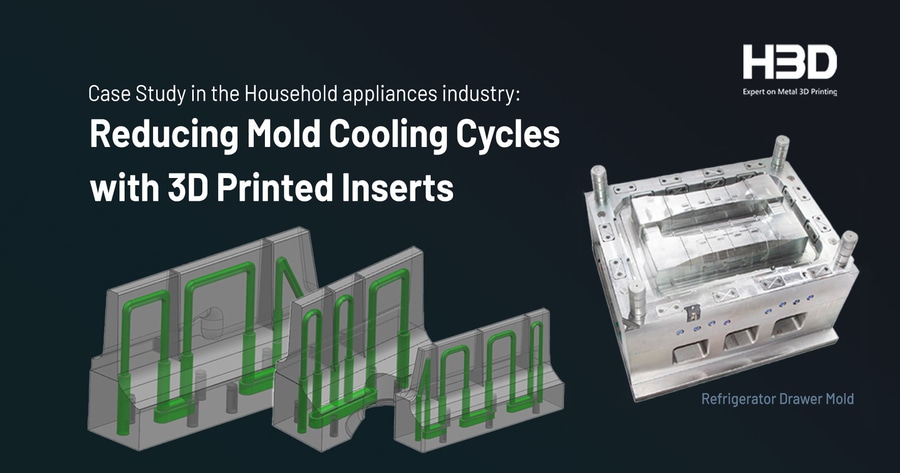
#Industry News
Case Study in the Household appliances industry: Reducing Mold Cooling Cycles with 3D Printed Inserts
Case Study in the Household appliances industry: Reducing Mold Cooling Cycles with 3D Printed Inserts
In this case study, we collaborated with a mold manufacturer to provide an optimization solution for mold cooling efficiency to a well-known household appliance company. During production testing, the household appliance company discovered that the cooling cycle for ribs inside the refrigerator drawer mold lasted as long as 70 seconds, resulting in unstable rubber quality and hindering efficient large-scale production. To address this challenge, the appliance company's collaborative mold manufacturing partner, who is also our partner mold company, proposed the use of metal 3D printing technology to create inserts (width 10mm, height 70mm) at the ribs of the rubber to manufacture molds with innovative waterway designs to enhance mold cooling efficiency and product quality.