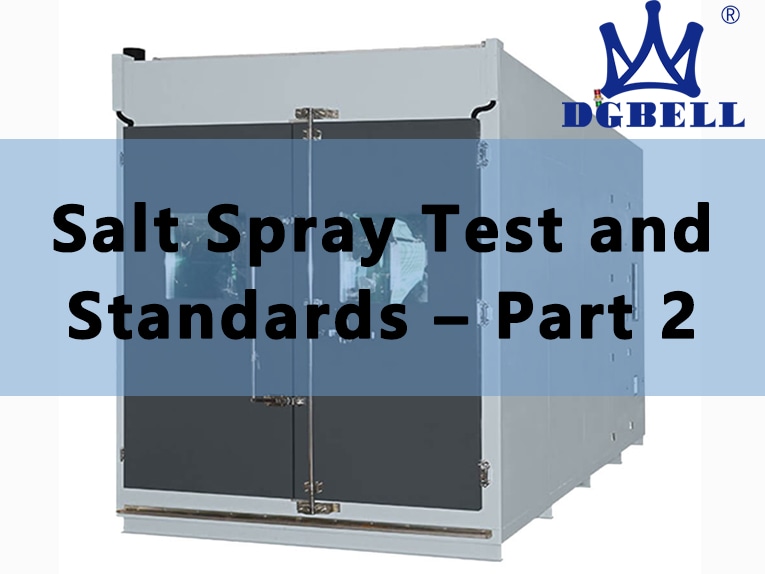
#Industry News
Salt Spray Test and Standards – Part 2
Salt Spray Test and Standards – Part 2
3.2 Volkswagen Standard PV 1210
PV 1210 is the cyclic salt spray corrosion standard for body and accessories of Volkswagen AG, and is the most widely used cyclic corrosion test standard. This standard is applicable to the corrosion detection of coated body, body sheet, structural components and other test samples.
The test was divided into three stages: spraying salt spray, standard climate preservation and humid and hot storage. Spray salt spray according to NSS method in DIN 50021 standard, with NaCl mass concentration of (50 ± 5) g/l and spraying time of 4 h; The standard climate shall be kept for 4 h under the condition of 23/50-2 in DIN 50014 standard; The wet and hot storage shall be conducted under the constant state (KK) conditions in DIN 50017 standard (40+3) ℃ and 100% humidity for 16 h. After 5 cycles, it shall be stored in the standard climate for 2 days before continuing.
The test can be carried out for 15, 30, 60 or 90 Cycles, and then the corrosion of the sample is evaluated, including the type of corrosion (coating or substrate corrosion), the form of corrosion (plane corrosion or edge corrosion) and the progress of corrosion (adhesion reduction, whether there are bubbles).
3.3 General Motors Standard GMW 14872
GMW 14872 is the cyclic corrosion laboratory test standard of general motors, which is applicable to automotive metal parts. The test process includes salt water spray, normal temperature storage, humidity storage, dry storage and other stages. In the normal temperature storage stage, the temperature is (25+3) ℃, and the humidity is 45%+10%, lasting for 8 h; In the humidity storage stage, the temperature is (49+2) ℃, and the humidity is 100%, lasting for 8 h; In the dry storage stage, the temperature is (60+2) ℃, and the humidity is ≤ 30%, lasting for 8 h.
For exterior parts, spray salt spray 4 times per cycle, 28 cycles without surface corrosion and 52 cycles without substrate corrosion; for interior parts, spray salt spray once every 5 cycles, depending on the location, the maximum requirement is 22 cycles without surface corrosion and 40 cycles without substrate corrosion; For engine compartment parts, the maximum requirement is to spray salt spray 4 times per cycle, 9 cycles without surface corrosion and 51 cycles without substrate corrosion; For underbody parts, spray salt spray for 4 times per cycle. The maximum requirement is 6 cycles without surface corrosion and 68 cycles without substrate corrosion.
