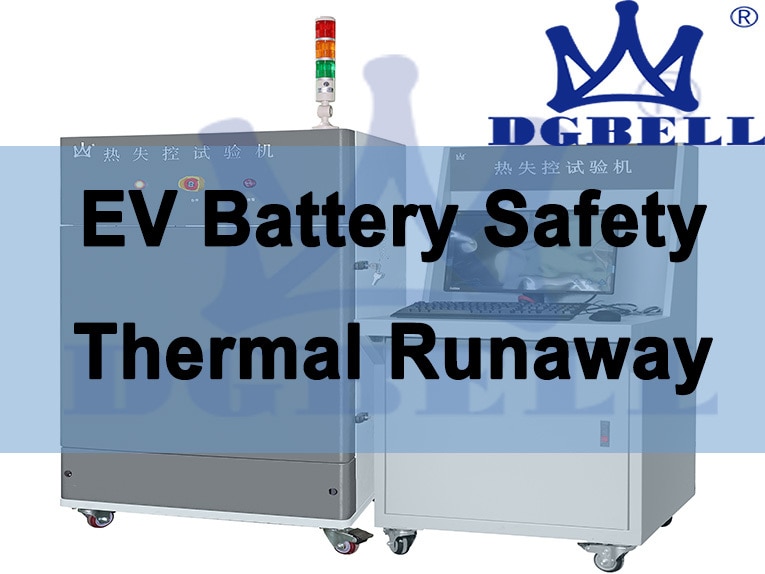
#Industry News
About EV Lithium Battery Safety — Thermal Runaway
About EV Lithium Battery Safety — Thermal Runaway
The main reason for electric vehicle fires is due to battery fires, which are mainly caused by thermal runaway of the battery. The so-called thermal runaway refers to the heating of power batteries during operation. When the battery temperature is too high or the charging voltage is too high, a chain of chemical reactions will occur inside the battery, causing a sharp increase in internal pressure and temperature, leading to thermal runaway and ultimately combustion.
There are various reasons for thermal runaway of batteries, which may be due to uneven temperature of the battery pack itself, high temperature in local areas, external short circuits, internal short circuits, and other reasons that can cause ignition. The design of the separator is one of the important factors affecting the occurrence of internal short circuits in batteries. If the design margin of the diaphragm is insufficient or the design direction is incorrect, it will affect the mechanical ductility and flexibility of the diaphragm, leading to shrinkage during the charging process, and then the positive and negative poles will come into contact with each other, causing a short circuit.
At the same time, the production process is not strictly controlled, and metal particles are mixed into the battery cells. These impurities can cause differential reactions on the electrode surface during the charging and discharging process, which can accumulate and puncture the diaphragm, leading to short circuits. Once a battery cell encounters a problem, such as a short circuit, open circuit, etc., it will affect other cells in the battery pack, causing serious internal problems and ultimately leading to safety issues.
1 Battery Management System
Electric vehicles contain a large amount of lithium batteries, and if one link is not done well, a chain reaction will occur. Apart from the efforts of battery manufacturers and charging companies, the responsibility that vehicle manufacturers actually need to bear is not light. Because the Battery Management System (BMS) is an important element in the overall architecture of electric vehicles, and these are currently designed by the vehicle manufacturer. BMS is located at the core of the power battery system and is a core component for battery protection and management. BMS not only ensures the safe and reliable use of the battery, but also controls the charging and discharging of the battery pack, and reports the basic parameters and fault information of the power battery system to the vehicle controller. It can be said that it is a bridge between the battery, the vehicle controller, and the driver.
The thermal management system is important in BMS, and its basic working principle is to maintain the temperature of the battery pack within a certain temperature range through cooling or heating to ensure the performance and lifespan of the battery cells. The thermal management system is mainly divided into three categories: heating system, air-cooled system, and water-cooled system. Different design schemes have different working principles, but there is a possibility of causing thermal runaway of the battery pack.
Firstly, for the water-cooled system, it is a thermal management method that reduces the temperature of the battery cells by exchanging heat through liquid convection. However, the water-cooled plate is usually located at the bottom of the battery pack and is placed on the chassis of the vehicle. Abnormal impacts, bottom scratches, or long-term reliability failure of the water-cooled design structure during long-term operation may cause coolant leakage, leading to insulation failure of the battery pack and thermal runaway of the entire vehicle.
