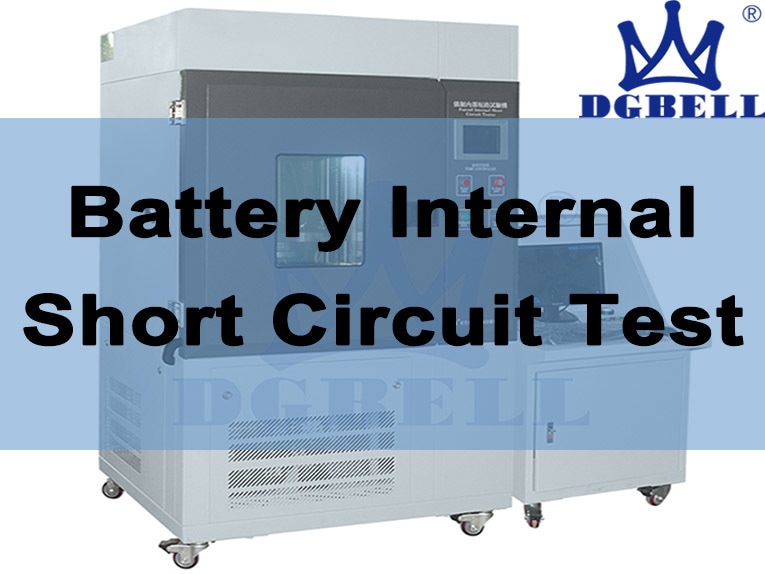
#Industry News
Battery Internal Short Circuit Test
During the battery production process, due to negligence in process control, extremely small metal particles were mixed inside the lithium-ion battery.
During battery use, temperature changes or various impact metal particles pierced the separator between the positive and negative electrodes, causing a short circuit inside the battery and causing a large amount of heat, causing the battery to catch fire.
Due to the accidental inclusion of metal particles during the production process, it is difficult to completely prevent such incidents from occurring. Therefore, we attempt to simulate the situation where metal particles penetrate the separator and cause internal short circuits through the “forced internal short circuit test”.
If lithium-ion batteries can ensure that there is no risk of fire or explosion during the test process, it can effectively ensure that even if metal particles are mixed inside the battery during the production process, they cannot penetrate the separator between the positive and negative electrodes. Or even if the diaphragm is punctured and an internal short circuit is caused, there will still be no danger of fire or explosion that endangers personal safety.
1.Test chamber
The “Single Battery Forced Internal Short Circuit Test” requires the test to be conducted in an environment of 10~60 ℃, with a pressure application speed of 0.1mms, an accuracy requirement of ± 0.005ms, and a maximum pressure of 1000N. In addition, voltage and pressure data need to be collected during the test process.
When the voltage drops by more than 50mV or when the applied pressure meets the requirements (cylindrical battery 800N, square battery 400N), the pressure should be stopped and maintained for 30s. This puts forward strict requirements for pressure equipment: firstly, to control the speed and accuracy of pressure application; secondly, to ensure the pressure application; thirdly, to control the environmental temperature; fourthly, to meet the frequency and accuracy of voltage and pressure data collection.
How to ensure an accurate speed of 0.1 ± 0.01mm/s and a pressure of 100N in high and low temperature environments is a key technology for whether the test equipment can meet the test standards. To generate a speed that meets the test requirements, the equipment material selection must first meet the usage requirements of the test environment temperature, and the other key is to select the power source and control the accuracy of the transmission mechanism design.
We have developed a ” Battery Internal Short Circuit Test Chamber ” through repeated experiments, which can achieve high-precision pressure application. By equipped with high-precision high and low temperature boxes and data acquisition systems, we fully meet the temperature requirements and data acquisition requirements of the pressure equipment.
2.Charging steps for the test
The single battery forced internal short circuit test is a test conducted on a fully charged single battery. The charging conditions are to stabilize for 1-4 hours at the upper and lower test temperatures respectively, and then use the upper charging voltage and maximum charging current to charge until the current value under constant voltage charging control becomes 0.05ItA.
The upper and lower limit test temperatures indicate that when the battery can use the upper limit charging voltage and maximum charging current, the highest and lowest temperatures on the surface of the battery cell are selected for charging under the upper and lower limit test temperature conditions based on the material characteristics of the lithium battery.
The upper and lower test temperatures proposed by JSC 8714 are 45 ℃ and 10 ℃, respectively. The upper charging voltage is 4.25V, which is based on the characteristics of commonly used lithium-ion batteries (lithium cobalt oxide negative electrode • carbon positive electrode) materials on the market and cannot represent all lithium batteries.
JSC8714 proposes that if new upper and lower test temperatures and upper charging voltages need to be used, certain tests need to be conducted and additional data basis needs to be supplemented. The investigation content for determining the new upper limit charging voltage includes: the structural stability of the positive electrode material, the lithium absorption of the negative electrode material, and the structural stability of the electrolyte;
When determining the new upper and lower limit test temperatures, the inspection content includes the structural stability of the positive electrode material, the structural stability of the electrolyte, and other material characteristics that need to ensure the safety of the charged battery at the new upper limit test temperature.
In addition, 5 ℃ is added to the new upper limit test temperature, which is applicable to the charging conditions of JSC8714 clause 5.1, and meets the test requirements of clauses 5.2-5.5. Based on the lithium ion absorption of the negative electrode material The mobility of lithium ions in the electrolyte (corresponding to temperature) should ensure the safety of the charged battery at the new lower limit test temperature, and 5 ℃ should be added to the new lower limit test temperature to meet the charging conditions of 5.1 and meet the test requirements of 5.2 to 5.5.
3.Pressure application steps
Under the upper and lower temperature conditions, use the pressurizing tooling to apply pressure at a speed of 0.1mm/s to the position where a small nickel plate is placed on a single battery. At the same time, use the Voltmeter to monitor the voltage change at the output terminal of the single battery. When a voltage drop greater than 50mV is observed or when the applied pressure meets the requirements (cylindrical battery 800N square battery 400N), stop reducing the pressurizing tool, hold it for 30s, and then remove the pressure.
Using a pressure level as slow as 0.1mm/s can better control the time and severity level of internal short circuits. When a voltage drop of 5mV occurs during the pressure application process, it indicates that the small nickel sheet placed inside the single battery has punctured the battery separator under pressure, causing an internal short circuit in the single battery. At this time, there is no need to continue applying pressure. If the pressure reaches 800N and the square battery is pressurized for 400N, there is still no voltage drop, indicating that the separator of the single battery can effectively prevent the puncture of the small nickel sheet, This can also prevent the occurrence of internal short circuits in a single battery after mixing with small metal particles.
4.Conclusion
With the increasingly widespread application of lithium-ion batteries and the continuous progress of related technologies, their safety requirements are also increasing. Various countries, institutions, and enterprises are actively researching detection methods that can more accurately and effectively evaluate the safety of lithium-ion batteries. Only by continuously researching and exploring the electrochemical and environmental characteristics of lithium-ion batteries can we develop more scientific, targeted, and operable lithium-ion battery testing projects and conditions.