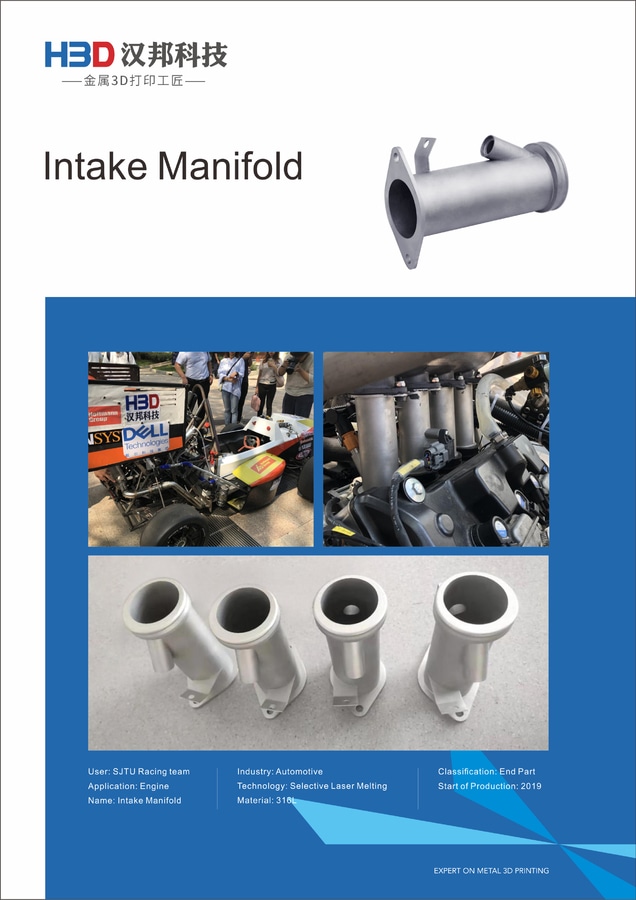
#Industry News
Intake Manifold-by HBD Metal 3D Printer
Automotive-HBD metal 3D printing application
Before using metal 3D printing technology, engineers first machined the main casing and then welded some of the side wall structures together by welding, so the entire fuel injection seat was particularly simple and cumbersome. Existing 3D printing processing features: (1) Adopting the design idea of 3D printing, the structural design has more possibilities, and finally achieves the purpose of lightweight design. (2) The previous manufacturing cycle was 2-3 weeks, and now it is shortened to one week, which speeds up the research and development. Future product design ideas: There are currently four fuel injection seats on a single car, and they are independent of each other. In the future, the design can be simplified, the four independent structures can be reduced to two or even a single integrated structure, and then directly manufactured by 3D printing, so that the structural design of the entire engine is more compact and lighter.
User: SJTU Racing team
Application: Engine
Name: Intake Manifold
Industry: Automotive
Technology: Selective Laser Melting
Material: 316L
Classification: End Part
Start of Production: 2019