Secondly, the air-cooled system is a thermal management method that uses air as the medium and utilizes thermal convection to reduce the temperature of battery cells. However, air-cooled design can increase the difficulty of sealing the battery system. During long-term operation of the vehicle, the sealing structure fails, posing a risk of thermal runaway due to water ingress and insulation failure during driving in cloudy and rainy days. Finally, for electric vehicles mainly used in cold regions, a heating system is used, which uses a heating film to heat the battery pack and maintain it within a reasonable working temperature range, ensuring the performance of the battery cells. The unreasonable design of the heating power or assembly scheme of the heating film, or its long-term reliability failure, may also lead to insulation failure of the battery pack, which can lead to thermal runaway events.
2 Battery materials
At present, there are technical solutions for these problems of thermal management, and whether these problems can be effectively solved is an indicator reflecting the progressiveness technology of each manufacturer. In order to solve the problem of electric vehicle range, improving the energy ratio of power batteries is a necessary path for development. To improve the energy ratio, it is necessary to adjust the proportion of materials related to lithium batteries.
At present, most power batteries for passenger cars use a ternary system, which means that the positive electrode material is lithium nickel cobalt manganese oxide or lithium nickel cobalt aluminum oxide batteries. According to the different ratios of nickel, cobalt, and manganese, they can be further divided into 111, 532, 622, and 811 types. As the proportion of nickel continues to increase, the energy ratio of the power battery will also increase, which means that the range of the car will correspondingly increase. For lithium batteries, safety, lifespan, cost, and energy density are in a dynamic balance. If the energy density increases, then the other three will inevitably encounter some problems.
The higher the nickel ratio, the poorer the thermal stability of the entire positive electrode material. High nickel batteries may pose safety hazards when exposed to high temperatures, external impacts, and other factors. Gas generation during charging of high nickel batteries can also cause battery swelling, which is a major issue. At the same time, once the 811 battery experiences thermal runaway, the consequences are also quite serious.
In the past, the thermal runaway of lithium iron phosphate batteries only resulted in smoking; The 532 type ternary lithium battery may experience combustion due to thermal runaway. Once the 811 type ternary battery loses its thermal control, it is likely to experience detonation. The pursuit of high energy density is inevitable for development. But for the development of high specific energy power batteries for electric vehicles, safety will always be the top priority.
3 Safety of electric vehicle batteries
For the safety of electric vehicles, this is not something that one or two companies, or one or two link companies need to do. This is a string that every enterprise, from the regulatory level to the entire industry chain, must firmly tighten. The priority is that the product must pass the standards. In previous accidents, electric vehicle products have had more or less problems. Insufficient testing and verification of battery products, deterioration of reliability during vehicle use, and low level of charging safety management technology.
The most noteworthy aspect is that the concept of escape time was first proposed in relevant mandatory national standards. According to regulations, the battery pack or system should provide a thermal event alarm signal (serving as a vehicle thermal event alarm to remind passengers to evacuate) 5 minutes before a single battery thermal runaway causes thermal diffusion and poses a danger to the passenger compartment.
Once there is an alarm signal, the occupants of the vehicle have enough time to escape, thereby minimizing personal safety risks. The most helpless option is to report a danger, and the best strategy is to nip the danger in the bud. Under complex working conditions, electric vehicle batteries inevitably encounter problems over time. Therefore, it is urgent to proactively monitor the safety of electric vehicles.
At present, electric vehicles and fuel vehicles use the same testing system, but there is a lack of full life-cycle testing for electric vehicles worldwide. This makes it difficult for electric vehicles to detect minor issues in a timely manner after prolonged use. The Thousand Mile Embankment was destroyed in an ant colony, and over time, safety issues will eventually erupt.
Several lithium power plants have called for the establishment of a standardized testing system for new energy vehicles, requiring them to undergo professional standardized testing. Unlike gasoline vehicles, the annual inspection of new energy vehicles should establish a corresponding safety inspection system based on the characteristics of high-voltage electrical and power batteries. The establishment of a new energy annual inspection system can ensure the safety of the use of new energy vehicles and to some extent avoid the occurrence of safety accidents.
Many vehicles in the current market are still in use beyond their designed lifespan, which poses safety risks in the later stages. Therefore, it is recommended to establish mandatory scrapping standards for vehicles that exceed the product design requirements in terms of operating time or mileage. In addition, due to the lack of deep understanding of battery characteristics by vehicle manufacturers and the lack of effective analysis of backend monitoring data, many faults could have been early warned through historical data analysis. Therefore, it is recommended that vehicle manufacturers share data with battery companies with energy to achieve early warning and reduce market risks.
In addition to the above measures, Nissan believes that regardless of the driving system used, any vehicle driving on the road needs to undergo appropriate maintenance and upkeep, which is very important. Timely maintenance, regular scrapping or battery replacement can completely eliminate the safety hazards caused by vehicle aging.