature test failure
The failure of temperature test leads to the high working temperature of the battery and irreversible reaction of the battery, which has a great impact on the battery capacity and internal resistance. The calendar life of the battery cell is directly related to the temperature. The number of cycles at 45 ° C is half that at 25 ° C. In addition, the battery is prone to bulging, liquid leakage, explosion and other problems when the temperature is too high. Therefore, the temperature of the battery should be strictly controlled between 20-45 ° C during the use of the battery, In addition to effectively improving the service life and reliability of the battery, it can also effectively guard against short circuit and high-temperature thermal runaway caused by lithium evolution during low-temperature charging of the battery.
4.Insulation monitoring failure
Insulation failure will occur in case of deformation or liquid leakage of power battery system. If BMS is not detected, personal electric shock may occur. Therefore, the BMS system should have the highest requirements for monitoring sensors. Avoiding the failure of the monitoring system can greatly improve the safety of the power battery.
5.Electromagnetic compatibility problem communication failure
For BMS system, EMC mainly tests its anti electromagnetic interference ability. Electromagnetic interference will cause BMS communication failure, causing the above problems.
6.Large SOC estimation deviation
At present, the common problem of all BMS manufacturers is only the difference of deviation size. Basically, the current inspection standard requirements are within 5%, which should be difficult for most manufacturers’ BMS to achieve, because the SOC error will be greater and greater in actual use, because the use environment is more complex and there are more conditions affecting the accuracy.
Pack system integration failure mode
1.Failure of busbar:
In case of bolt connection, in the later use process, the oxidation and falling off of the bolt or the loosening of the bolt caused by vibration will lead to a lot of heat at the conductor connection, and in extreme cases, it will lead to the ignition of the power battery. Therefore, most power battery system manufacturers adopt laser welding at the connection between cells or between modules, or add temperature sensors at the connection to avoid the failure of bus bar by means of detection.
2.Failure of main circuit connector of power battery system:
The high voltage line of the power battery system is connected with the external high voltage system through a connector. The performance of the connector is unreliable. Connector will be in high-temperature ablation when virtual connection occurs under vibration. Generally speaking, when the connector temperature exceeds 90 degrees, the connection failure will occur. Therefore, in the system design, the connector needs to increase the high-voltage interlock function, or add a temperature sensor between the connectors to monitor the temperature of the connector at all times to prevent the failure of the connector.
3.High voltage contactor sticking
The contactor has a certain number of on load disconnection, and most contactors are ablated when the high current on load is closed. In the system design, the double relay scheme is generally adopted, and the control is closed in order to avoid the sticking of high-voltage contactor.
4.Fuse overcurrent protection failure:
The selection and matching of fuses in high-voltage system components need to be comprehensively considered. Vibration or external collision and extrusion lead to deformation of power battery, seal failure and IP grade reduction. Therefore, the collision protection of battery box structure needs to be considered in system design.
According to the above failure modes of the power battery system, scientific researchers and battery manufacturers need to continuously improve the process and technology to improve the safety of lithium battery cells. BMS system manufacturers should fully understand the performance of the battery and design a safe and reliable battery system based on the safety design principle of power battery. At the same time, correct use is the final barrier to ensure the safety of the battery. Users should correctly use the power battery system, eliminate mechanical abuse, thermal abuse and electrical abuse, and effectively improve the safety and reliability of electric vehicles.
Conclusion
In the failure mode of lithium-ion power battery, the failure of cell, BMS and pack is related to internal short circuit, ambient temperature, overcharge and discharge, physical collision and extrusion, etc. GDBELL can provide this series of testing equipment, which conforms to most international standards and can give practical and effective professional data. With such data reference, it can give practical help to the improvement of production process and further improve the safety and reliability of power lithium battery. GDBELL can well meet your regular and customized needs. If necessary, please contact us. We’ll get back to you within 12 hours.