3.4 Chrysler Standard SAEJ 2334
SAEJ 2334 is a laboratory test standard for corrosion of decorative materials formulated by the automotive corrosion and Protection Committee of the international society of automotive engineers. It is applicable to evaluate the corrosion resistance of specific coating systems, substrates, processes or designs. The test process includes three stages: humidity storage, salt water spray and high temperature storage: humidity storage requires humidity of 100%, temperature of 50 ℃, and maintenance for 6 h; Salt water spray for 15 min; High temperature storage requires temperature of 60 ℃, humidity of 50%, storage for 17 h and 45 min.
For severely corroded exterior parts and closures, such as wiper rods, B-pillar and C-pillar exterior trim panels, it is required to have no corrosion after 60 cycles and no function loss after 120 cycles; for cockpit and internal visible parts, such as inner handle and seat headrest support, it is required to have no corrosion after 30 cycles and no function loss after 120 cycles.
3.5 Nissan Engineering Standard M 0158
Nissan’s cyclic salt spray test provides three different cyclic methods for different corrosion degrees of parts.
The first method is applicable to commonly corroded parts, such as body parts, fasteners, etc. the whole cycle is divided into three stages: neutral salt spray corrosion, drying and moisture retention, with a total time of 8 h.
The second method is applicable to severely corroded parts such as outer plates. On the basis of the first test cycle, the number of cycles of moisture preservation and drying preservation is increased.
The third method is applicable to the parts with serious internal corrosion. The neutral salt spray is changed to salt water immersion, and the test conditions are more stringent than the first two methods.
3.6 SAIC Roewe SMC 30054
SMC 30054 is the cyclic corrosion test standard of Shanghai Automotive Group Co., Ltd. Firstly, spray salt spray for 6 h, and then store in high temperature and high humidity and high temperature and dry environment respectively. The specific cycle times are determined according to the corrosion degree of the parts and the installation position, and are generally selected within the range of 20~720 cycles.
4.Summary
From the above comparison, it can be seen that although the contents of each standard are different, the basic test stages are roughly the same, including salt spray stage, drying stage and wet stage. The national standard GB/T 24195 divides the circulating salt spray into two types. The salt spray is sprayed at different times for different corrosion conditions, which is highly targeted and operable. It is also the only standard in the circulating corrosion standard that uses acid salt spray conditions. The Volkswagen standard PV 1210 does not set the cycle process for different parts, but sets different cycle times. GM standard GMW 14872 has the longest salt spray time among all the above standards, reaching 8 h, which shows its strict requirements. Chrysler Automobile standard SAEJ 2334 has the longest retention time of high temperature and humidity, reaching 17 h 45 min. it can be seen that it has the most stringent requirements for corrosion resistance in harsh environments. Nissan engineering standard M 0158 subdivides the cycle conditions into three stages, and formulates different cycle stages for different corrosion parts, which can more truly simulate the actual corrosion environment, and is also the only standard requiring parts to be soaked in salt water. SMC 30054 standard of SAIC Roewe requires that the temperature in the high-temperature holding phase of the test changes continuously, and the holding time in the dry and wet phase is longer.
It can be seen that most European and American test standards adopt the same cycle process and simulate different corrosion degrees through different cycle times; Japanese standards subdivide corrosion parts and formulate different corrosion standards for different parts, which makes the simulation more realistic. Most of the domestic self owned brand automobile enterprises have not developed their own cyclic corrosion test standards, but draw lessons from foreign standards. The corrosion requirements are low, so it is urgent to strengthen the cyclic corrosion test.
In a word, the cyclic salt spray test can simulate the actual use conditions of users through different temperature and humidity changes. Compared with the neutral salt spray test, it can accelerate the corrosion and better reflect the corrosion resistance of parts. Through the cyclic salt spray corrosion test, the effective anti-corrosion control in the early stage of the development of metal parts is of great significance to prolong the service life of metal parts.